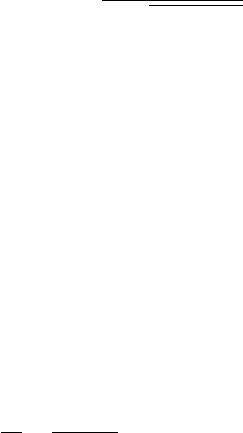
140 Tribology of Metal Cutting
In Eq. (3.24), C, the constant term included as pressure, is singular at each end of the
contact interval. This constant can be found using Eq. (3.21) as
P
s
=
a
s
−a
s
p(x)dx (3.25)
which gives
p
(
x
)
=
P
s
a
s
π
1 −
(
x/a
s
)
2
(3.26)
This is known as the Boussinesq solution [71].
Figure 3.7(b) shows the contact pressure distribution, p(x) calculated using Eq. (3.26).
The contact pressure is singular at the edges of the contact. In reality, the contact pressure
is limited by the elastic limit of the body 2 (the chip), as shown in Fig. 3.7(b). Besides,
the edges of the punch (the tool) are not perfectly sharp.
If the sliding of the punch is allowed so that all points within the contact are slipping
in the same direction, then the shear stress acts over this contact. When the friction
coefficient, µ
f
is constant, this shear stress is defined as
|
q(x)
|
= µ
f
p(x) (3.27)
so that
A
s
π
a
s
−a
s
p
s
(ς)dς
x − ς
+A
s
β
s
µ
f
p(x) = 0 (3.28)
In reality, however, the punch does not have sharp edges as those shown in Fig.3.7(a).
Moreover, its face is not ideally flat. Therefore, the problem of indentation by a general,
convex body should be considered next to approach reality. Figure 3.7(c) shows the rigid
punch having a spherical face of radius r
s
, which is pressed into a viscoelastic material
that can be regarded as semi-infinite, i.e. a half-space. If the contact is sufficiently small
in comparison with the face radius r
s
, then the problem of contact stress distribution
has a direct solution [72]. The distribution of the contact stress for this case is shown
in Fig. 3.7(d). As seen, when x =±a
s1
, the contact pressure becomes zero, and when
x = 0, this pressure is maximum.
The next step is to start building a model which is closer to the real conditions of the
tool–chip interface. Figure 3.8 shows the following essential features of this interface:
• The resultant cutting force R does not intersect the middle point of the tool–chip
contact length OB. Rather, the line of its action is shifted toward the tool point O,
which represents the projection of the cutting edge.