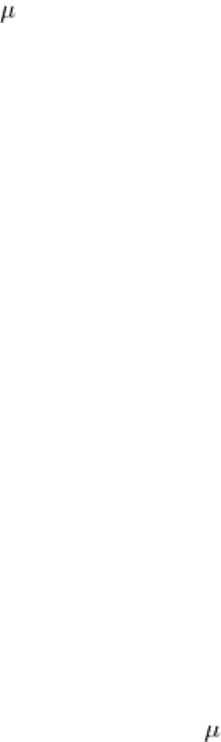
of photon counting when signal levels are low. Gas ionization detectors have low detection efficiencies but better long-
term stability than scintillator- and phosphor-photodetector arrays.
A typical phosphor-photodetector array for the radiographic inspection of welds consists of 1024 pixel elements with 25
m (1 mil) spacing, covering 25 mm (1 in.) in length perpendicular weld seam. The linear photodiode array is covered
with a fiber-optic faceplate and can be cooled in order to reduce noise. For the conversion of the x-rays to visible light,
fluorescent screens are coupled to the array by means of the fiber optics. A linear collimator parallel to the array is
arranged in front of the screen. The resolution perpendicular to the array is defined by the width of this slit and the speed
of the manipulator. A second, single-element detector is provided to detect instabilities of the x-ray beam. Using 100-kV
radiation, a spatial resolution of 0.1 mm (0.004 in.) can be achieved with a scanning speed of 1 to 10 mm/s (0.04 to 0.4
in./s).
The data from the detector system are digitized and then stored in a fast dual-ported memory. This permits quasi-
simultaneous access to the data during acquisition. Before the image is stored in the frame buffer and displayed on the
monitor, simple preprocessing can be done, such as intensity correction of the x-ray tube by the data of the second
detector and correction of the sensitivity for different array elements. If further image processing or automatic defect
evaluation is required, the system can be equipped with fast image-processing hardware. All standard devices for digital
storage can be utilized.
Image Processing. Because real-time systems generally do not provide the same level of image quality and contrast as
radiographic film, image processing is often used to enhance the images from image intensifiers, fluorescent screens, and
detector arrays. With image processing, the video images from real-time systems can compete with the image quality of
film radiography. Moreover, image processing also increases the dynamic range of real-time systems beyond that of film
(which typically has a dynamic range of about 1000:1).
Images can be processed in two ways: as an analog video signal and as a digitized signal. An example of analog
processing is to shade the image after the signal leaves the camera. Shading compensates for irregularities in brightness
across the video image due to thickness or density variations in the testpiece. This increases the dynamic range (or
latitude) of the system, which allows the inspection of parts having larger variations in thickness and density.
After analog image processing, the images can be digitized for further image enhancement. This digitization of the signal
may involve some detector requirements. In all real-time radiological applications, the images have to be obtained at low
dose rates (around 20 R/s). In digital x-ray imaging, however, the most often used dose is around 1 mR, in order to
reduce the signal fluctuations that would result from a weak x-ray flux. This means that only a short exposure time (of the
order of a few milliseconds) and a frequency of several images can be used if kinetic (motion) blurring is to be avoided.
The resulting requirements for the x-ray detector are therefore:
• The capability of operating properly in a pulsed mode, which calls for a fast temporal response
• An excellent linearity, to allow the use of the simplest and most efficient form of signal processing
• A wide operating dynamic range in terms of dose output (around 2000:1)
Once the image from the video camera has been digitized in the image processor, a variety of processing techniques can
be implemented. The image-processing techniques may range from the relatively simple operation of frame integration to
more complex operations such as automatic defect evaluation. The following discussions briefly describe three image-
processing operations. More detailed information on image processing is available in the article "Digital Image
Enhancement" in this Volume.
Frame integration (or summing) is a simple technique that can improve the signal-to-noise ratio and decrease (or
eliminate) the screen mottle associated with low levels of radiation intensity. This technique adds the digital images from
a number of frames and displays the result on a video monitor. Frame integration can be done in real time, that is, at
standard television frequency of 30 frames per second. The number of television frames that can be integrated depends on
the number of frame buffers available for this procedure. Typical summation times range from a few seconds for
applications using x-rays with high intensities up to 1 min or more for applications using radiation from low-activity
radionuclide sources. However, these times are small compared to the time required for exposing and developing x-ray
film.