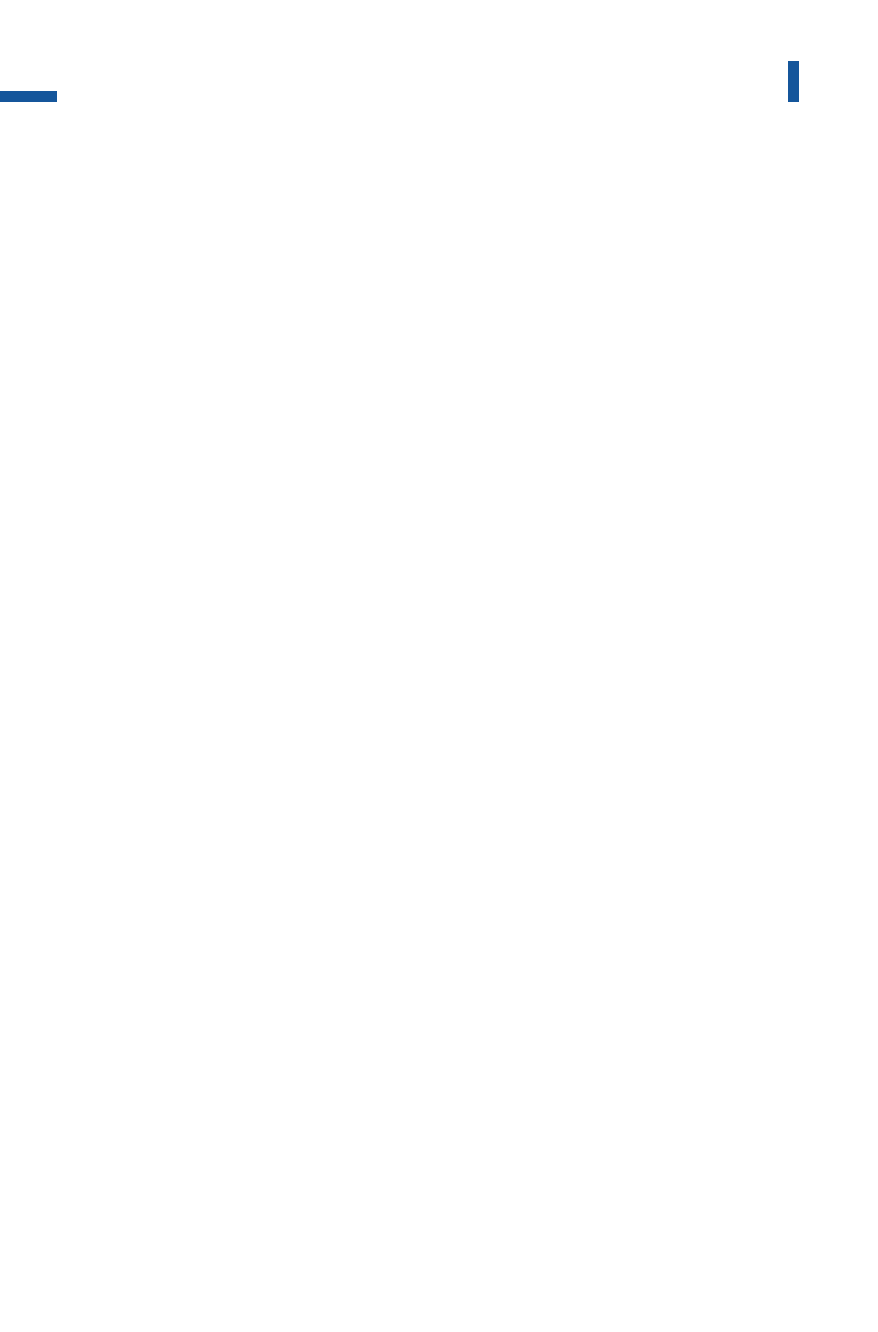
operations. The machines require a controlled movement sequence
with a precise top dead center (Fig.4.7.4).The narrow blanking clear-
ance of the dies must not change even under high levels of stress. Fine
blanking presses are, therefore, required to comply with stringent preci-
sion requirements for example regarding slide gibs, high frame rigidity
and the parallelism of die clamping surfaces. Both mechanical and
hydraulic systems are used for the main slide drive.
Machine layout and drive system
In standard configuration, mechanical presses (Fig.4.7.27)are equipped
with a “combination bed” for the tool systems of moving and fixed punch
(Fig. 4.7.23and 4.7.24). Making use of the straight-side principle, the
monobloc press frame as a welded construction offers good dimensional
rigidity and freedom from vibrations (cf. Fig. 3.1.1). A clearance-free, pre-
tensioned slide gib is used (cf. Fig. 3.1.5).A central support in the upper
and lower die clamping plate ensures optimum die support and introduc-
tion of forces to the die. A controlled, infinitely variable DC motor drives
the press via the flywheel, a disk clutch and a worm gear pair on two syn-
chronously running crankshafts with different eccentricity (Fig. 4.7.27).
The crankshafts drive a double knuckle-joint system which generates the
movement sequence of the slide required for fine blanking.
This drive system is particularly suited for material thicknesses
between approx. 1 and 8 mm, and total press forces of up to 2,500 kN.
The vee-ring force and counterforce are applied by hydraulic systems.
The mechanical drive system is characterized by the following factors:
–a fixed slide movement sequence with constant stroke and precise
position of the top and bottom dead center,
–low energy consumption,
–high output depending on the size of the press with stroking rates of
up to 140/min,
–minimal setting and maintenance input.
The press body of hydraulic presses comprises a robust monobloc welded
straight-side construction with high rigidity (Fig. 4.7.28andcf. Fig. 3.1.1).
This is achieved by implementing suitable design measures such as selec-
tion of large upright cross-sections and large ribs. The slide and main
piston together form a unit which is integrated in the press bed. The
slide is guided in the press body and the lower part of the slide piston.
360
Sheet metal forming and blanking
Metal Forming Handbook / Schuler (c) Springer-Verlag Berlin Heidelberg 1998