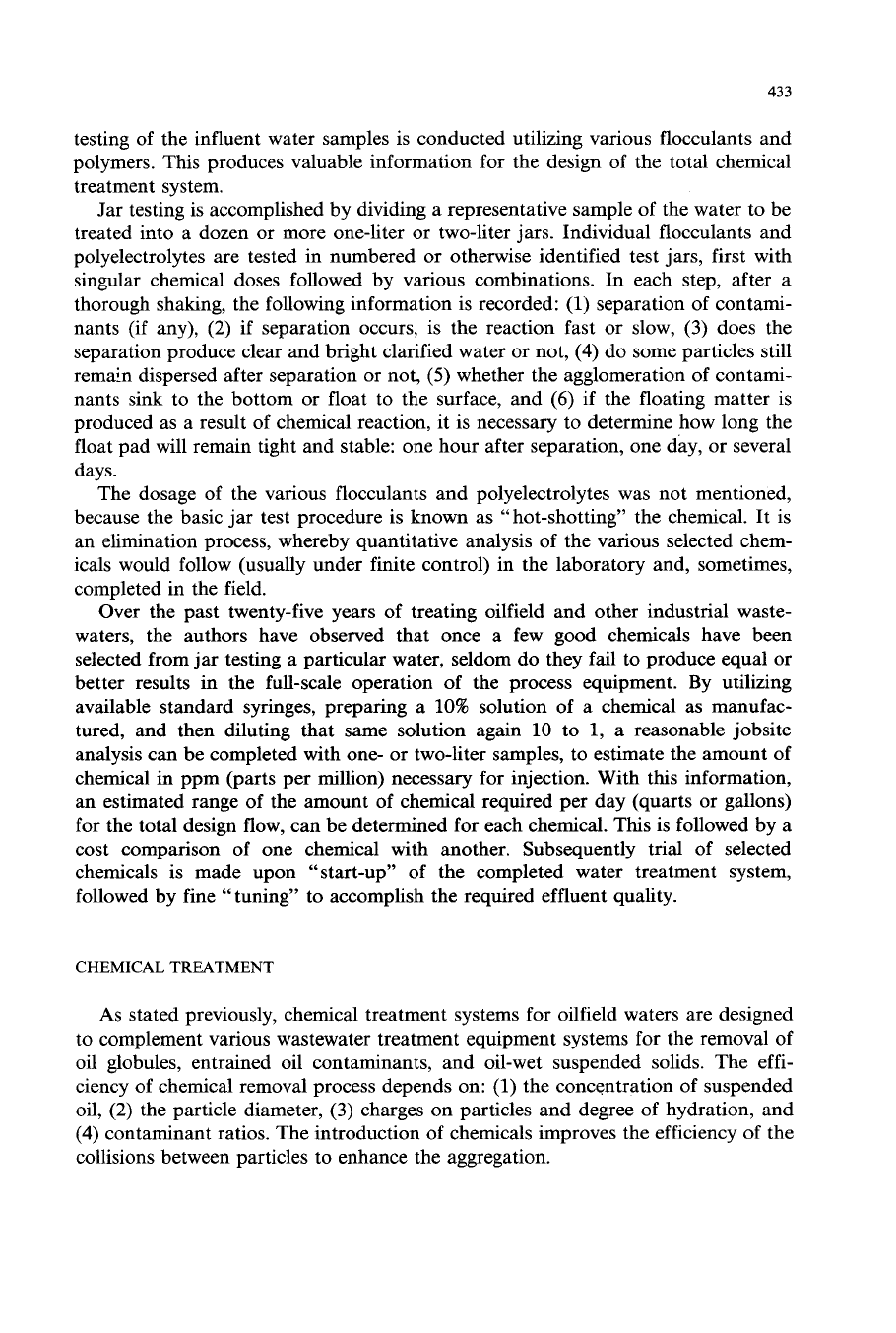
433
testing of the influent water samples is conducted utilizing various flocculants and
polymers. This produces valuable information for the design of the total chemical
treatment system.
Jar testing is accomplished by dividing a representative sample of the water to be
treated into a dozen or more one-liter or two-liter jars. Individual flocculants and
polyelectrolytes are tested in numbered or otherwise identified test jars, first with
singular chemical doses followed by various combinations. In each step, after a
thorough shaking, the following information is recorded:
(1)
separation of contami-
nants (if any),
(2)
if separation occurs, is the reaction fast or slow,
(3)
does the
separation produce clear and bright clarified water or not,
(4)
do some particles still
remain dispersed after separation or not,
(5)
whether the agglomeration of contami-
nants sink to the bottom or float to the surface, and
(6)
if the floating matter is
produced as a result of chemical reaction, it is necessary to determine how long the
float pad will remain tight and stable: one hour after separation, one day, or several
days.
The dosage of the various flocculants and polyelectrolytes was not mentioned,
because the basic jar test procedure is known as “hot-shotting” the chemical. It is
an elimination process, whereby quantitative analysis of the various selected chem-
icals would follow (usually under finite control) in the laboratory and, sometimes,
completed in the field.
Over the past twenty-five years of treating oilfield and other industrial waste-
waters, the authors have observed that once a few good chemicals have been
selected from jar testing a particular water, seldom do they fail to produce equal or
better results in the full-scale operation of the process equipment. By utilizing
available standard syringes, preparing a
10%
solution of a chemical as manufac-
tured, and then diluting that same solution again
10
to
1,
a reasonable jobsite
analysis can be completed with one- or two-liter samples, to estimate the amount of
chemical in ppm (parts per million) necessary for injection. With this information,
an estimated range of the amount of chemical required per day (quarts or gallons)
for the total design flow, can be determined for each chemical. This is followed by a
cost comparison of one chemical with another. Subsequently trial
of
selected
chemicals is made upon “start-up” of the completed water treatment system,
followed by fine “tuning” to accomplish the required effluent quality.
CHEMICAL TREATMENT
As
stated previously, chemical treatment systems for oilfield waters are designed
to complement various wastewater treatment equipment systems for the removal of
oil globules, entrained oil contaminants, and oil-wet suspended solids. The effi-
ciency of chemical removal process depends on:
(1)
the concentration of suspended
oil,
(2)
the particle diameter,
(3)
charges on particles and degree of hydration, and
(4) contaminant ratios. The introduction of chemicals improves the efficiency of the
collisions between particles to enhance the aggregation.