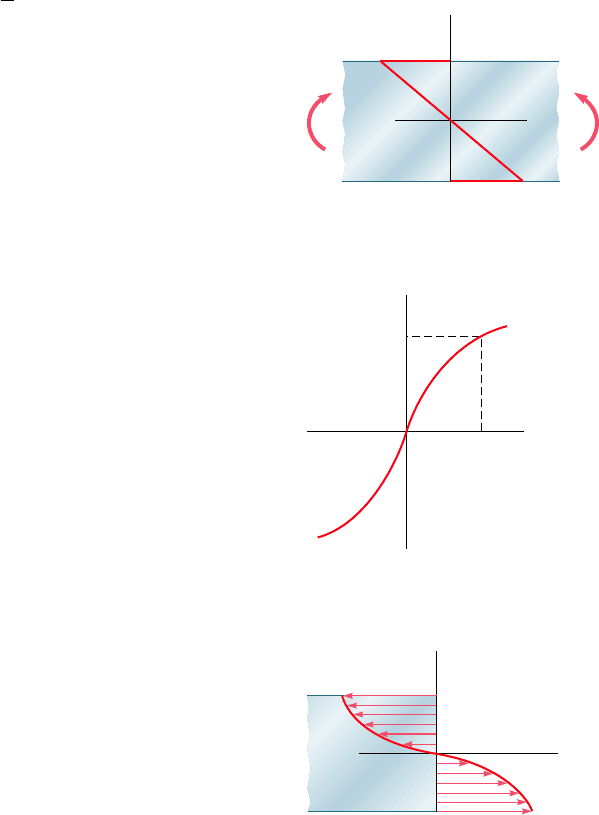
Apago PDF Enhancer
255
*4.8 PLASTIC DEFORMATIONS
When we derived the fundamental relation s
x
5 2MyyI in Sec. 4.4,
we assumed that Hooke’s law applied throughout the member. If the
yield strength is exceeded in some portion of the member, or if the
material involved is a brittle material with a nonlinear stress-strain
diagram, this relation ceases to be valid. The purpose of this section
is to develop a more general method for the determination of the
distribution of stresses in a member in pure bending, which can be
used when Hooke’s law does not apply.
We first recall that no specific stress-strain relationship was
assumed in Sec. 4.3, when we proved that the normal strain P
x
varies
linearly with the distance y from the neutral surface. Thus, we can
still use this property in our present analysis and write
P
x
52
y
P
m
(4.10)
where y represents the distance of the point considered from the
neutral surface, and c the maximum value of y.
However, we cannot assume anymore that, in a given section,
the neutral axis passes through the centroid of that section, since
this property was derived in Sec. 4.4 under the assumption of elastic
deformations. In general, the neutral axis must be located by trial
and error, until a distribution of stresses has been found, that satis-
fies Eqs. (4.1) and (4.3) of Sec. 4.2. However, in the particular case
of a member possessing both a vertical and a horizontal plane of
symmetry, and made of a material characterized by the same stress-
strain relation in tension and in compression, the neutral axis will
coincide with the horizontal axis of symmetry of the section. Indeed,
the properties of the material require that the stresses be symmetric
with respect to the neutral axis, i.e., with respect to some horizontal
axis, and it is clear that this condition will be met, and Eq. (4.1)
satisfied at the same time, only if that axis is the horizontal axis of
symmetry itself.
Our analysis will first be limited to the special case we have
just described. The distance y in Eq. (4.10) is thus measured from
the horizontal axis of symmetry z of the cross section, and the dis-
tribution of strain P
x
is linear and symmetric with respect to that axis
(Fig. 4.30). On the other hand, the stress-strain curve is symmetric
with respect to the origin of coordinates (Fig. 4.31).
The distribution of stresses in the cross section of the member,
i.e., the plot of s
x
versus y, is obtained as follows. Assuming that s
max
has been specified, we first determine the corresponding value of P
m
from the stress-strain diagram and carry this value into Eq. (4.10).
Then, for each value of y, we determine the corresponding value of P
x
from Eq. (4.10) or Fig. 4.30, and obtain from the stress-strain diagram
of Fig. 4.31 the stress s
x
corresponding to this value of P
x
. Plotting s
x
against y yields the desired distribution of stresses (Fig. 4.32).
We now recall that, when we derived Eq. (4.3) in Sec. 4.2, we
assumed no particular relation between stress and strain. We can there-
fore use Eq. (4.3) to determine the bending moment M corresponding
to the stress distribution obtained in Fig. 4.32. Considering the particular
4.8 Plastic Deformations
z
– c
–
m
m
x
MM'
y
c
Fig. 4.30 Linear strain distribution in
beam.
0
x
m
x
max
Fig. 4.31 Nonlinear stress-
strain material diagram.
y
c
– c
max
x
Fig. 4.32 Nonlinear stress
distribution in beam.
bee80288_ch04_220-313.indd Page 255 11/11/10 3:03:13 PM user-f499bee80288_ch04_220-313.indd Page 255 11/11/10 3:03:13 PM user-f499 /Users/user-f499/Desktop/Temp Work/Don't Delete Job/MHDQ251:Beer:201/ch04/Users/user-f499/Desktop/Temp Work/Don't Delete Job/MHDQ251:Beer:201/ch04