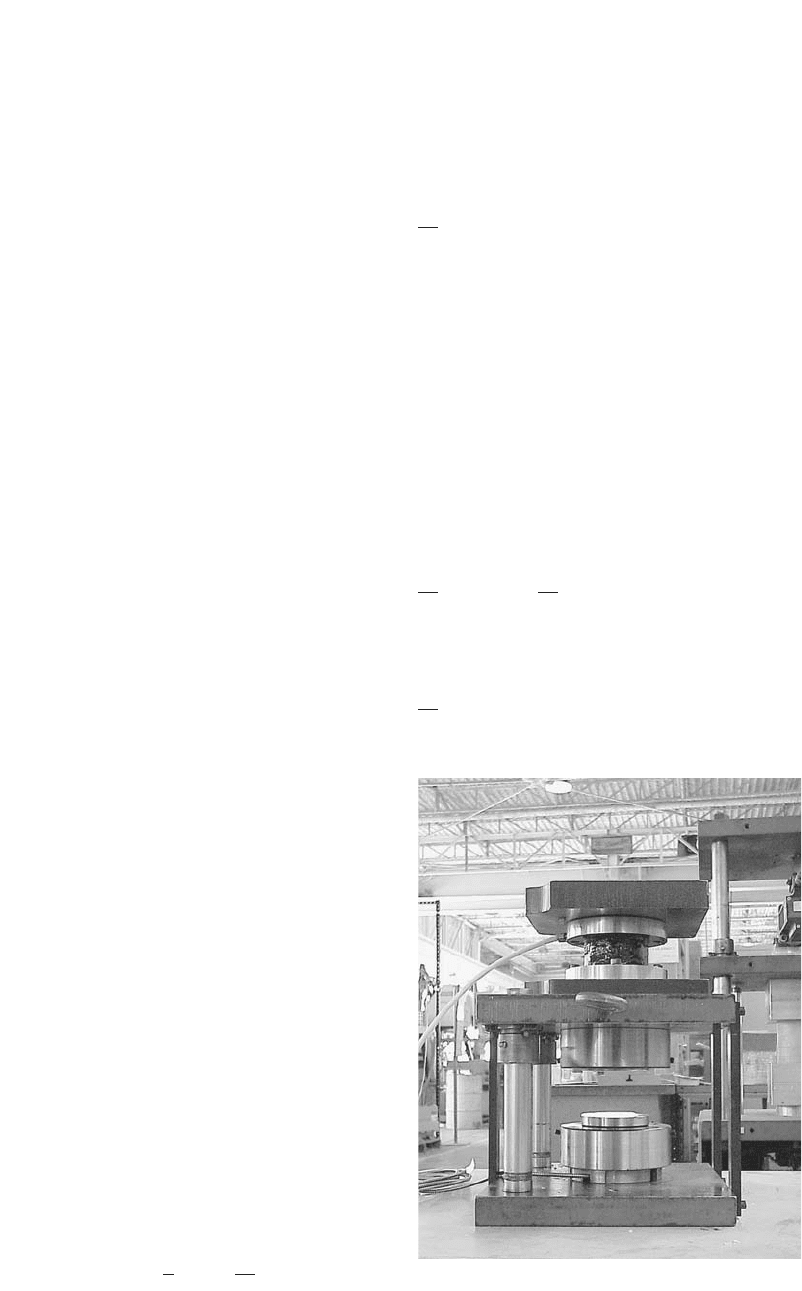
Flow Stress and Forgeability / 27
would result from a drop of 100 ⬚F (55 ⬚C) in
the hot forging temperature (from 1700 to 1600
⬚F, or 925 to 870 ⬚C) is about 40%. The same
temperature drop in the hot working range of
AISI type 4340 steel would result in a 15% in-
crease in the flow stress [Altan et al., 1973].
To be useful in metal forming analyses, the
flow stresses of metals should be determined ex-
perimentally for the strain, strain rate, and tem-
perature conditions that exist during the forming
processes. The most commonly used methods
for determining flow stress are the tensile, uni-
form compression and torsion tests.
4.2 Tensile Test
The tensile test is commonly used for deter-
mining the mechanical properties of metals.
However, the properties determined from this
test are useful for designing components and not
for producing parts by metal forming processes.
The reason for this is that the tensile test data is
valid for relatively small plastic strains. Flow
stress data should be valid for a large range of
plastic strains encountered in metal forming pro-
cesses so that this data is useful in metal forming
analysis.
Two methods of representing flow stress data
are illustrated in Fig. 4.1 [Thomsen et al., 1965].
In the classical engineering stress-strain diagram
(Fig. 4.1a), the stress is obtained by dividing the
instantaneous tensile load, L, by the original
cross-sectional area of the specimen, A
o
. The
stress is then plotted against the engineering
strain, e ⳱ (l ⳮ l
o
)/l
o
. During deformation, the
specimen elongates initially in a uniform fash-
ion. When the load reaches its maximum value,
necking starts and the uniform uniaxial stress
condition ceases to exist. Deformation is then
concentrated only in the neck region while the
rest of the specimen remains rigid.
Figure 4.1(b) illustrates the true stress-strain
representation of the same tensile test data. In
this case, before necking occurs, the following
relationships are valid:
¯r ⳱ true stress (flow stress)
⳱ instantaneous load/instantaneous area
⳱ L/A (Eq 4.2)
and
lA
o
¯e ⳱ true strain ⳱ ln ⳱ ln (Eq 4.3)
冢冣 冢 冣
lA
o
The instantaneous load in tension is given by
L ⳱ The criterion for necking can be for-A¯r.
mulated as the condition that L be maximum or
that:
dL
⳱ 0 (Eq 4.4)
d¯e
Near but slightly before the attainment of max-
imum load, the uniform deformation conditions,
i.e., Eq 4.2 and 4.3 are valid [Thomsen et al.,
1965]. From Eq 4.3:
ⳮ ¯e
A ⳱ A (e)
o
or
ⳮ ¯e
L ⳱ A¯r ⳱ A¯r(e) (Eq 4.5)
o
Combining Eq 4.4 and 4.5 results in:
dL d ¯r
ⳮ ¯e ⳮ¯e
⳱ 0 ⳱ A (e) ⳮ ¯r(e) (Eq 4.6)
o
冢冣
d¯e d¯e
or
d¯r
⳱ ¯r (Eq 4.7)
d¯e
Fig. 4.5 Compression test tooling. [Dixit et al., 2002]