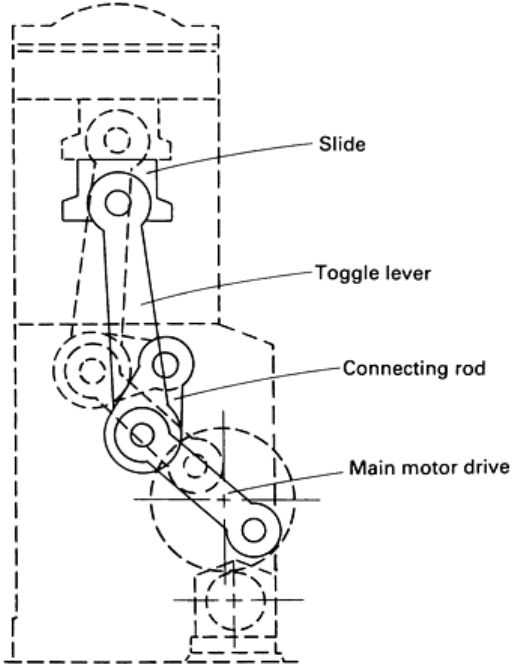
A closed-die flashless warm-forging process was developed with the capability to generate vertical sides (no draft) and
square (filled) corners (Ref 5). In the context of applying this process for ferrous forging, the warm temperature range was
considered to extend to approximately 1000 °C (1830 °F). The process is also applicable to the forging of brass,
aluminum, copper, and titanium.
Dimensional tolerances of this process are ±0.25 mm (±0.010 in.). All forged surfaces have a finish of 3.20 μm (125 μin.)
rms or better.
Because there is no flash to absorb variations in the billet material volume, control of that volume is critical. Any material
in excess of the volume of the die cavity must be accommodated by elastic deflection of the tooling and the press. During
the development of the flashless process, it was found that a mechanical press with a tension knuckle drive (Fig. 8)
system would be an advantage because it would have a higher compliance than other types of mechanical presses.
Specifically, it was determined that a 5300 kN (600 tonf) tension knuckle press would stretch 2 mm (0.080 in.) when fully
loaded. A comparable top (compression) driven mechanical press would deflect only 0.2 mm (0.008 in.), an order of
magnitude less.
Fig. 8 Schematic of tension knuckle drive forging press. Source: Komatsu, Ltd.
With the tension knuckle drive press, the allowable variation in preform volume is -0.0/+1.4%. Preforms are headed
(upset) prior to forging to control weight within this tolerance. Preform volume is also affected by temperature because of
the effect of thermal expansion. Temperature control within ±28 °C (±50 °F) was found to be acceptable.
The relationship of the volume of the preform to the volume of the die cavity is also affected by any changes in the
tooling itself. Therefore, the tooling temperature is held within 17 °C (30 °F) of ambient by using a flood of coolant. The
coolant also contains graphite and therefore functions as a lubricant. Buildup of lubricant within the tooling would
effectively decrease the volume of the die, and the lubricant is controlled to prevent this. Tool wear is also closely
monitored because this increases the die volume. Such an increase would result in an underfill condition because there is
no excess of raw material.