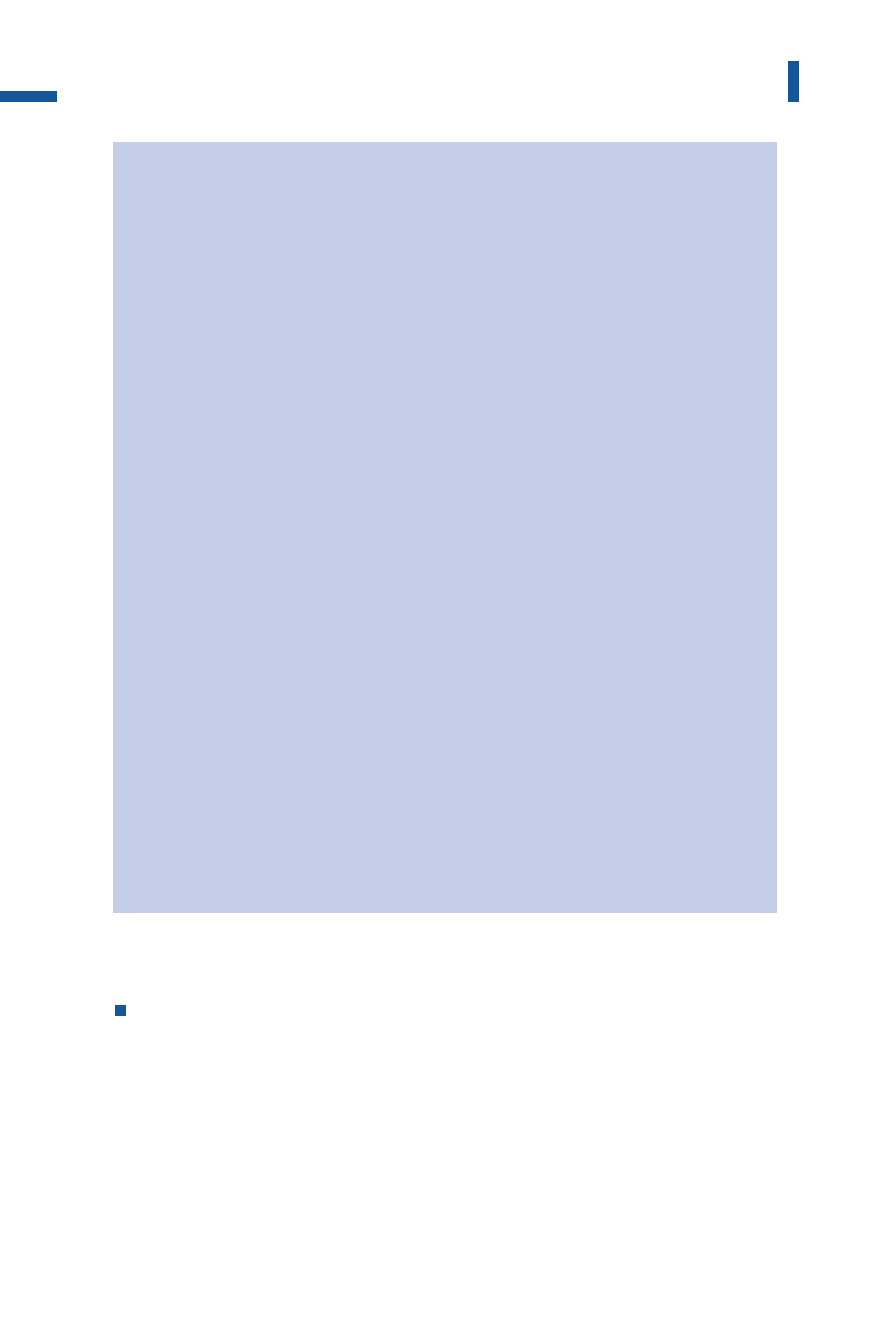
398
Sheet metal forming and blanking
Example:
A production unit has to be configured in which 44 pressed parts – primarily A
parts – have to be produced every year for 100,000 vehicles. The unit comprises
a blanking line, a crossbar transfer press and a tri-axis transfer press. A possible
configuration of this stamping plant with optimized material flow and periph-
eral devices is illustrated in Fig. 4.9.6.The material is supplied in the form of coil
stock and stored in the coil storage, from where it is fed to the blanking line.
This supplies through the blank storage both large-panel transfer presses with a
total of 4 million blanks a year. Following production on the transfer presses,
the parts are transported in part-specific racks to the intermediate storage for
finished parts.
Table 4.9.3 lists the part spectrum for both forming presses. The crossbar trans-
fer press is run using eight individual and eight double die sets, whereby the
double dies in this example always produce two different parts. Their die
change time amounts to 10 min. The tri-axis transfer press manufactures 20 dif-
ferent parts using 20 die sets. The die change time is also 10 min. Overall, the 44
parts are produced using 36 sets of dies – 20 on the tri-axis transfer press, and 24
on the crossbar transfer press.
If 222 working days are available per year, parts for 450 vehicles must be pro-
duced every day. In three-shift operation with working periods of 1,260 min per
day, the total of approx. 4.8 million parts indicated in Table 4.9.2 (achieved
with 3.9 million strokes) can be produced every year on the transfer presses.
This is based on a planned capacity utilization of 80%. Three days are selected
as a production cycle. If we take the simplified assumption that every part is
only run once per cycle, three times 450 parts must be produced per cycle. The
intermediate storage for finished parts has a theoretical maximum inventory of
1,800 pressed parts of each part type: 1,350 parts from running production plus
450 parts as a minimum safety inventory. On average, however, as body-in-
white production runs on a parallel basis, only around half of the parts are
located in the intermediate storage. At any point in time, the inventory com-
prises 900 344, i.e. approx. 40,000 parts. As a result, the part storage and the
capital investment this involves are considerably lower than when producing
on conventional press lines.
4.9.3Quality assurance through quality control
The aim of achieving zero-defect production calls for continuous qual-
ity control. This involves the detection of any changes in the produc-
tion process which could precede a defect, and the segregation of indi-
vidual defective parts. Conventional methods of quality assurance in
stamping plants include visual inspections – in the case of deep drawn
Metal Forming Handbook / Schuler (c) Springer-Verlag Berlin Heidelberg 1998