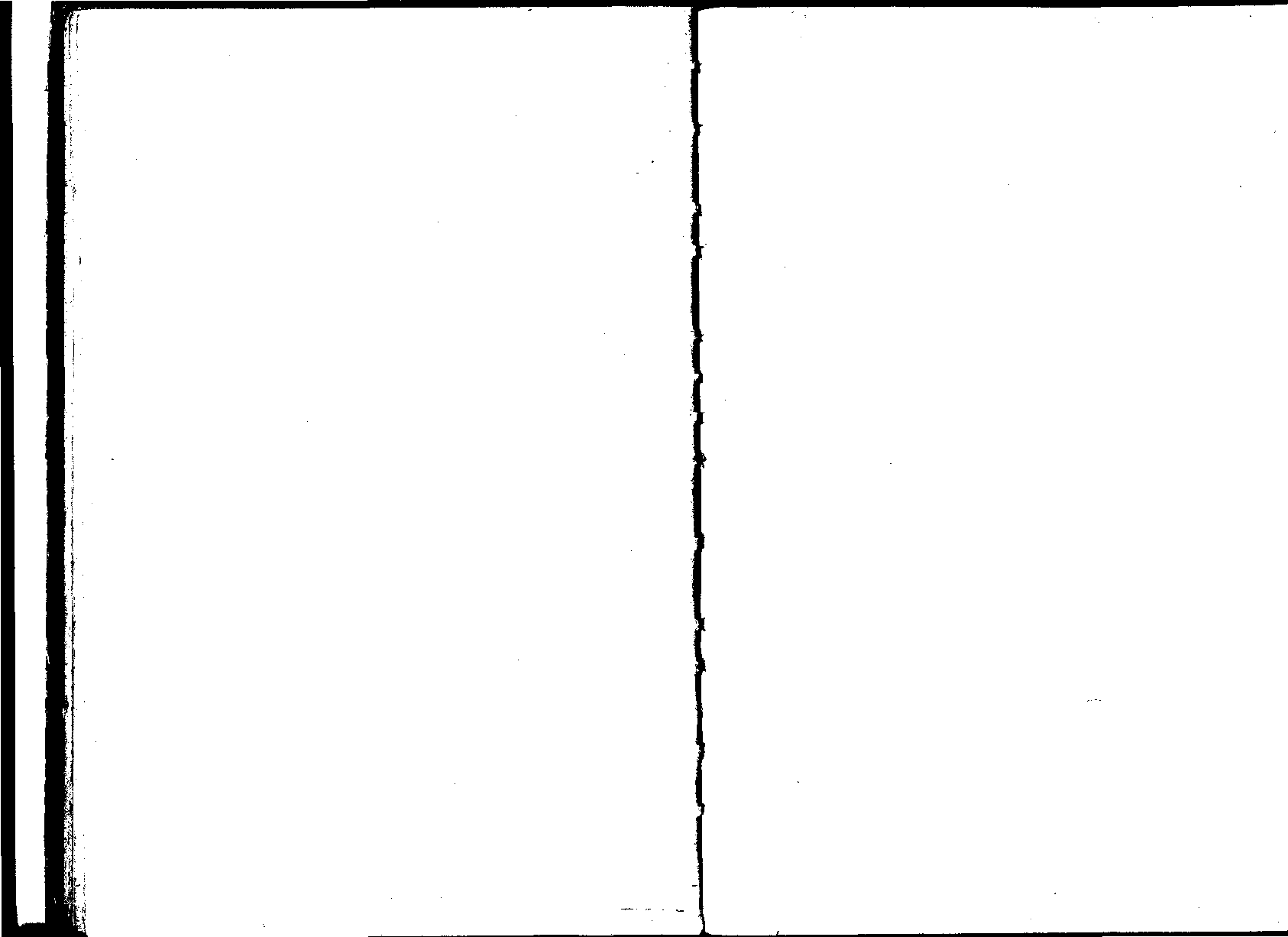
ют струей холодной ЕОДЫ, просушивают сжатым
воздухом
и
облуча-
ют ультрафиолетовыми лучами (ртутно-кварцевой лампой ПРК2
или ПРК4). По зеленовато-желтому свечению флюоресцирующей
жидкости, выходящей из трещины, выявляют дефекты в детали.
Сведения о деталях, подлежащих ремонту и замене, заносят
в ведомость дефектов на ремонт оборудования и узлов газового кра-
на, которую составляет инженер по ремонту газовых кранов при
участии бригадира ремонтной бригады и мастера по обслуживанию
газовых кранов. При разбраковке детали делят- на три группы: год-
ные для дальнейшей эксплуатации, требующие ремонта или восста-
новления и подлежащие замене. Ремонту подвергают сложные в из-
готовлении детали, восстановление которых обходится значительно
дешевле, чем замена новыми (пробки, шпиндели, штоки и т. А-)->
Ремонтируемая деталь должна иметь значительный запас прочности,
позволяющий восстанавливать или изменять размеры сопрягаемых
поверхностей (по системе ремонтных размеров), ие снижая, а в ряде
случаев повышая их долговечность и сохраняя или улучшая эксплу-
атационные качества сборочной единицы. Детали заменяют в следу-
ющих случаях: уменьшение размеров в результате износа нарушает
нормальную работу механизма или вызывает дальнейший интенсив-
ный износ, который приводит к выходу механизма из строя; детали
имеют предельный износ или износ менее допустимого; согласно рас-
чету детали не дослужат до очередного ремонта (срок службы рас-
считывают с учетом предельного износа и интенсивности их изна-
шивания во время эксплуатации).
