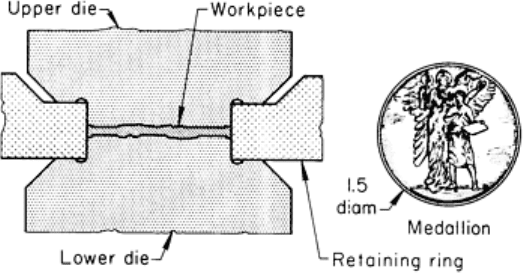
Two workpieces were formed and coined simultaneously from one blank, in two blows of the drop hammer. The two-
cavity die permitted easy loading and unloading of parts and also provided symmetry to prevent shifting of the punch. A
volatile, fatty oil-base lubricant was applied to the blank by rollers.
The formed and coined halves were separated by slitting with a rotating cutter made of T1 tool steel, and the flange was
removed in a pinch-trim operation. After belt grinding to deburr and provide a smooth, flat surface, the half handles were
fluxed along the edges and soldered together. The soldered handles were then pickled, washed, and finished by a light
emery on the soldered seams, and then were silver plated. The handle and blade were assembled and finish buffed.
Coins and medallions are produced by closed-die coining, in which a prepared blank is compressed between the
coining dies while it is retained and positioned between the dies by a ring or collar. The volume of metal in the workpiece
is equal to the volume of the die space when the die is closed. The volume of metal cannot exceed the closed-die space
without developing excessive loads that may break the die and press. The simplest means of ensuring volume control in a
coin blank is by carefully controlling the weight, which is easily measured and converted to volume.
In general, coins are needed in large quantities (about 300,000 before die dressing). To facilitate production and minimize
die wear, the detail incorporated into the coin design is in low relief. The coin should have good wear resistance, which is
achieved by the compressive working of the metal during coining. Wear of the coin face is prevented by raising the edge
of the coin, which is usually serrated to have a so-called milled edge. This edge detail is machined into the retaining ring
and is transferred to the expanding workpiece during coining. A typical procedure for coin manufacture is as follows:
• Coin disks are blanked from sheet of prescribed thickness and surface finish
• The disks are barrel tumbled to deburr, to develop a suitable surface finish, and to control weight
• The disks are edge rolled
• The disks are fed, one at a time, to the coining station for coining
•
The coins are ejected from the retaining ring. This may be done by movement of the upper or lower die
rather than by use of a conventional ejector
The steps employed to manufacture coins may also be used for medallions, with some added steps. Usually the processing
of medallions does not require edging operations, but if the design details are in high relief, the full development of
details may require restriking. Coined blanks are usually annealed before restriking. The blank must be reinserted into the
coining dies in its initial position and then restruck. The use of this method for the manufacture of a medallion is
described in the following example.
Example 2: Coining of Sterling Silver Alloy Medallions.
Medallions made from sterling silver alloy (92.5Ag-7.5Cu) and weighing 28 g (1 oz) (±1%) were made by coining, using
the die setup illustrated in Fig. 2. Disks were blanked from strip and barrel finished. Following the first coining operation,
the workpiece was annealed at 690 °C (1275 °F), repositioned in the die, and restruck. The single-station tooling
consisted of the upper and lower incised O1 tool steel dies (60 HRC) and a retaining ring. After coining without
lubrication, the medallion was manually removed from the retaining ring, because of the low production requirements (48
pieces per hour). Coining was done in a 3.6 MN (400 tonf) knuckle-type mechanical press.