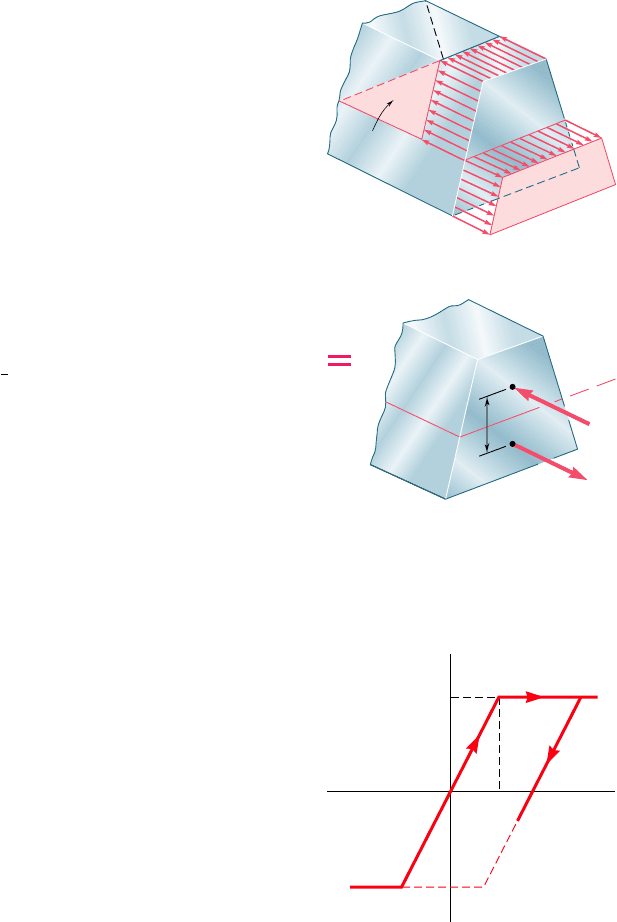
Apago PDF Enhancer
261
cross section is not symmetric with respect to that axis. To locate
the neutral axis, we consider the resultant R
1
of the elementary
compressive forces exerted on the portion A
1
of the cross section
located above the neutral axis, and the resultant R
2
of the tensile
forces exerted on the portion A
2
located below the neutral axis
(Fig. 4.39b). Since the forces R
1
and R
2
form a couple equivalent
to the couple applied to the member, they must have the same
magnitude. We have therefore R
1
5 R
2
, or A
1
s
Y
5 A
2
s
Y
, from
which we conclude that A
1
5 A
2
. In other words, the neutral axis
divides the cross section into portions of equal areas. Note that the
axis obtained in this fashion will not, in general, be a centroidal axis
of the section.
We also observe that the lines of action of the resultants R
1
and
R
2
pass through the centroids C
1
and C
2
of the two portions we have
just defined. Denoting by d the distance between C
1
and C
2
, and by
A the total area of the cross section, we express the plastic moment
of the member as
M
5 1
1
2
As
Y
2 d
An example of the actual computation of the plastic moment of
a member with only one plane of symmetry is given in Sample
Prob. 4.6.
*4.11 RESIDUAL STRESSES
We saw in the preceding sections that plastic zones will develop in
a member made of an elastoplastic material if the bending moment
is large enough. When the bending moment is decreased back to
zero, the corresponding reduction in stress and strain at any given
point can be represented by a straight line on the stress-strain dia-
gram, as shown in Fig. 4.40. As you will see presently, the final value
of the stress at a point will not, in general, be zero. There will be a
residual stress at most points, and that stress may or may not have
the same sign as the maximum stress reached at the end of the load-
ing phase.
Since the linear relation between s
x
and P
x
applies at all
points of the member during the unloading phase, Eq. (4.16) can be
used to obtain the change in stress at any given point. In other words,
the unloading phase can be handled by assuming the member to be
fully elastic.
The residual stresses are obtained by applying the principle of
superposition in a manner similar to that described in Sec. 2.20 for
an axial centric loading and used again in Sec. 3.11 for torsion. We
consider, on one hand, the stresses due to the application of the
given bending moment M and, on the other, the reverse stresses due
to the equal and opposite bending moment 2M that is applied to
unload the member. The first group of stresses reflect the elastoplas-
tic behavior of the material during the loading phase, and the second
group the linear behavior of the same material during the unloading
phase. Adding the two groups of stresses, we obtain the distribution
of residual stresses in the member.
4.11 Residual Stresses
Y
Neutral
surface
(a)
(b)
R
2
C
1
C
2
A
2
A
1
d
R
1
N.A.
Y
Fig. 4.39 Nonsymmetrical beam
subject to plastic moment.
Y
Y
x
x
Y
Fig. 4.40 Elastoplastic material
stress-strain diagram.
bee80288_ch04_220-313.indd Page 261 10/26/10 4:29:34 PM user-f499bee80288_ch04_220-313.indd Page 261 10/26/10 4:29:34 PM user-f499 /Volumes/201/MHDQ251/bee80288_disk1of1/0073380288/bee80288_pagefiles/Volumes/201/MHDQ251/bee80288_disk1of1/0073380288/bee80288_pagefiles