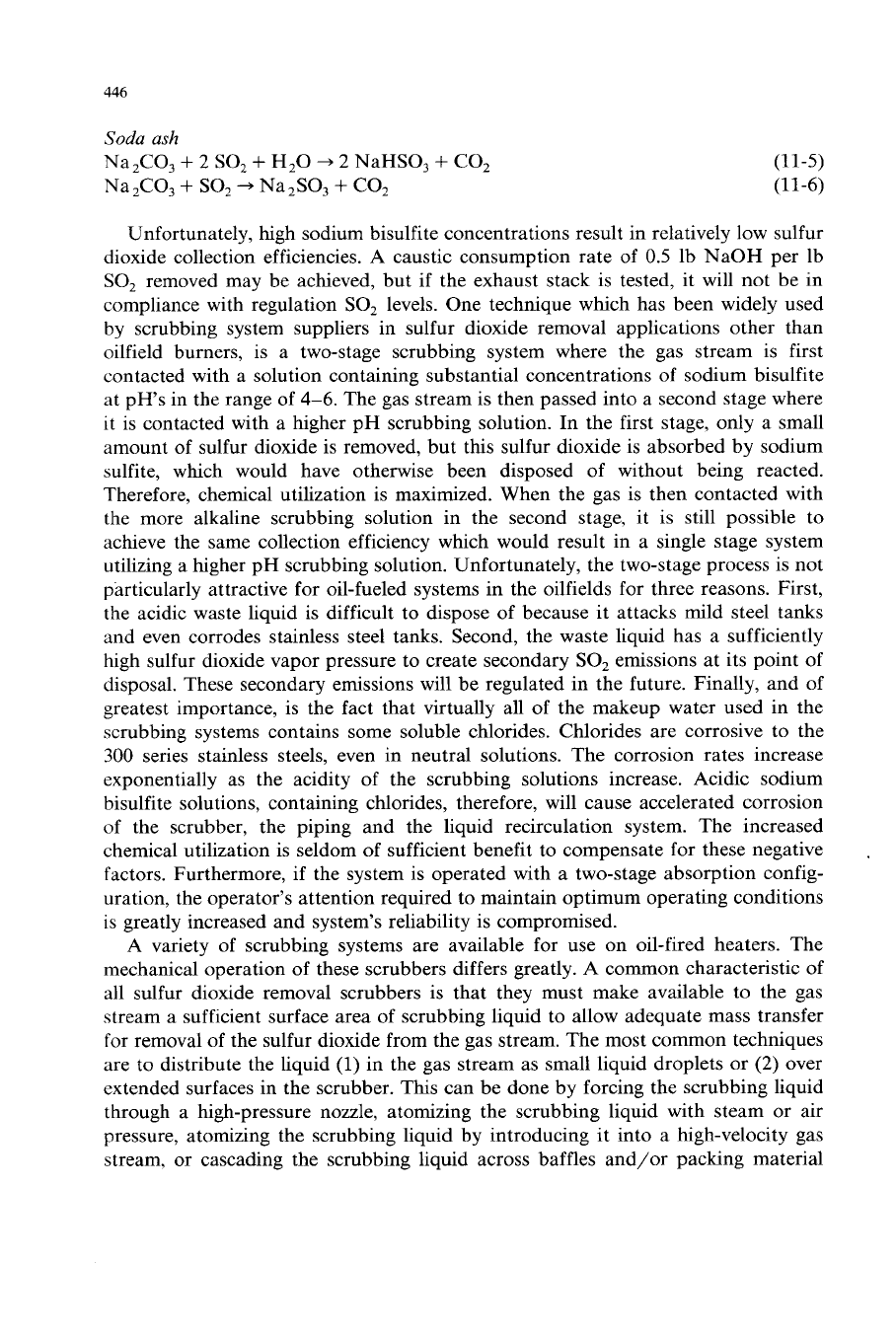
446
Soda
ash
Na,CO,
+
2
SO,
+
H,O
+
2
NaHSO,
+
CO,
Na,CO,
+
SO,
+=
Na,SO,
+
CO,
(11-5)
(11-6)
Unfortunately, high sodium bisulfite concentrations result in relatively low sulfur
dioxide collection efficiencies. A caustic consumption rate of
0.5
Ib NaOH per Ib
SO,
removed may be achieved, but if the exhaust stack is tested, it will not be in
compliance with regulation
SO,
levels. One technique which has been widely used
by scrubbing system suppliers in sulfur dioxide removal applications other than
oilfield burners, is a two-stage scrubbing system where the gas stream is first
contacted with a solution containing substantial concentrations of sodium bisulfite
at pH’s in the range of
4-6.
The gas stream is then passed into a second stage where
it is contacted with a higher pH scrubbing solution. In the first stage, only a small
amount of sulfur dioxide is removed, but this sulfur dioxide is absorbed by sodium
sulfite, which would have otherwise been disposed of without being reacted.
Therefore, chemical utilization is maximized. When the gas is then contacted with
the more alkaline scrubbing solution in the second stage, it is still possible to
acheve the same collection efficiency which would result in a single stage system
utilizing a higher pH scrubbing solution. Unfortunately, the two-stage process is not
particularly attractive for oil-fueled systems in the oilfields for three reasons. First,
the acidic waste liquid is difficult to dispose
of
because it attacks mild steel tanks
and even corrodes stainless steel tanks. Second, the waste liquid has a sufficiently
high sulfur dioxide vapor pressure to create secondary
SO,
emissions at its point of
disposal. These secondary emissions will be regulated in the future. Finally, and of
greatest importance, is the fact that virtually all of the makeup water used in the
scrubbing systems contains some soluble chlorides. Chlorides are corrosive to the
300
series stainless steels, even in neutral solutions. The corrosion rates increase
exponentially as the acidity
of
the scrubbing solutions increase. Acidic sodium
bisulfite solutions, containing chlorides, therefore, will cause accelerated corrosion
of the scrubber, the piping and the liquid recirculation system. The increased
chemical utilization is seldom
of
sufficient benefit to compensate for these negative
factors. Furthermore, if the system is operated with a two-stage absorption config-
uration, the operator’s attention required to maintain optimum operating conditions
is greatly increased and system’s reliability is compromised.
A
variety of scrubbing systems are available for use on oil-fired heaters. The
mechanical operation of these scrubbers differs greatly.
A
common characteristic of
all sulfur dioxide removal scrubbers is that they must make available to the gas
stream a sufficient surface area of scrubbing liquid to allow adequate mass transfer
for removal of the sulfur dioxide from the gas stream. The most common techniques
are to distribute the liquid
(1)
in the gas stream as small liquid droplets
or
(2)
over
extended surfaces in the scrubber. This can be done by forcing the scrubbing liquid
through a high-pressure nozzle, atomizing the scrubbing liquid with steam or air
pressure, atomizing the scrubbing liquid by introducing it into a high-velocity gas
stream, or cascading the scrubbing liquid across baffles and/or packing material