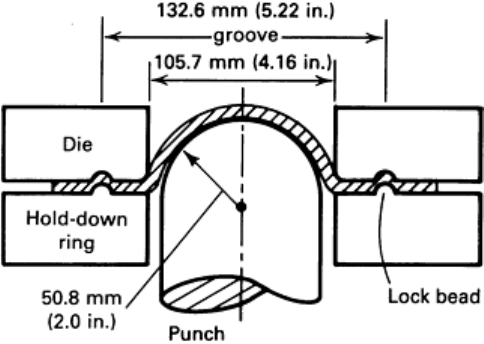
The specimens fracture circumferentially at a distance (for
lightly lubricated low-carbon steel) of 35 to 40 mm (1.38
to 1.57 in.) from the pole, at which point the radial strain
peaks sharply. The circumferential strain varies gradually
from a maximum of 10 to 20% at the pole to zero at the
lock bead.
The hemispherical dome test yields more reproducible
results than the Olsen and Erichsen cup tests. For low-
carbon steels, the dome height, which is measured at the
point of maximum load, increases linearly with the n
value. For a wide range of material (including brasses,
aluminum alloys, and zinc), optimal correlation is found
between the dome height and the total elongation, which
incorporates the effects of strain rate hardening and
limiting strains.
Overall, the use of lubrication in hemispherical dome tests
is beneficial. A thin layer of a standard lubricant, applied
in a consistent manner, reduces scatter in test results,
simulates production conditions more closely, reduces damage to the tooling, and simplifies specimen preparation. The
improved sensitivity obtained in the dry condition is negated by the increased scatter in the results.
The use of lubrication makes the strain ratio at fracture more biaxial. This is undesirable for production simulation,
because most production failures occur in the region of plane strain, that is, in a less biaxial manner. To control the strain
ratio at fracture, specimens of different widths were used (Ref 54). This technique has been developed further into the
limiting dome height test (Ref 55, 56).
Limiting Dome Height (LDH) Test. Specimens of various widths are held in a circular lock bead and stretched over
a 100 mm (3.94 in.) dome using tooling of the type shown in Fig. 22. In principle, this test can be used to duplicate a large
range of production failure strain states and to select the most suitable material for each particular operation. In practice,
most production failures occur close to plane strain, which is generally the strain state at the minimum on a plot of dome
height versus specimen width. Consequently, attention has concentrated on this minimum value.
When testing a new material, initial tests should be performed to determine the specimen width that yields the minimum
dome height, or LDH value, and the corresponding minor strain. Once this has been established, tests can be conducted at
this width only. For low-carbon steels, the minimum dome height occurs at a width of approximately 124 mm (4.9 in.).
This can also be used as an approximation for other materials. Increments in test specimen width of ±3 mm (±0.12 in.) are
sufficiently close.
It has been found that, for specimens lubricated lightly with a wash oil, the dome height increases with decreasing hold-
down force below about 250 kN (28 tonf). This is attributed to the drawing-in of the flange. Therefore, a hold-down force
of at least 250 kN (28 tonf) should be used. The limiting dome height is taken as the height at which the maximum load
occurs.
Preliminary tests have shown a correlation between the limiting dome height test and production stamping performance
(Ref 57). Some problems have been encountered with test reproducibility over a period of time and among different test
facilities. Numerous attempts have been made to determine a correlation between the limiting dome height test and
mechanical and forming property measurements. The dome height depends on the ability of the material to distribute
strain and on the limiting strain level and would therefore be expected to correlate with the total elongation. Correlation
for a range of different materials has been reported (Ref 58).
The specimens used in the limiting dome height test can be sheared or blanked from the sheet sample, and the test can be
performed rapidly on equipment that automatically measures the dome height at the maximum punch load. The test has
considerable potential for production control and research applications.
Hole Expansion Test. A flat sheet specimen with a circular hole in the center is clamped between annular die plates
and deformed by a punch, which expands and ultimately cracks the edge of the hole. Flat-bottomed hemispherical and
Fig. 22
Tooling for the 101.6 mm (4.0 in.)
hemispherical dome test. Source: Ref 52.