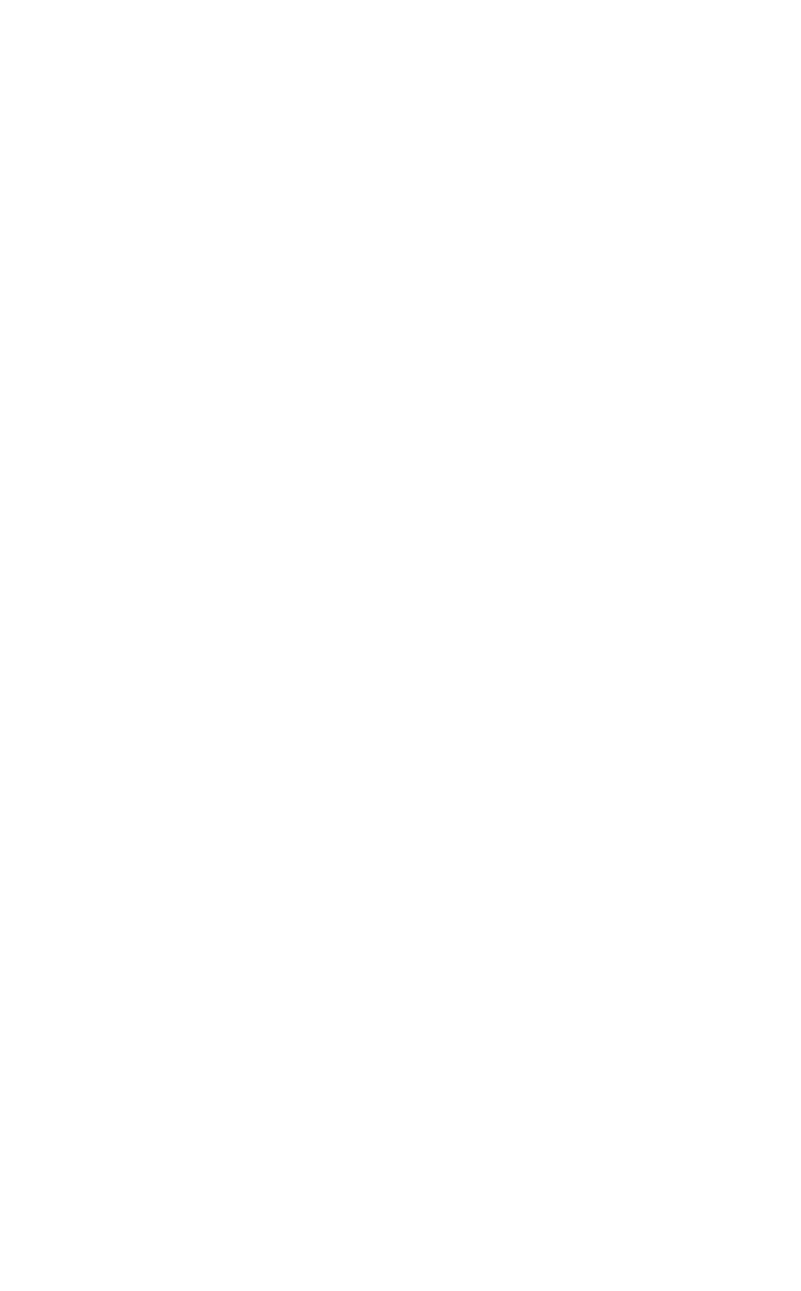
Die Materials and Die Manufacturing / 285
loys are given in the literature [Semiatin et
al., 1981].
21.2.4 Ceramic Dies
Some of the newer nonferrous alloys have
marked improvements over the traditional die
materials (Cr-Mo-V-base steels) used in hot forg-
ing. For example, Nissan Motor Co. is using cer-
met dies in extrusion [Kesavapandian et al.,
2001]. The material is composed of MoB (ce-
ramic) and nickel (metal.) Boron improves resis-
tance to oxidation at high temperatures. The ma-
terial is powder formed and sintered. Die life
improvements over traditional materials is 2 to 1.
Hot forging wear tests [Bramley et al., 1989]
compare silicon-base ceramics to conventional
die steels. Silicon-base ceramics exhibit far less
wear than the conventional die steels. These ma-
terials are very pure, with fine grains and uni-
form microstructures. They have high hardness,
strength, and resistance to mechanical and ther-
mal shock. However, these materials are brittle
and must not be subjected to tensile stresses; in
addition, they are expensive. Therefore, they are
used only in selected applications.
21.2.5 Nickel Aluminides
Nickel aluminides are attractive because they
derive their strength from their ordered micro-
structure instead of heat treatments. Their yield
strength increases with temperature up to about
1560 F (850 C), and they have excellent resis-
tance to oxidation up to 1830 F (1000 C). In-
formation on the composition and properties of
various nickel aluminides is available in the lit-
erature.
[Maddox et al., 1997] documented the results
of a series of performance tests between the
nickel aluminide alloys 221M-T and more tra-
ditional die steels. Whereas H11 and H13 lose
strength and hardness above 1000 F (540 C),
nickel aluminide alloys have improved high-
temperature strength, oxidation resistance, and
thermal stability at temperatures ranging from
1500 to 2300 F (815 to 1260 C). The compo-
sition of this alloy is Ni
3
Al, with additions of
chromium for ductility and resistance to oxida-
tion; molybdenum for strength; zirconium for
strength, resistance to oxidation, weldability,
and castability; and boron for ductility. The alloy
is stronger than Inconel 718 in both tension and
compression. The results of the performance test
are impressive for the nickel aluminide die ma-
terial. For the particular part being forged (at
2300 F, or 1260 C), conventional dies typically
failed after 5000 parts due to erosion, whereas
the nickel aluminide dies lasted for 35,000 parts
(a sevenfold increase). After resinking the cav-
ity, the nickel aluminide dies lasted for 50,000
parts (a tenfold increase). Hardness in the flash
actually also went up due to work hardening.
This alloy keeps its hardness at high tempera-
tures from the cast microstructure and not
through a thermal treatment. Also important is
that, while heat checking was detected in the
dies, it was not important, because of the high
ductility of the material.
21.3 Heat Treatment
Heat treatment of die steels involves the fol-
lowing steps:
1. Austenitizing temperature of a hot work tool
steel ranges from 1830 to 2730 F (1000 to
1500 C). During this phase, the structure of
steel transforms from a ferrite-pearlite struc-
ture to austenite. The dies are held at these
temperatures for a long time, which is called
a “soak” or “hold” time, to convert the entire
structure uniformly to austenite. Carbides or
alloying elements go into solution [Krauss et
al., 1998 and Kesavapandian et al., 2001].
2. After soaking, the dies are quenched in a
quench medium to a temperature below the
transformation temperature. Based on the
cooling rate, the die transforms into different
phases. Martensite is the ideal final structure,
but lower bainite, upper bainite, pearlite, or
retained austenite can be present in the struc-
ture.
3. During tempering, the martensite is tempered
to a tougher structure. This can be done in
several stages to maximize toughness with-
out reducing hardness.
Hardening and tempering temperatures for
various tool steels are available in literature and
from die steel suppliers [Roberts et al., 1980].
21.4 Die and Tool
Materials for Cold Forging
The tooling for cold forging is described in
Chapter 17, “Cold and Warm Forging,” in this
book. The back or pressure plates, which must
have high compressive strength, are made from