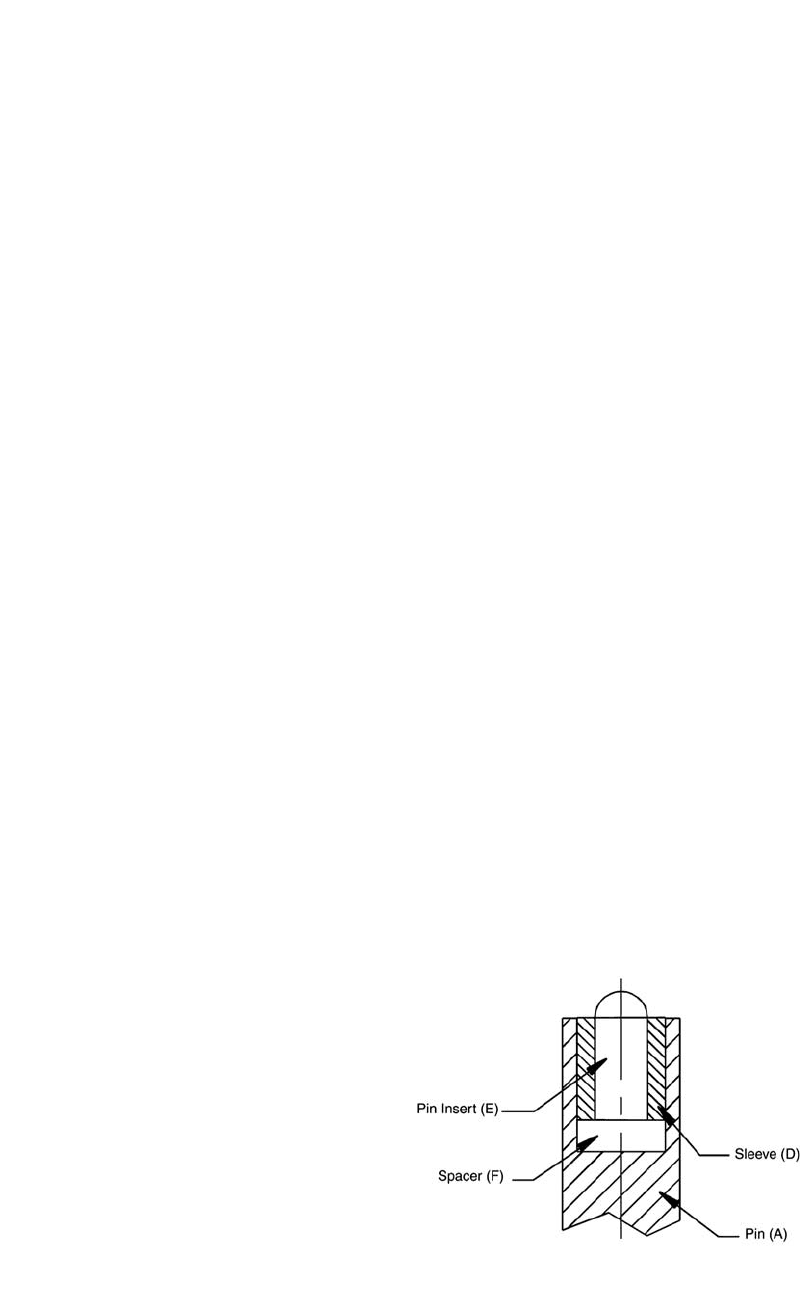
Die Failures in Cold and Hot Forging / 307
are needed in order to reduce die temperatures.
Alternatively, it is also possible to leave one
forging station intermittently empty in order to
provide time for the dies to cool.
In order to produce an economically sound
part with prolonged die life by either cold or hot
forging, a multitude of variables, as discussed
above, must be carefully considered. In partic-
ular, the effect and importance of each variable
based on the nature of the given component must
be assessed.
22.7 Prediction of Die Fatigue
Fracture and Enhancement of
Die Life in Cold Forging Using
Finite-Element Modeling (FEM)
A reliable method to analyze, predict, prevent,
and/or control die fatigue fracture has long been
one of the most important issues in cold forging.
Therefore, a fatigue analysis method that can be
utilized to estimate tool life has been developed
and can be summarized as follows (Fig. 22.10)
[Knoerr et al., 1994, and Matsuda, 2002]:
●
The forging process is simulated using FEM
in order to estimate the tool stresses.
●
The tool stress values are used to complete
an elastic-plastic stress-strain analysis of the
tooling using FEM.
●
The stress-strain analysis is used to perform
a damage analysis and estimate the number
of cycles until fatigue fracture.
If the predicted tool life is insufficient,
changes in the process and tooling design must
be made in order to reduce the loading condi-
tions. A significant increase in tool life can be
achieved by reducing the stresses in the highest
loaded zone below the yield strength of the tool
material. This may be achieved by the following
means [Knoerr et al., 1994]:
●
Change material flow in the die to reduce the
contact stresses on the tool.
●
Redesign the process to avoid drastic
changes in the direction of the material flow,
which usually leads to peaks in the contact
stress.
●
Increase the transition radii to reduce the
notch effect.
●
Split the tooling at the highest loaded zone.
●
Increase the interference of the stress ring.
●
Apply advanced stress ring techniques, such
as strip-wound containers or profiled stress
rings.
Several case studies where this fatigue anal-
ysis method was employed are presented as fol-
lows.
22.7.1 Forward Extrusion—A Case Study
In forward extrusion, fatigue cracks initiate at
the transition radius to the extrusion shoulder
and propagate in the radial direction (Fig.
22.11).
In order to verify the fatigue analysis method
for evaluating tool life, an experimental inves-
tigation of fatigue fracture of forward extrusion
dies, performed at the Institute for Metal Form-
ing (IFUM) at the University of Stuttgart, was
used [Hettig, 1990]. Figure 22.12 shows the
cross section of the forward extrusion die, and
Table 22.2 summarizes the test conditions and
the results obtained. In addition, Table 22.2 sum-
marizes the results obtained from the fatigue
analysis for the same test conditions. As the ta-
ble shows, the predicted die lives were in the
range of those found experimentally. Thus, the
fatigue analysis method was verified.
Table 22.2 illustrates that the die opening an-
gle and the transition radius have a large effect
on the die life. With FEM-based fatigue analy-
sis, this effect is noted quickly and economi-
cally. Also, the FEM-based fatigue analysis eas-
ily determines the location where fatigue
fracture will occur. Figure 22.13 shows the local
plastic zone at the transition radius found during
the FEM-based stress-strain analysis of the die.
Figure 22.13 also shows that the maximum prin-
cipal stresses in this same region are tensile,
Fig. 22.21
Split knockout pin insert design [Hannan et al.,
2001]