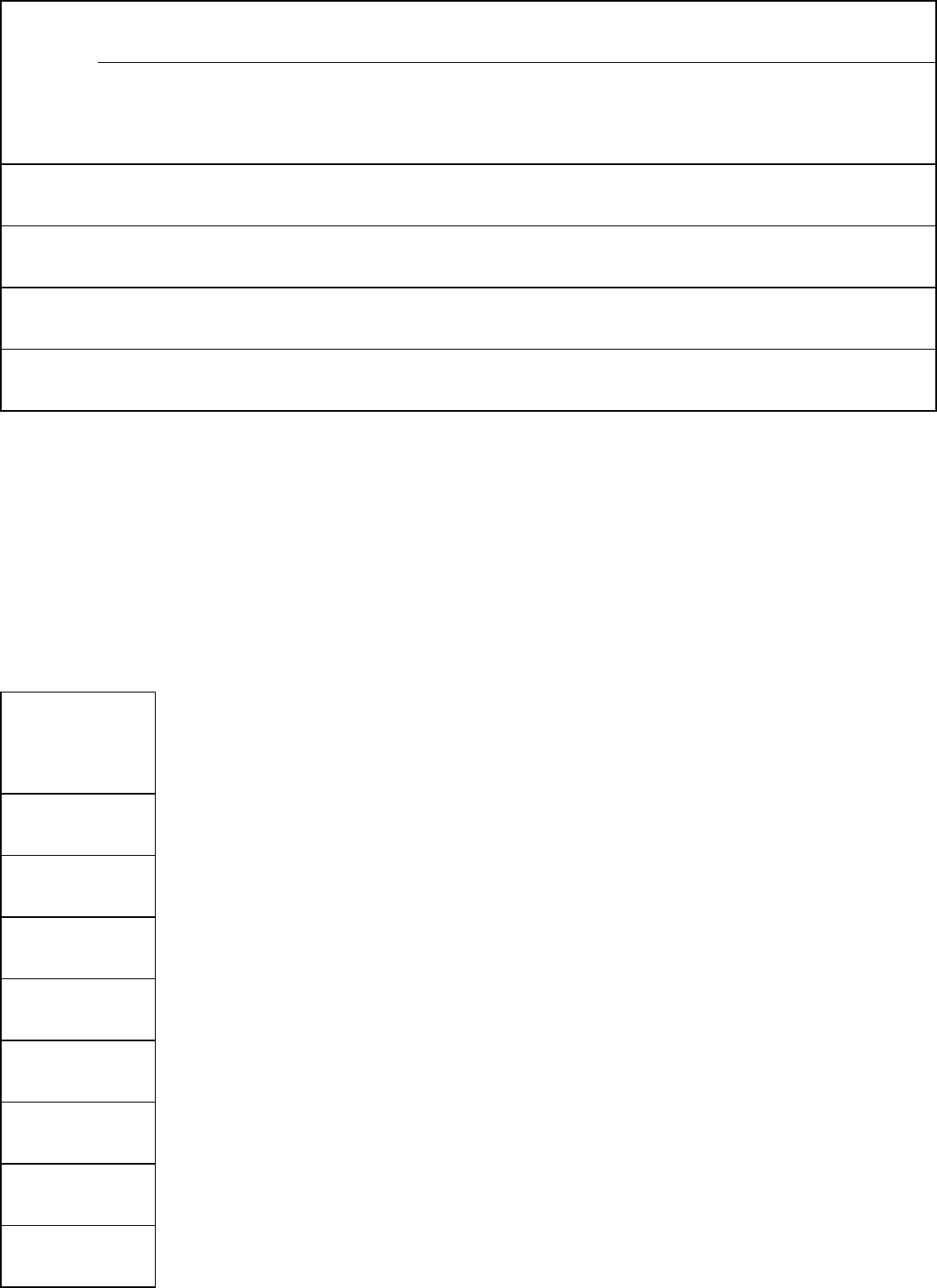
Correction factor for workpiece with diameter of: Observed
reading
3.175 mm
(0.125 in.)
6.350 mm
(0.250 in.)
9.525 mm
(0.375 in.)
12.700 mm
(0.500 in.)
15.875 mm
(0.625 in.)
19.050 mm
(0.750 in.)
22.225 mm
(0.875 in.)
25.400 mm
(1.000 in.)
55 3.5 2.0 1.5 1.0 1.0 0.5 … 0.5
50 3.5 2.0 1.5 1.0 1.0 1.0 … 0.5
45 4.0 2.5 2.0 1.0 1.0 1.0 … 1.0
40 4.5 3.0 2.0 1.5 1.0 1.0 … 1.0
Note: These correction factors are added to the dial-gage reading when hardness testing on the outer (convex) surface and
subtracted when testing on the inner (concave) surface. The values are approximate only and represent the averages, to
the nearest half Rockwell number, of numerous actual observations by different investigators, as well as mathematical
analyses of the same problem. The accuracy of tests on cylindrical workpieces will be seriously affected by alignment of
elevating screw, V-anvil, and indenters, and by surface finish and straightness of the cylinders.
The method recommended by the International Organization for Standardization for correcting Vickers hardness values
taken on spherical or cylindrical surfaces is given in Tables 5, 6, and 7. These tables give correction factors to be applied
to Vickers hardness values when testing on curved surfaces. The correction factors are tabulated in terms of the ratio of
the mean diagonal d of the indentation to the diameter D of the sphere or cylinder.
Table 5 Correction factors for use in Vickers hardness tests made on spherical surfaces
d/D Correction
factor
Convex surface
0.004 0.995
0.009 0.990
0.013 0.985
0.018 0.980
0.023 0.975
0.028 0.970
0.033 0.965