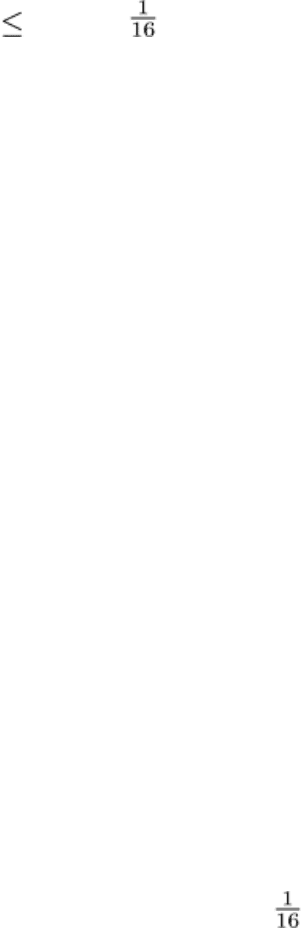
Most simple shapes can be deep drawn in nickel-base alloys using dies and tools designed for use on steel or copper
alloys. However, when intricate shapes with accurate finished dimensions are required, minor die alterations are
necessary. These alterations usually involve increasing clearances and enlarging the radius of the draw ring or of the
punch nose.
Double-Action Drawing. In drawing and redrawing of thin stock ( 1.6 mm, or in.) into cylindrical shells with no
ironing, the diameter reduction should be 35 to 40% on the first operation and 15 to 25% on redraws. If the walls are held
to size, the first and second operations may be the same as suggested above, but the amount of reduction should be
diminished by about 5% on each successive redraw.
Although reductions of up to 50% can be made in one operation, this is not advisable because of the possibility of
excessive shell breakage. Also, large reductions may open the surface of the metal and cause difficulty in finishing.
The number of redraws that can be made before annealing is necessary depends on the alloy being drawn. The alloys with
the lower rates of work hardening (Fig. 1) can often be redrawn more than once without intermediate annealing. Trial runs
may be needed to determine when annealing is necessary.
Single-Action Drawing. As with all metals, the depth to which nickel-base alloys can be drawn in single-action
presses without some means of blank restraint is controlled by the blank-thickness-to-diameter ratio. For single-action
drawing without holddown pressure, the blank thickness should be at least 2% of the blank or workpiece diameter for
reductions of up to 35%. With properly designed dies and sufficiently thick material, the reduction on the first (cupping)
operation with a single-action set-up may be made equal to those recommended for double-action dies--that is, 35 to 40%.
Redraws should not exceed a 20% reduction.
If the shell wall is to be ironed, the increased pressure on the bottom of the shell usually necessitates a decrease in the
amount of reduction to prevent shell breakage. With reductions of 5% or less, the shell wall may be thinned by as much as
30% in one draw. With medium reductions of about 12%, the thickness of the shell wall can be decreased by about 15%.
If the wall is to be reduced by a large amount, the shell should first be drawn to the approximate size with little or no wall
thinning and the ironing done last. If a good surface finish is desired, the final operation should have a burnishing effect
with only a slight change in wall thickness.
Clearances. Because nickel-base alloys have higher strengths than do low-carbon steel of drawing quality, nickel alloys
have greater resistance to the wall thinning caused by the pressure of the punch on the bottom of the shell. Consequently,
greater die clearance is required than is the case for steel if the natural flow of the metal is not to be resisted. However, the
clearances required for nickel-base alloys are only slightly greater than those required for steel, and if dies used for steel
have greater-than-minimum clearances, they are usually satisfactory for drawing nickel-base alloys, depending primarily
on the mechanical properties of the alloy.
For ordinary deep drawing of cylindrical shells, a punch-die clearance per side of 120 to 125% of the blank thickness is
sufficient and will prevent the formation of wrinkles. In the drawing of sheet thicker than 1.6 mm ( in.), it is general
practice to have the inside diameter of the draw ring larger than the diameter of the punch by three times the thickness of
the blank (150% of stock thickness per side).
Draw-Ring and Punch Radii. Because nickel-base alloys work harden rapidly, relatively large draw-ring and punch
radii should be used, especially for the early operations in a series of draws. Nickel-base alloys require more power to
draw than does steel; consequently, the punch imposes a greater stress on the bottom corner of the shell. Small punch
radii cause thinning of the shell at the line of contact, and if such a shell is further reduced, the thinned areas will appear
farther up the shell wall, and may result in visible necking or rupture. Also, buffing a shell having thinned areas will cause
the shell wall to have a wavy appearance. For redraws, it is preferable to draw over a beveled edge and to avoid round-
edged punches except for the final draw.
The draw-ring radius for a circular die is principally governed by the thickness of the material to be drawn and the amount
of reduction to be made. A general rule for light-gage material is to have the draw-ring radius from 5 to 12 times the
thickness of the metal. Insufficient draw-ring radius may result in galling and excessive thinning of the wall.
Drawing Rectangular Shells. As with other materials, the depth to which rectangular shapes can be drawn in nickel-
base alloys in one operation is principally governed by the corner radius. To permit drawing to substantial depths, the