При дефектовке детали маркируют. Детали присваивают поряд-
ковый номер, под которым она числится в ведомости дефектов, и
инвентарный номер газового крана. Это облегчает выполнение даль-
нейших операций. Маркировку выполняют клеймением (обозначения
набивают на нерабочих поверхностях незакаленных деталей), крас-
кой, кислотой. Для этих целей используют также бирки, электро-
граф. При маркировке незакаленных деталей можно пользоваться
резиновым штампом, который смачивают в растворе, состоящем из
40% азотной кислоты, 20% уксусной кислоты и 40% воды, закален-
ных деталей — в растворе, состоящем из 10% азотной кислоты,
30% уксусной кислоты, 5% спирта и 55% воды. Смоченный штамп
накладывают на нерабочий участок маркируемой детали. После вы-
держки в течение 1—2 мин поверхность нейтрализуют, протирая там-
поном, смоченным в растворе кальцинированной соды.
Детали, которые подлежат замене, хранят до окончания ремонта,
так как они могут понадобиться для составления чертежей или изго-
товления образцов новых деталей.
ВОССТАНОВЛЕНИЕ ДЕТАЛЕЙ
Изнашивание деталей нередко приводит к нарушению посадки
в сопряжении: увеличиваются зазоры и уменьшаются первоначаль-
ные натяги, изменяется форма поверхностей. Такие детали при ре-
монте восстанавливают разными способами. Стоимость восстановле-
ния обычно составляет 15—40% стоимости новых деталей. Восста-
60
новленная деталь должна обладать теми же качествами, что и новая,
быть достаточно долговечной и надежной в эксплуатации.
Способ восстановления деталей следует выбирать на основе
комплексного анализа технической и экономической целесообразно-
сти их применения. При этом в каждом конкретном случае учитыва-
ют условия работы деталей сопряжения в кране (характер сопряже-
ния, величину и характер действующих нагрузок, скорость взаимно-
го перемещения деталей сопряжения с подвижной посадкой, условия
смазки деталей сопряжения с подвижней посадкой), величину и ха-
рактер износа, прочность детали к моменту ремонта, требования
технических условий на восстановление; конструкции, материал и
вид термической обработки, наличие ремонтных средств, число одно-
типных деталей с одинаковым износом, подлежащих одновременному
восстановлению.
Факторы, влияющие на выбор оптимального технологического
процесса восстановления и упрочнения детали, следующие: сравни-
тельная износостойкость и усталостная прочность, длительность пре-
бывания деталей в ремонте (трудоемкость), дефицитность материа-
лов и затраты на них, размер производственных затрат на восста-
новление детали и сопряжения, относительная себестоимость вос-
становления детали и сопряжения в целом. Основной показатель
оценки экономической эффективности восстановления изношенных
деталей и определения целесообразности применения того или иного
способа восстановления и упрочнения — относительная себестои-
мость, т. е. себестоимость восстановления детали, отнесенная к сро-
ку службы ее после ремонта. Этот показатель является наиболее
комплексным и обобщающим, так как он отражает не только все
элементы затрат, но и износостойкость деталей после их восстанов-
ления. Немаловажное значение имеют данные о продолжительности
и трудоемкости технологического процесса, примененных материалах
и затратах на них.
Для обоснованного выбора способов восстановления деталей,
обеспечивающих требуемую долговечность, необходимо изучить усло-
вия работы типовых деталей механизмов, иметь данные о физико-
механических свойствах и работоспособности материалов, применя-
емых для восстановления изношенных деталей до заданных разме-
ров. От степени износа деталей крана зависит его работоспособность,
которую характеризуют герметичность затвора, минимальное время
его перестановки, безотказность в работе силового привода и систе-
мы управления.
При ремонтах широко используют следующие способы восстанов-
ления изношенных деталей: механическую и слесарную обработку,
сварку, наплавку, металлизацию, хромирование, никелирование, ос-
таливание, склеивание, упрочнение поверхностей деталей и восста-
новление их формы под давлением, восстановление полимерными ма-
териалами, химическую обработку и др. Механическая или слесар-
ная обработка необходима для восстановления посадок сопряжен-
ных деталей, устранения овальности или конусности их поверхно-
стей, обеспечения требуемой чистоты обработки. Этим способом
61
файл скачан с www.turbinist.ru