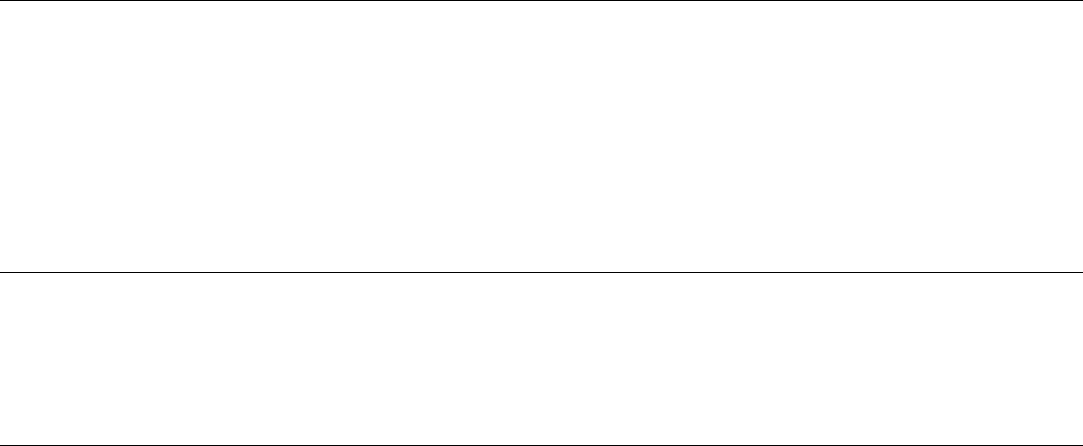
Chemical corrosion of soldered joints is frequently caused by inadequate removal of corrosive flux residues left from
the soldering operation. Other causes of chemical corrosion include residual plating or etching solutions and
contamination from packaging materials, handling procedures (including human perspiration), and environmental
conditions. Additional information on the corrosion characteristics of soldering alloys and soldered assemblies is
available in Corrosion, Volume 13 of ASM Handbook, formerly 9th Edition Metals Handbook.
Cleanliness in Soldered Joints
It is important that traces of flux or flux residues be removed during postsoldering cleaning procedures. In addition, many
solder operations are by nature contributors of small solder droplets. These small metallic particles can eventually be
dislodged in the assembly and can cause short circuits and other undesirable side effects. When an assembly is improperly
cleaned after soldering or fluxes are not removed, visual inspection is physically hampered. Cleanliness is therefore one
of the items that should be specified in any proper procedure for the inspection of soldered joints.
Developments in high-reliability low-current circuitry (especially printed circuits) have emphasized the importance of
cleanliness of electronic assemblies because of the danger of corrosion. Corrosion damage to conductors can increase
circuit resistance, and high resistance is undesirable. Corrosion can also cause physical failure of the conductors by
weakening and embrittlement. In addition, corrosion products themselves can cause current leakage. Current leakages are
particularly bad because they are not consistent; humidity changes in the atmosphere cause variations in and sometimes
intermittent occurrences of current leakage. Corrosion products also can cause contamination throughout the whole
system in the form of nonconductive deposits on mechanical contacts and relay surfaces. Corrosion is definitely a
problem, but corrosion is not always caused by fluxes. Additional information on the sources of corrosion in electronic
components is available in the articles "Corrosion in the Electronics Industry" and "Case Histories and Failures of
Electronics and Communications Equipment" in Corrosion, Volume 13 of ASM Handbook, formerly 9th Edition Metals
Handbook.
Cleanliness is easily checked after the proper cleaning procedures are followed. The danger to the assembly stems from
the presence of ionizable materials, mostly chlorides. The easiest and most thorough check is done with a conductivity
cell and distilled and demineralized water, either leaching the ionizable materials off the surfaces in premeasured amounts
of water or submerging the whole assembly into a container of the water and measuring the resistivity of the water. This
indicates the presence of ionizable materials. However, because chlorides are the major contributors in the corrosion
mechanism and are the most abundant form of ionic contamination on the assembly, standardized, simple silver nitrate
tests can be used to establish the presence of chlorides.
Cleanliness after soldering is important because soldering is usually the last step in a long process of assembly. However,
precautions must be taken to prevent recontamination of the surfaces; otherwise, the purpose of cleanliness and of the
check for corrosion products in the final inspection is defeated.
References cited in this section
8.
R. Vanzetti, "Intelligent Laser Soldering Inspection and Process Control, Electronics Reliability and
Measurement Technology," NASA CP-2472, National Aeronautics and Spac
e Administration, June 1986, p
85-94
9. A.C. Traub, Parts Inspection by Laser Beam Heat Injection, NDT Int., Vol 21 (No. 2), April 1988, p 63-69
10.
R.S. Gilmore, Acoustic Microscopy, in Encyclopedia of Materials Science and Engineering,
Press, 1986, p 38-43
Note cited in this section
** Example 3was prepared by Dr. Robert S. Gilmore, General Electric Research and Development Center.
Nondestructive Inspection of Weldments, Brazed Assemblies, and Soldered Joints
References