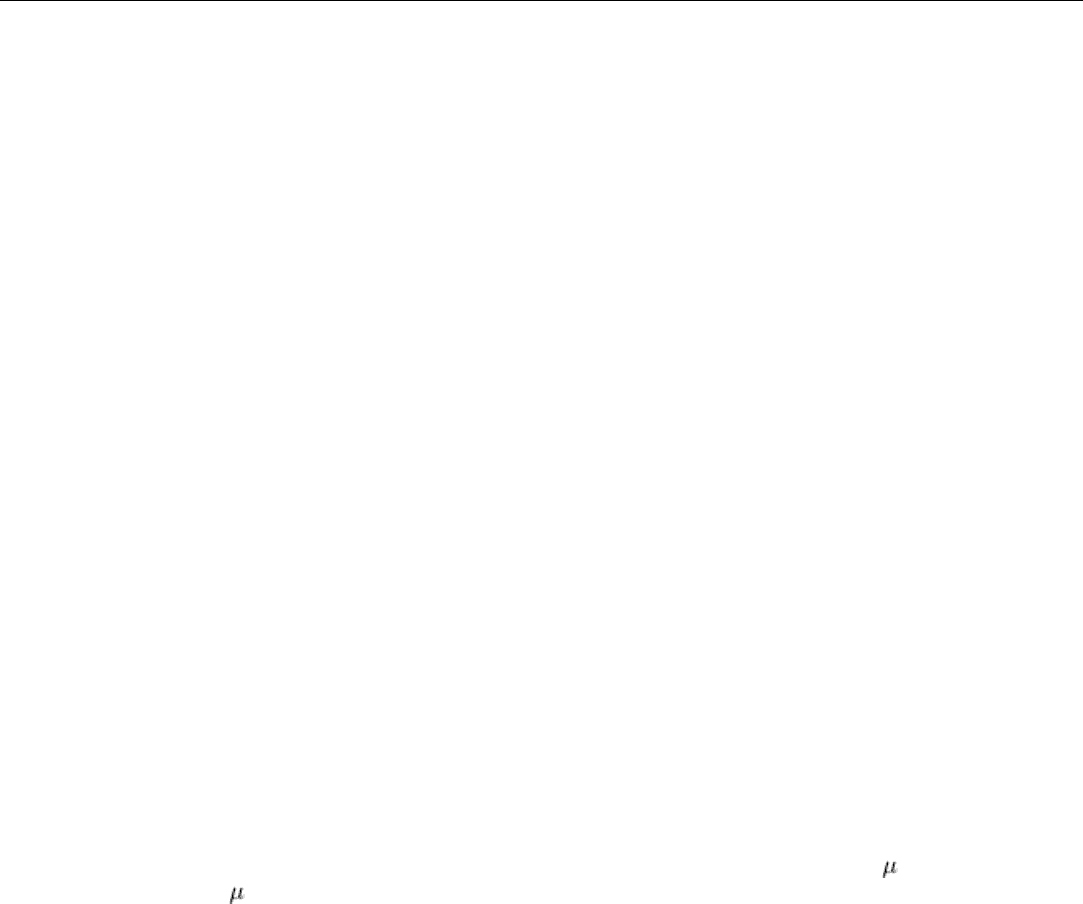
by this method are less formable than steels that are coated at lower temperature. Depending on carbon content, steels
coated by the high-temperature hot-dip process may or may not require postannealing to enhance formability. Low-
carbon steels often require postannealing to restore full formability; extralow-carbon steels (0.01% C) normally do not
require postannealing.
Electrogalvanizing is conducted at temperatures at or near ambient; therefore, the properties of electrogalvanized steel
sheet are nearly identical to those of uncoated cold-rolled steel.
Other types of coatings discussed in this article include aluminum, tin, terne (lead-tin alloy), nickel and chromium,
and organic coatings. Because aluminum is applied by hot dipping, aluminum-coated (aluminized) steel is subject to the
same types of problems as hot-dip galvanized steel. Tin coatings can be applied by hot-dipping or electroplating; the latter
is much more common. Terne is a hot-dip product. Nickel plating and chromium plating are applied by electroplating.
The methods used to apply paints and other organic coatings vary, although most require curing at moderate temperature
to achieve final properties. These coatings will be discussed in more detail in the following sections.
Press Forming of Coated Steel
Galvanized Steels
The formability of galvanized steels is reduced to some extent by the brittle iron-zinc alloy layer that is produced between
the metallic zinc and the steel base during hot-dip galvanizing. The thickness of the alloy layer depends on the
temperature-time cycle in galvanizing, but it is also affected by the percentage of other metals, especially lead and
aluminum, in the molten-zinc bath. The decrease in formability is usually in direct proportion to the thickness of the iron-
zinc alloy layer. Modern hot-dip galvanizing processes use special thermal cycles and low-lead low-aluminum coating
materials to minimize formation of the iron-zinc alloy layer.
In deep drawing, the beneficial effects of the free-zinc layer on the surface of the work metal outweigh the adverse effect
of the alloy layer, often permitting greater reductions and greater draw depths than with similar uncoated steel. The layer
of soft metallic zinc prevents galling during forming by eliminating direct contact between the steel substrate and the
punch.
Formability is also influenced by other factors; chief among these are the initial properties of the steel base; the amount of
mechanical work before or after galvanizing; and the response of the steel to the heating cycle for galvanizing, to
supplementary heat treatments, and to aging. These factors often have a greater effect on the formability of galvanized
steel than the galvanized coating does.
Mill Products. Galvanized steel sheet for use in forming is generally purchased in one of four AISI grades:
• Commercial quality (CQ)
• Drawing quality (DQ)
• Drawing quality, special killed (DQSK)
• Drawing-quality special-killed extralow carbon
Drawing-quality special-killed extralow-carbon steel is available in both stabilized (interstitial-free) and nonstabilized
grades. The grades listed above are available in either the dead-soft or the temper-rolled condition.
The thickness of the zinc coating per side, including the iron-zinc alloy layer, ranges from about 55 m (2.15 mils) for the
heaviest coating to 16.5 m (0.65 mils) in eight coating classes. It is more common, however, to specify the desired
coating by weight per unit of surface area. This is particularly true in the automotive industry; automakers are requesting
closer weight control tolerances for more consistent welding and forming characteristics. Coating weight is commonly
specified in the auto industry in terms of grams per square meter (g/m
2
) per side.
One-side galvanized steels have also been developed for the automotive industry. These materials are used with the
galvanized side facing inward; this gives the protection of galvanizing while maintaining the paintability and weldability
of uncoated low-carbon steel on the outside of the panel.