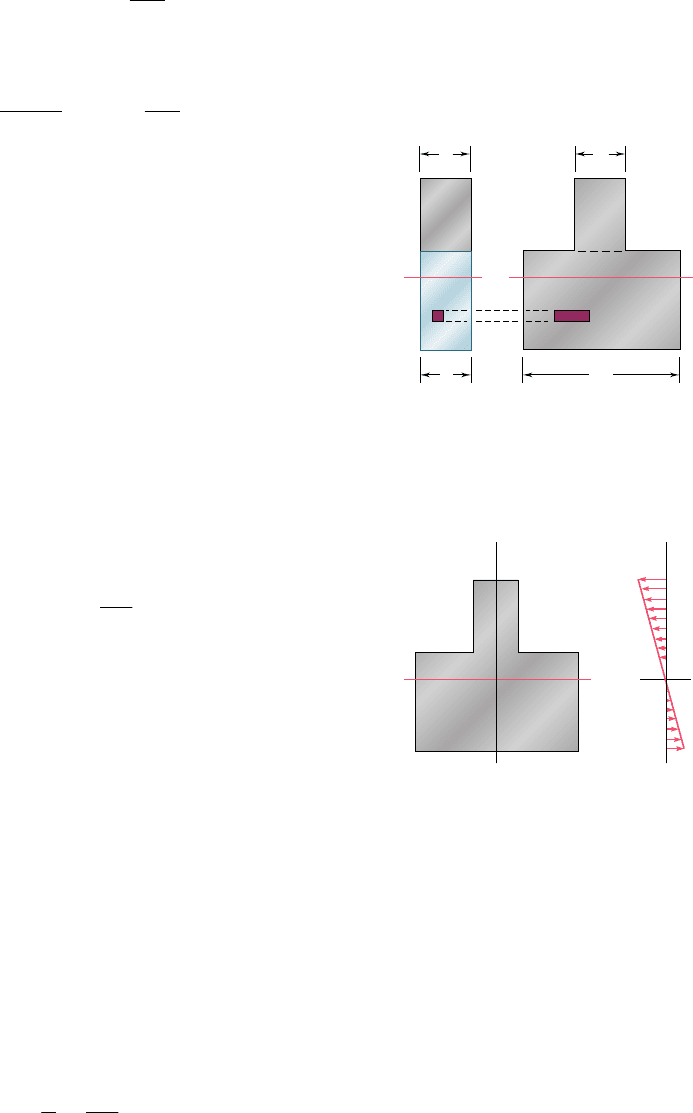
Apago PDF Enhancer
243
while the force dF
2
exerted on an element of the same area dA of the
lower portion is
F
2
5 s
2
dA 52
E
2
y
r
dA (4.26)
But, denoting by n the ratio E
2
yE
1
of the two moduli of elasticity, we can
express dF
2
as
F
2
52
1nE
1
2y
r
dA 52
E
1
y
r
1n dA2 (4.27)
Comparing Eqs. (4.25) and (4.27), we note that the same force dF
2
would be exerted on an element of area n dA of the first material. In
other words, the resistance to bending of the bar would remain the
same if both portions were made of the first material, provided that
the width of each element of the lower portion were multiplied by the
factor n. Note that this widening (if n . 1), or narrowing (if n , 1),
must be effected in a direction parallel to the neutral axis of the sec-
tion, since it is essential that the distance y of each element from the
neutral axis remain the same. The new cross section obtained in this
way is called the transformed section of the member (Fig. 4.22).
Since the transformed section represents the cross section of a
member made of a homogeneous material with a modulus of elastic-
ity E
1
, the method described in Sec. 4.4 can be used to determine
the neutral axis of the section and the normal stress at various points
of the section. The neutral axis will be drawn through the centroid
of the transformed section (Fig. 4.23), and the stress s
x
at any point
of the corresponding fictitious homogeneous member will be obtained
from Eq. (4.16)
s
x
52
My
I
(4.16)
where y is the distance from the neutral surface, and I the moment of
inertia of the transformed section with respect to its centroidal axis.
To obtain the stress s
1
at a point located in the upper portion of
the cross section of the original composite bar, we simply compute the
stress s
x
at the corresponding point of the transformed section. However,
to obtain the stress s
2
at a point in the lower portion of the cross section,
we must multiply by n the stress s
x
computed at the corresponding point
of the transformed section. Indeed, as we saw earlier, the same elemen-
tary force dF
2
is applied to an element of area n dA of the transformed
section and to an element of area dA of the original section. Thus, the
stress s
2
at a point of the original section must be n times larger than
the stress at the corresponding point of the transformed section.
The deformations of a composite member can also be deter-
mined by using the transformed section. We recall that the trans-
formed section represents the cross section of a member, made of a
homogeneous material of modulus E
1
, which deforms in the same
manner as the composite member. Therefore, using Eq. (4.21), we
write that the curvature of the composite member is
1
r
5
M
E
1
I
where I is the moment of inertia of the transformed section with
respect to its neutral axis.
4.6 Bending of Members Made
of Several Materials
b
dA ndA
nbb
b
=
Fig. 4.22 Transformed section for
composite bar.
C
N. A.
x
– —–
My
I
yy
x
Fig. 4.23 Distribution of stresses in
transformed section.
bee80288_ch04_220-313.indd Page 243 10/27/10 5:46:14 PM user-f499bee80288_ch04_220-313.indd Page 243 10/27/10 5:46:14 PM user-f499 /Users/user-f499/Desktop/Temp Work/Don't Delete Job/MHDQ251:Beer:201/ch04/Users/user-f499/Desktop/Temp Work/Don't Delete Job/MHDQ251:Beer:201/ch04