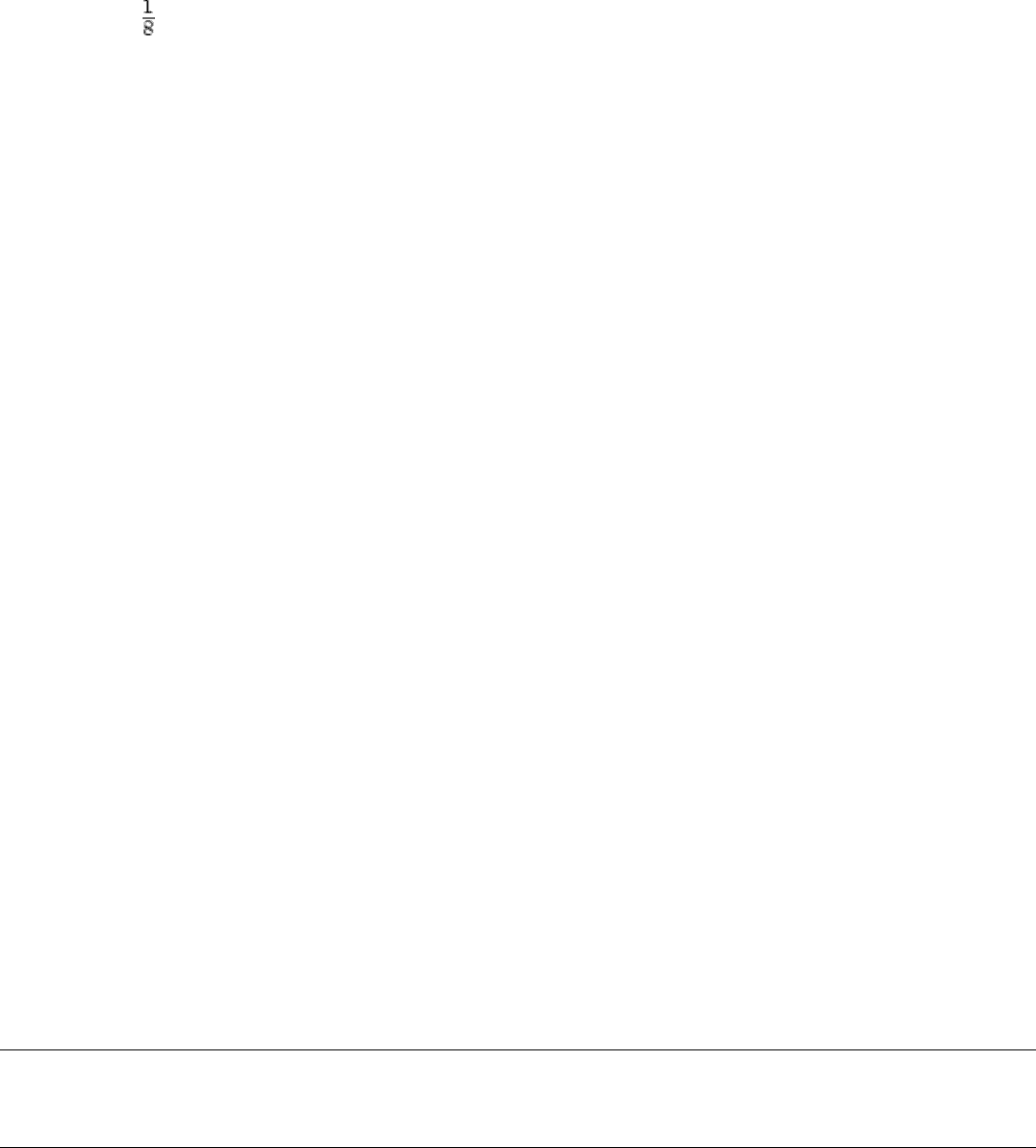
Cast irons, because of graphite inclusions, usually show indentation values that are below the matrix value. For
small castings or restricted areas in which a Brinell test is not feasible, tests may be made with either the
Rockwell B or C scale. If the hardness range permits, however, the Rockwell E or K scale is preferred, because
the 3.175 mm ( in.) diam ball provides a better average reading.
Powder metallurgy (P/M) parts usually are tested on the Rockwell F, H, or B scale. Where possible, the
Rockwell B scale should be used. In all instances, the result is apparent hardness because of the voids present in
the P/M parts. Therefore, indentation testing does not provide accurate results of matrix hardness, although it
serves well as a quality-control tool.
Cemented carbides are usually tested with the Rockwell A scale. If voids exist, the result is apparent hardness,
and matrix evaluations are possible only by microhardness testing.
Case-Hardened Parts. For accuracy in testing case-hardened workpieces, the effective case depth should be at
least 10 times the indentation depth. Generally, cases are quite hard and require the use of a diamond indenter;
thus, a choice of six scales exists, and the scale should be selected in accordance with the case depth.
If the case depth is not known, a skilled operator can, by using several different (sometimes only two) scales
and making comparisons on a conversion table, determine certain case characteristics. For example, if a part
shows a reading of 91 HR15N and 62 HRC, this indicates a case that is hard at the surface, as well as at an
appreciable depth, because the equivalent of 62 HRC is 91 HR15N. However, if the reading shows 91 HR15N
and only 55 HRC, this indicates that the indenter has broken through a relatively thin case.
Decarburization can be detected by the indentation hardness test, essentially by reversing the technique
described above for obtaining an indication of case depth. Two indentation tests—one with the Rockwell 15N
scale and another with the Rockwell C scale—should be performed. If the equivalent hardness is not obtained
in converting from the Rockwell 15N to the Rockwell C scale, a decarburized layer is indicated. This technique
is most effective for determining very thick layers of decarburization, 0.1 mm (0.004 in.) or less. When
decarburization is present, other methods such as microindentation hardness testing should be used to determine
the extent.
References cited in this section
1. F. Garofalo, P.R. Malenock, and G.V. Smith, Hardness of Various Steels at Elevated Temperatures,
Trans. ASM, Vol 45, 1953, p 377–396
2. M. Semchyshen and C.S. Torgerson, Apparatus for Determining the Hardness of Metals at
Temperatures up to 3000 °F, Trans. ASM, Vol 50, 1958, p 830–837
3. J.H. Westbrook, Temperature Dependence of the Hardness of Pure Metals, Trans. ASM, Vol 45, 1953, p
221–248
4. L. Small, “Hardness—Theory and Practice,” Service Diamond Tool Company, Ferndale, MI, 1960, p
363–390
Macroindentation Hardness Testing
Edward L. Tobolski, Wilson Instruments Division, Instron Corporation; Andrew Fee, Consultant
Brinell Hardness Testing
The Brinell test is a simple indentation test for determining the hardness of a wide variety of materials. The test
consists of applying a constant load (force), usually between 500 and 3000 kgf, for a specified time (10 to 30 s)
using a 5 or 10 mm (0.2 or 0.4 in.) diam tungsten carbide ball on the flat surface of a workpiece (Fig. 12a). The