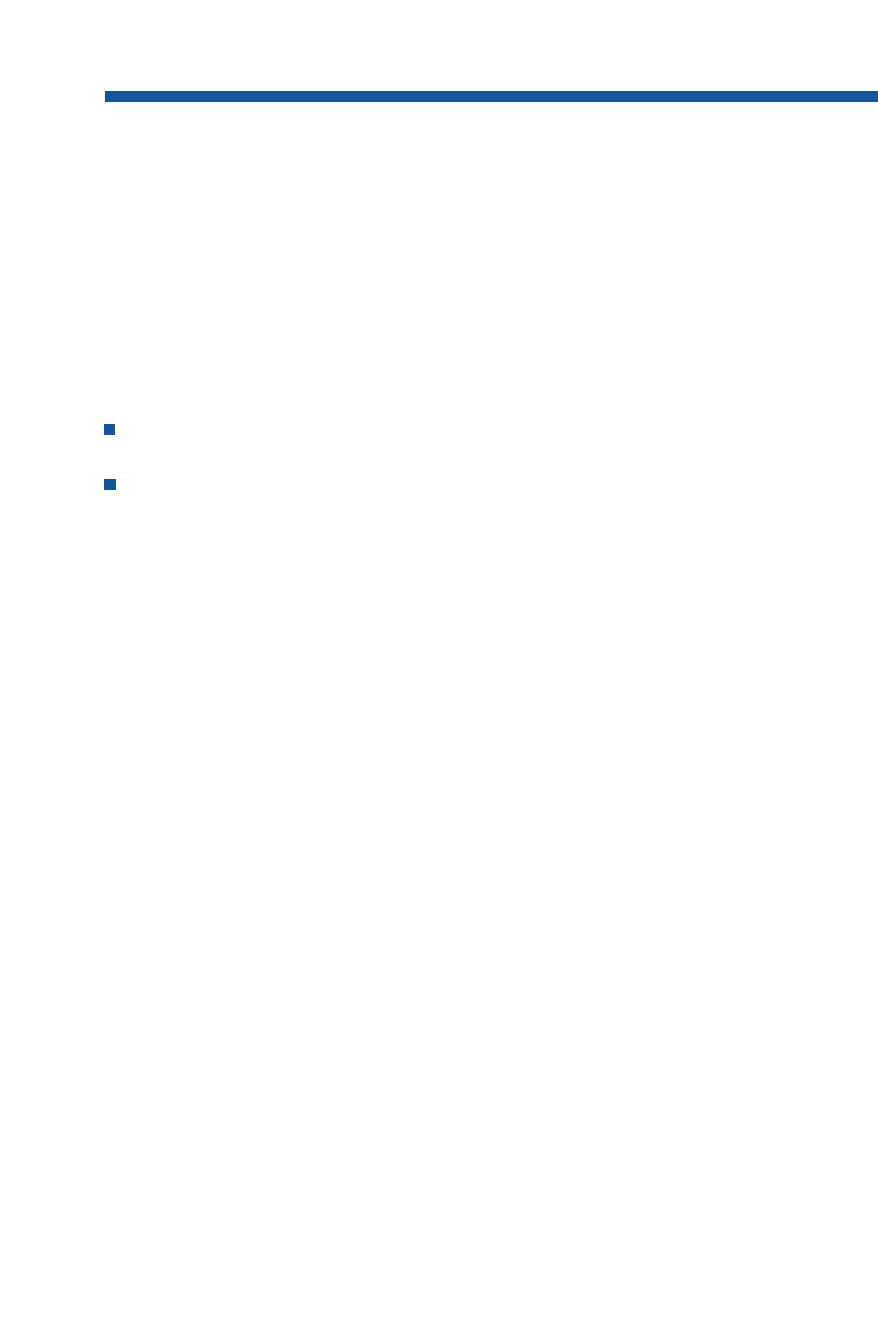
4Sheet metal forming and blanking
4.9Organization of stamping plants
4.9.1Design
Sheet metal stamping plants are among the most capital-intensive of all
manufacturing installations in industry. The high degree of investment
necessary and long-term commitment to selected manufacturing meth-
ods mean that careful investment and production planning are essen-
tial. In the production of sheet metal parts using deep drawing, stretch
drawing and blanking processes, major criteria include part accuracy,
die life, line output and its availability. The implementation of mea-
sures for continuous in-process quality assurance using suitable sensor
technology allows objective assessment of part quality (cf. Sect. 4.9.3).
Stamping plants generally comprise different sheet metal process-
ing equipment, each of which manufactures a certain range of parts
(Fig. 4.9.1).The aim of efficient stamping plant layout is to ensure the
most economical operation possible. The selection of the individual
equipment depends primarily on the size, shape and metal forming
requirements imposed on the components, as well as the planned
batch sizes.
The sheet metal is supplied from the rolling mill in the form of coil.
When producing medium-sized to large parts such as bathtubs, sinks,
car doors or roofs, a separate blanking line cuts the blanks from the coil
stock and stacks them (cf. Fig.4.6.5).The blanks are destacked by the
blankloader (cf. Fig. 4.4.15and 4.4.16)and fed individually and auto-
matically into the press where they are formed. Due to its high capacity,
a blanking line is able to service several press lines (cf. Fig. 4.4.19)or
large-panel transfer presses (cf. Fig. 4.4.27and 4.4.38).
Metal Forming Handbook / Schuler (c) Springer-Verlag Berlin Heidelberg 1998