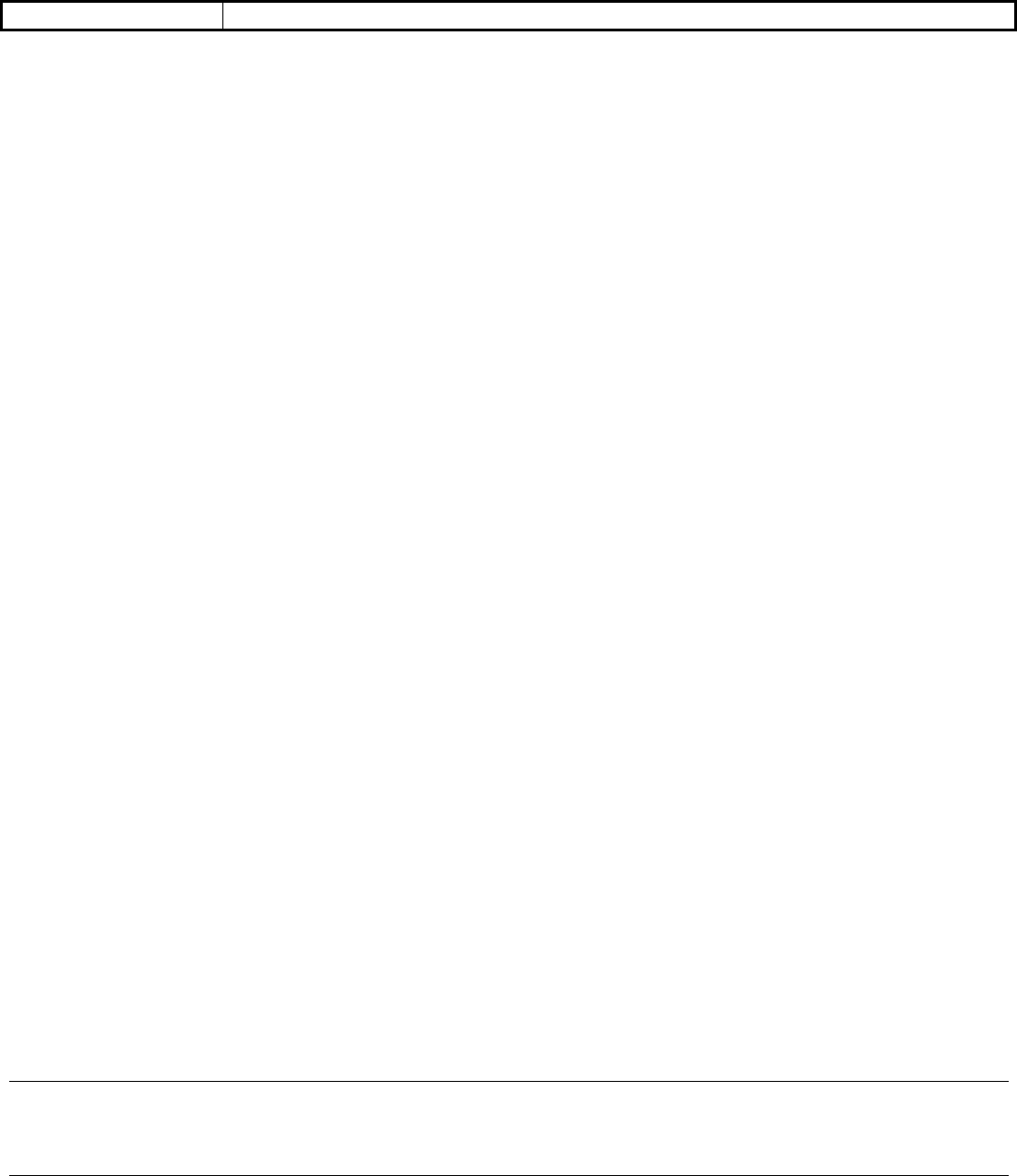
random pattern of fine scratches or gouges
The descriptions given in the “Characteristics” column of Table 1 suggest that the use of wear terminology is
not without ambiguities. It is therefore important, when discussing or reporting on wear problems, to describe
the phenomena sufficiently well so that terminology ambiguities are avoided. Wear problems can be further
complicated by environmental interactions, such as oxidation or other surface chemical reactions, which occur
along with wear. In fact, some wear classification schemes list oxidational or chemical wear as major forms of
wear. Tests for most of the important forms of wear listed in Table 1 are described in this section. Sources for
information regarding impact wear, polishing wear, and other types not covered here are listed in the
bibliography.
Abrasive wear is one of the most economically important types of wear. The cost of damaged equipment, down
time, and materials loss attributable to abrasive wear in the mining and agriculture industries alone is
staggering. Several types of two-body and three-body abrasive wear tests are described. As with other types of
wear, more than one kind of test can be needed to establish the suitability of a given material, coating, or
surface treatment for complex abrasive environments.
Erosive wear, as indicated in Table 1, can involve removal of material by impinging solids, liquids, liquid-
entrained or gas-entrained solids, bubbles (cavitation erosion), or sparks. Like abrasive wear, erosive wear is a
costly form of wear in industry. It attacks piping, pumping equipment, turbomachinery, and conveyor systems.
Loose particles from erosive wear can also travel to other parts of a machine, creating secondary damage and
loss of function. The variables associated with different types of erosive wear tests commonly include
impingement angle, impingement velocity, screening by rebounding particles, and the shapes and sizes of the
erodent particles.
Sliding contact, like galling or scuffing, can produce surface damage with only one contact event, or it can be a
progressive form of wear like fretting or other repetitive contact types of wear. The article “Testing for Sliding
Contact Damage” in this Section describes several forms of sliding contact damage and the methods commonly
used to evaluate the resistance of materials to these damages.
Just as machines and their parts exist in a spectrum of sizes, friction and wear phenomena can also occur in
various size scales. Obviously, the fine-scale interfacial contact processes involved in nanoscale coatings on
hard disks require a different testing approach than the macroscale wear that occurs on the digger teeth of
mining equipment and on the bows of icebreakers. Therefore, not only are there different types of wear, like
abrasive wear, erosive wear, and so on, but there are also different size-scales of wear phenomena.
References cited in this section
2. H. Czichos, Tribology: A Systems Approach, Elsevier, Amsterdam, Netherlands, 1978, p 322–325
3. P.J. Blau, Wear Testing, Metals Handbook Desk Edition, ASM International, 1998, p 1342–1347
4. P.J. Blau, Glossary, Friction, Lubrication, and Wear Technology, Vol 18, ASM Handbook, ASM
International, 1992, p 1–21
Introduction to Adhesion, Friction, and Wear Testing
Peter J. Blau, Oak Ridge National Laboratory
Adhesion, Friction, and Wear Testing Devices
Literally hundreds of devices for measuring adhesion, friction, and wear have been developed. Some of these
are commercially manufactured but most of them probably have been custom-designed for specific purposes.
This situation makes it difficult to compare the results from one study with those of another study unless the
appropriate correlation has been established. There is no simple answer to the problems arising from the