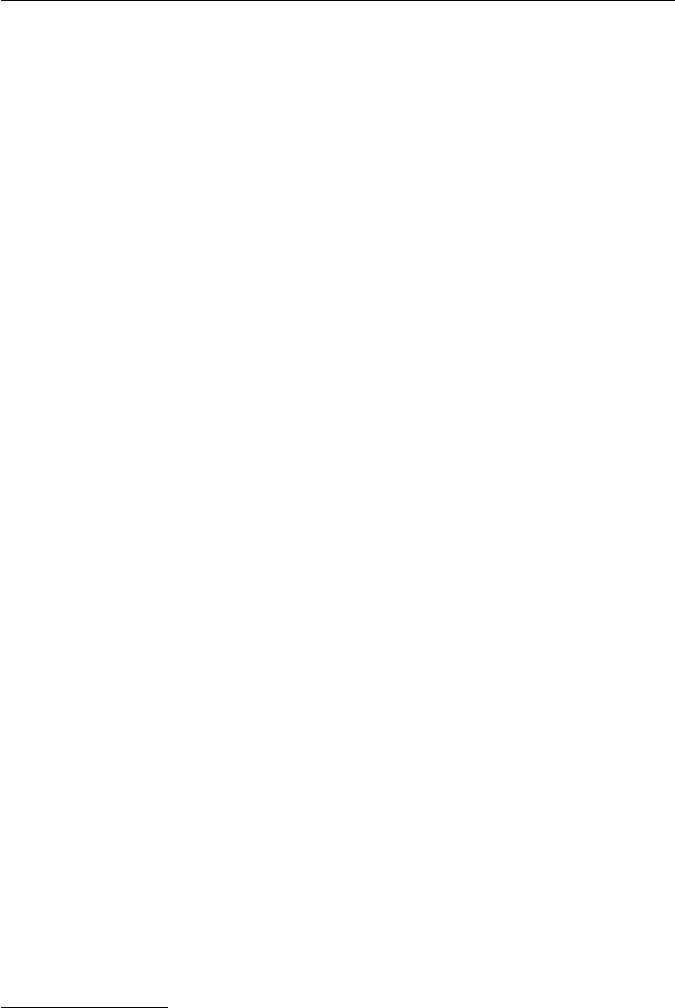
82 CHAPTER 4 EFFECTS OF ALLOYING ELEMENTS ON FE–C ALLOYS
allow even higher resolution.
4
In this way the systems Fe–Mn–C and Fe–
Cr–C have been examined, and partition has been found at temperatures as
low as 550
◦
C.
An approach to the pearlite reaction, similar to that described earlier for
the ferrite reaction, is to distinguish two modes of growth, a partition local
equilibrium and a non-partition local equilibrium situation,
5
which are both
temperature and composition dependent. Elements which favour the forma-
tion of austenite, and so depress the euctectoid temperature, and also have
low solubilities in cementite, e.g. Ni, will encourage the non-partitioning reac-
tion.Those elements which are strong ferrite formers and consequently raise the
eutectoid temperature, as well as being soluble in cementite,are likely to exhibit
the partitioning type of reaction at the higher transformation temperature, e.g.
Cr, Mo, Si. The growth of pearlite in the non-partitioning case is probably con-
trolled by volume diffusion of carbon in austenite, but this diffusivity is reduced
by the presence of other alloying elements, in part accounting for the observed
effect of elements such as Ni on the pearlite growth rate. Where partitioning
of X takes place, the diffusivity of the alloying element in austenite must be a
limiting factor.
Whatever the alloying element distribution is at the growing interface, sub-
sequent redistribution between the ferrite and the cementite takes place, i.e.
those elements with substantial solubility in cementite (carbide formers) will
diffuse into that phase and the non-carbide formers will not. In this way the
composition of cementite can vary over wide limits, e.g. manganese is very sol-
uble in Fe
3
C; up to 20% of the iron atoms can be replaced by chromium, while
vanadium will replace 10% and molybdenum only 4%. The change in compos-
ition of cementite, while not affecting the crystal structure, will influence, e.g.,
the pearlite interlamellar spacing, the detailed morphology and the tendency to
spheroidize.
Once the alloying element concentration reaches a critical level, the cemen-
tite will be replaced by another carbide phase. For example, in a chromium,
tungsten or molybdenum steel, the complex cubic M
23
C
6
carbide can form,
where M can include iron, chromium, molybdenum or tungsten (Figs 4.10 and
4.11). This change in the carbide phase does not necessarily alter the basic
pearlitic morphology and consequently alloy pearlites are obtained in which
an alloy carbide is associated with ferrite (Fig. 4.11). These pearlites occur
only in medium and highly alloyed steels, usually at the highest transformation
temperatures. At lower transformation temperatures in the same steel, cemen-
titic pearlite may still form because of the inadequate diffusion of the alloying
element.
4
Williams, P. R., Miller, M. K. and Smith, G. D. W., Solid–Solid Phase Transformations,TMS-
AIME, Pennsylvania, p. 813, 1981.
5
Coates, D. E., Metallurgical Transactions 4, 2313, 1973.