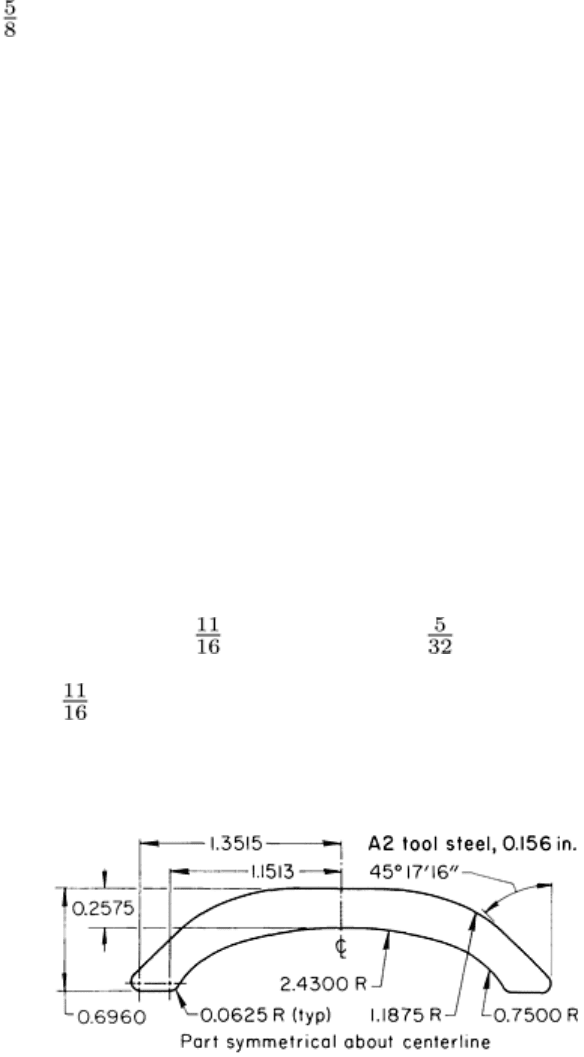
The punch and the die were both originally made of D2 tool steel at 62 to 63 HRC. To keep burr height on the parts at or
below the maximum of 0.08 mm (0.003 in.), it was necessary to grind the die after each 25,000 pieces. The steel die had a
usable depth of 16 mm ( in.) and 0.20 mm (0.008 in.) was removed with each grinding. Therefore, with 78 grindings,
the total die life was 1,950,000 pieces.
To improve die life, the tool material for both the punch and the die was changed to carbide. The carbide tools cost three
times as much as the steel punch and die, but production between grinds increased to 350,000 pieces and only 0.10 mm
(0.004 in.) of stock was removed per grind. Therefore, with the same amount of usable die, the total die life would be
54,600,000 pieces.
The die was a compound-type unit. It was operated in a 445 kN (50 tonf) open-back inclinable mechanical press having a
75 mm (3 in.) stroke and mechanical feed.
Tooling for Greatest Efficiency. Along with the increase in punch-to-die clearance, other tool changes are required
for efficiency in the blanking and piercing of high-carbon steel. For example, with high-carbon steel more so than with
low-carbon steel, the scrap skeleton from blanking and piercing operations is likely, in springing back, to adhere to the
punch, sometimes causing spalling of the punch edges. To strip this scrap from the punch, it is common practice to
include in the punch mechanism a second, chisel-pointed punch placed as close as possible to the blanking edge. This
second punch serves to spread the scrap skeleton, minimizing its adherence to the blanking punch (see Example 2).
The following example deals with changes in tooling that reduced cost. In the example, blanking replaced machining.
Example 2: Cost Reduction When Blanking Replaced Milling.
The blanked workpiece shown in Fig. 2 replaced a machined part of slightly different dimensions. For the machined part,
starting blanks 75 mm (3 in.) long by 17 mm ( in.) wide by 4.0 mm ( in.) thick were sawed from ground flat stock
of A2 tool steel spheroidize-annealed to 14 to 18 HRC. The long edges of the blanks were ground to reduce the width of
the blank from 17 to 15.9 mm ( to 0.625 in.). Grinding was followed by four separate milling operations. This change
in production method from milling to blanking reduced the machining time for 100 pieces from 28 to 0.23 h and
decreased cost per piece by a factor of 122.
Fig. 2 Part produced by blanking for less than 1% of the per-
piece cost of producing it by milling. The punch
was modified to solve a stripping problem. Dimensions given in inches.
The blanking was done in a 280 kN (32 tonf) open-back inclinable mechanical press with a punch and die made from A2
tool steel at 60 to 62 HRC. To obtain acceptable edges on the workpiece, a punch-to-die clearance of 8 to 10% of stock
thickness per side was used. Because of the force required for stripping, it was necessary to add a chisel-edge punch to
spread the scrap skeleton and to prevent damage to the blanking punch. In addition, a minimum corner radius of 1.6 mm
(0.062 in.) was necessary for efficient stripping, and the overall width of the part was increased to 17.7 mm (0.696 in.).
Dimensional accuracy in the blanking and piercing of high-carbon steel depends largely on the accuracy of the
tooling. Initially, the practical accuracy is the same as that for the blanking and piercing of other metals. However,
because the rate of tool wear is usually higher in the blanking and piercing of high-carbon steel (especially if