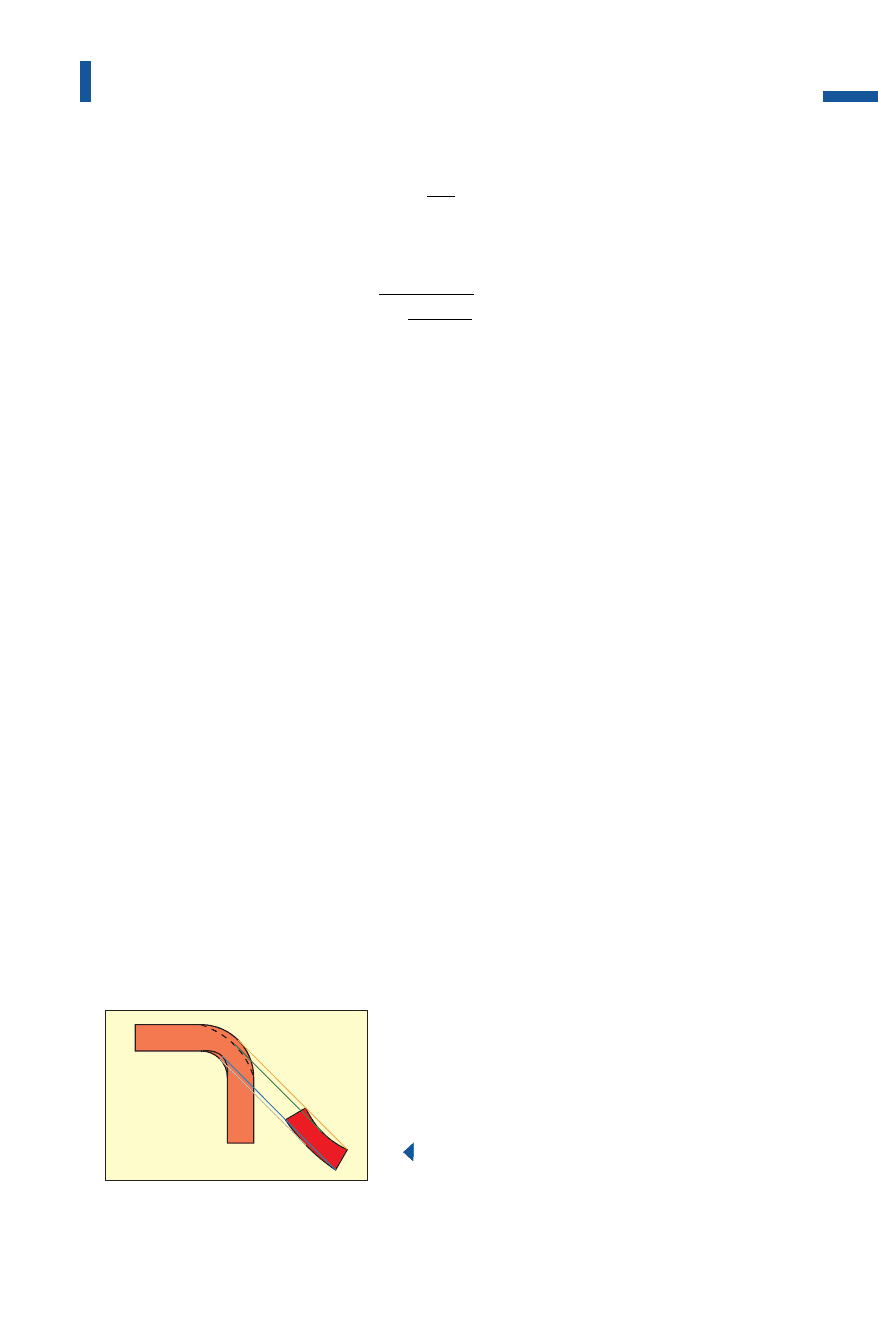
Accordingly, the necessary angle on the die is
The required inside radius at the die can thus be calculated as
with tensile strength R
m
[N/mm
2
] and elasticity module E [N/mm
2
].
Bending causes residual stresses in the workpiece. The smaller the
bending radius relative to the sheet metal thickness, the greater these
stresses are. When working with materials which are sensitive to stress-
corrosion, workpiece failure is therefore possible within a relatively short
period of time after forming. Coining following the bending process
helps to reduce residual stresses. When a subsequent heat treatment is
used to reduce residual stresses in the workpiece, it is important to
remember that heat treatment alters the workpiece radii and the angles.
Unwanted deformation during bending operations
If a sheet metal strip has a rectangular cross section, the sides of the rec-
tangle are determined by the coil width and the material thickness. In
the case of thick coil stock and sharp bends, i.e. small inside curvature
radius, this rectangle assumes a trapezoidal shape (Fig.4.8.2).
If several operations are executed on a single workpiece, i.e. several
folding processes are carried out simultaneously, steps must be taken to
ensure that sufficient material flow is available to replace the material
displaced during the forming process. Otherwise, under certain circum-
stances, it is possible that significant weakening or fracturing takes place
at the workpiece corners. In addition, the force required to achieve the
final shape increases.
369
Bending
r
r
rR
sE
mm
i
i
im
1
2
2
1
=
+
⋅
⋅
[]
Fig. 4.8.2
Deformation of the cross section during bending
α
α
1
2
=°
[]
k
R
Metal Forming Handbook / Schuler (c) Springer-Verlag Berlin Heidelberg 1998