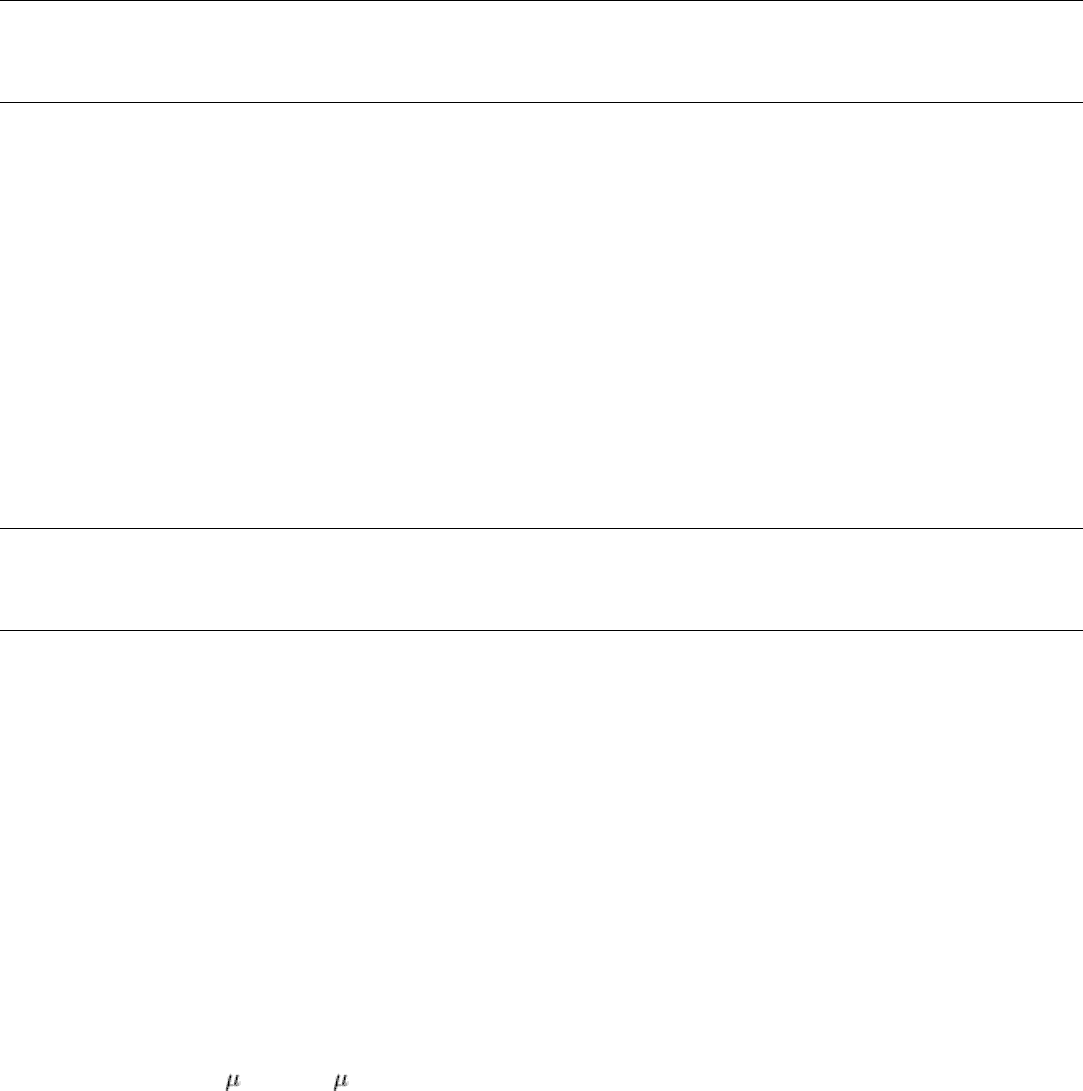
Superplastic Sheet Forming
C.H. Hamilton, Washington State University; A.K. Ghosh, Rockwell International
Manufacturing Outlook
The SPF process is unique in terms of the complexity of parts that can be produced and the methods that can be used to
shape such a material. A number of processing methods are currently being used, most of which involve significant
stretching of sheet material. The high ductility that can be achieved with these types of materials also has a consequence
that must be understood and dealt with, namely, thinning gradients. The thinning gradients are a natural consequence of
the stress gradients that develop in the various die configurations, and the superplastic property of the strain rate
sensitivity of the flow stress then determines the subsequent thinning gradient that will result in the part. Control of the
forming process, die configuration, and material characteristics are all factors that can affect the thinning.
The SPF processes are being increasingly used for a wide range of structural and nonstructural applications. The
availability of superplastic alloys is considered to be a major impediment to the broader use of these processes, but as the
use of the technology increases, more and perhaps better superplastic alloys can be expected to become available.
Superplastic Sheet Forming
C.H. Hamilton, Washington State University; A.K. Ghosh, Rockwell International
Appendix: Superplasticity in Iron-Base Alloys
Oleg D. Sherby, Stanford University; Jeffrey Wadsworth, Lockheed Missiles and Space Company; Robert D. Caligiuri, Failure Analysis
Associates
Superplasticity is the ability of certain polycrystalline metallic materials to extend plastically to large strains when
deformed in tension. Strains to failure in superplastic materials range from several hundred to several thousand percent. In
general, superplastic materials also exhibit low resistance to plastic flow in specific temperature and strain rate regions.
These characteristics of high plasticity and low strength are ideal for the manufacturer who needs to fabricate a material
into a complex but sound body with a minimum expenditure of energy.
The phenomenon of superplasticity was first observed over 70 years ago (Ref 48), but active research in this field did not
begin until 1962 (Ref 49). Since that time, superplastic effects have been reported in over 100 alloy systems (Ref 49). The
micro-mechanisms that permit extraordinary elongations in these materials are still under investigation (Ref 50), but it is
generally accepted that a major microstructural requirement for superplasticity is the development of a stable, very fine
grain size (typically <10 m, or 400 in.) (Ref 51). This requirement also usually (but not always) leads to the necessity
for a uniform distribution of a fine, second phase to inhibit matrix grain growth. Furthermore, the grain boundaries should
be high angled (that is, disordered), equiaxed, mobile, and must resist separation under tensile stresses (Ref 52). To
prevent cavitation around the second-phase particles, the strengths of the two phases should be similar at the temperature
of deformation (Ref 52). These micro-structural characteristics can lead to a flow stress that is highly sensitive to changes
in strain rate, which in turn resists the formation of instabilities during tensile deformation.
Even though superplasticity has been observed in many metallic alloy systems, only a relatively small number of them are
iron-base. This is because of the difficulty in generating microstructures in these systems with the above characteristics.
As a result, there have been relatively few industrial applications involving the superplastic bulk forming of ferrous
alloys. Those iron-base systems in which the microstructural requirements have been met include:
• Hypoeutectoid and eutectoid plain carbon steels (ferrite-carbide two-phase system)
• Hypereutectoid plain carbon steel (ferrite-carbide and austenite-carbide two-
cast iron (ferrite-carbide two-phase system)
• Low-to-medium alloy steels (ferrite-austenite two-phase system)