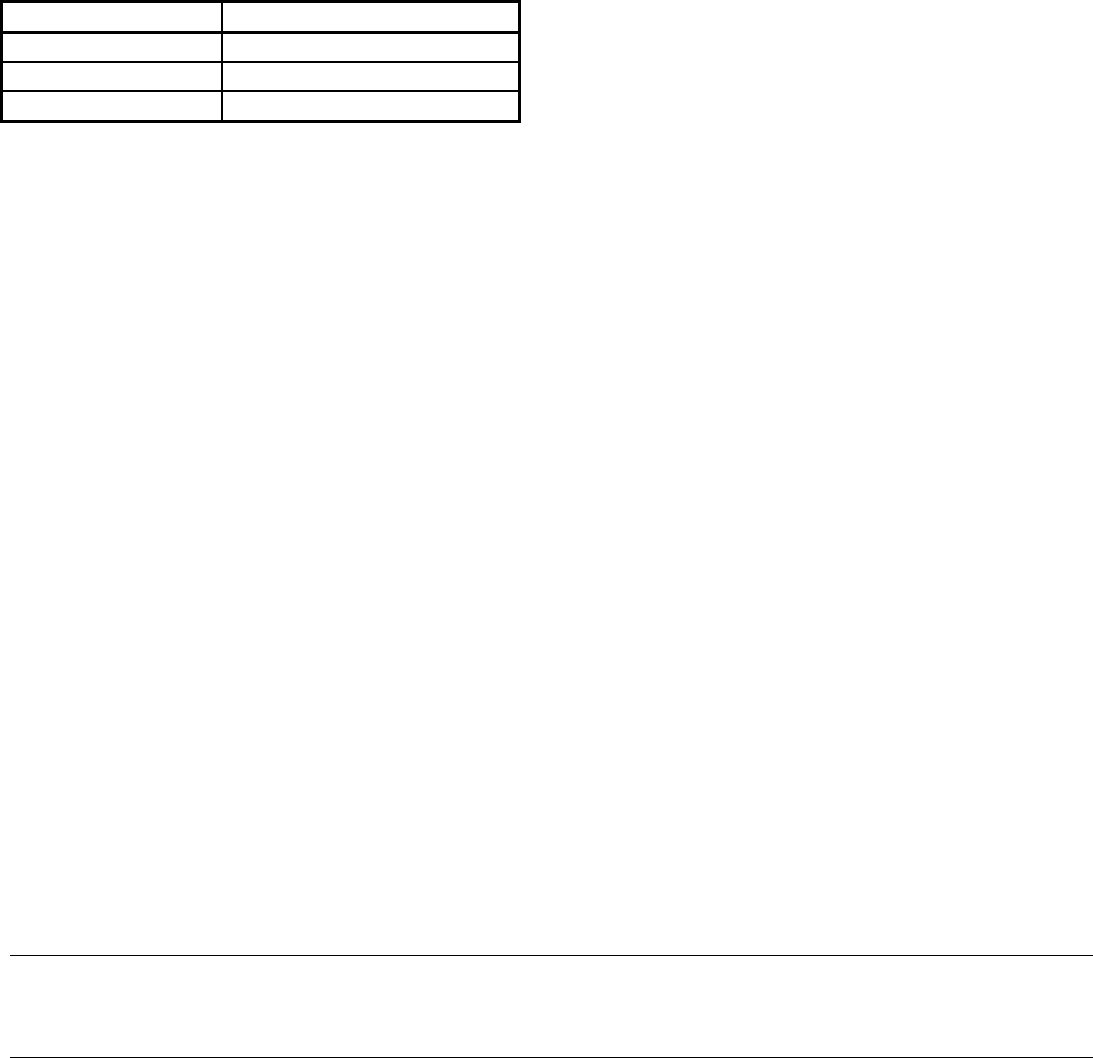
Verification by Test Block (Indirect Verification). Standardized Brinell test blocks are available so that the
accuracy of the Brinell hardness tester can be indirectly verified at the hardness level of the work being tested.
Commonly available hardnesses are:
Test block material
Hardness, HB
Steel
500, 400, 350, 300, 250, 200
Brass
90
Aluminum 140
Good practice is to verify the tester throughout the hardness range encountered. This ensures that all test
parameters are within tolerance.
Application for Specific Materials
As is true for other indentation methods of testing hardness, the most accurate results are obtained when testing
homogeneous materials, regardless of the hardness range.
Steels. Virtually all hardened-and-tempered or annealed steels within the range of hardness mentioned provide
accurate results with the Brinell test. However,a s a rule, case-hardened steels are totally unsuitable for Brinell
testing. In most instances, the surface hardness is above the practical range and is rarely thick enough to provide
the required support for a Brinell test. Thus, “cave in” results, and grossly inaccurate readings are obtained.
Cast Irons. The large area of the test serves to average out the hardness difference between the iron and graphite
particles present in most cast iron. This averaging effect allows the Brinell test to serve as an excellent quality-
control tool.
Nonferrous metals (especially the wrought types) are generally amenable to Brinell testing, usually with the 500
kgf load, but occasionally with the 1500 kgf load. Some high-strength alloys such as titanium- and nickel-base
alloys that are phase-transformation- or age-hardened can utilize the 3000 kgf load. In this situation, practical
limits must be observed and some testing may be required to establish the optimal technique for testing a
specific metal or alloy.
There are certain multiphase cast nonferrous alloys that are simply too soft for accurate Brinell testing.
Microhardness testing is then employed. The lower limit of 16 HB with a 500 kgf load must always be
observed.
Powder Metallurgy Parts. Testing of P/M parts with a Brinell tester (or any sort of macro-hardness tester)
involves the same problem as encountered with cast iron. Instead of a soft graphite phase (some P/M parts also
contain free graphite), P/M parts contain voids that may vary widely in size and number. Light-load Brinell
testing is sometimes used successfully for testing of P/M parts, but its only real value is as a quality-control tool
in measuring the apparent hardness of P/M parts (see the article “Selection and Industrial Applications of
Hardness Tests” for more information on P/M hardness testing.)
Macroindentation Hardness Testing
Edward L. Tobolski, Wilson Instruments Division, Instron Corporation; Andrew Fee, Consultant
Vickers Hardness Testing
The Vickers hardness was first introduced in England in 1925 by R. Smith and G. Sandland (Ref 5). It was
originally known as the 136° diamond pyramid hardness test because of the shape of the indenter. The
manufacture of the first tester was a company known as Vickers-Armstrong Limited, of Crayford, Kent,
England. As the test and the tester gained popularity, the name Vickers became the recognized designation for
the test.
The Vickers test method is similar to the Brinell principle in that a defined shaped indenter is pressed into a
material, the indenting force is removed, the resulting indentation diagonals are measured, and the hardness
number is calculated by dividing the force by the surface area of the indentation. Vickers testing is divided into
two distinct types of hardness tests: macroindentation and microindentation tests. These two types of tests are