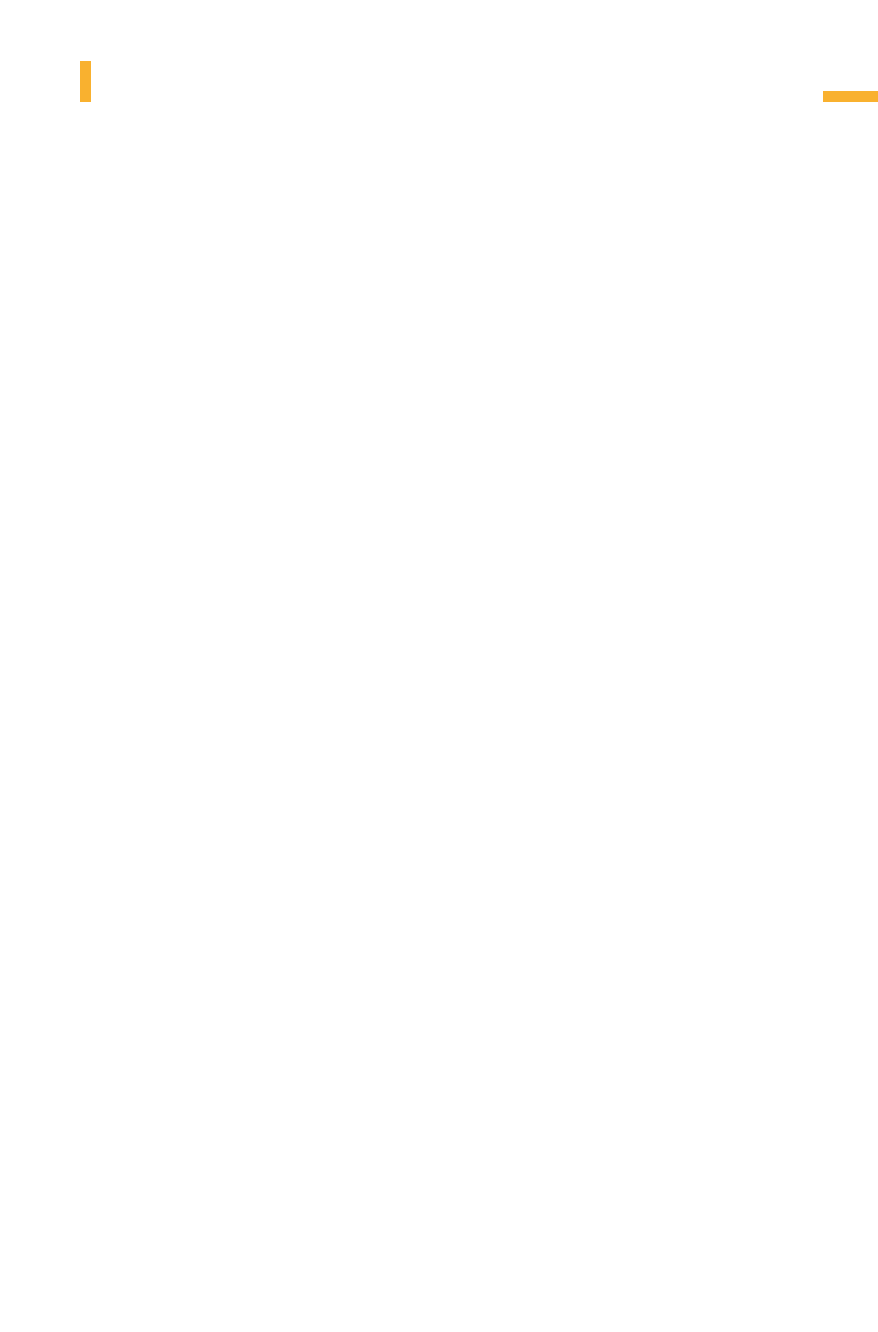
face of the component. Tube ends must be deburred for the same rea-
son, although chamfers must be avoided under any circumstances.
The ideal preform for the hydroforming process is a straight cylindri-
cal tube. However, deviations from this shape are common, as the tube
must be laid adequately in the die in order to ensure part quality. This
necessitates a pre-formingprocess. On principle, any pre-forming process
reduces subsequent formability and leads to differences in the wall
thickness and faults in the forming behavior of the parts as a result of
local strain hardening. However, suitable configuration of the compo-
nent and optimum selection of the pre-forming process can counteract
these negative effects.
Bendingis performed on a mandrel, profile, cam or induction bend-
ing machine depending on the bending radius, tube diameter and wall
thickness (cf.Sect.4.8). Because of the notching effects that may oc-
cur, surface damage, in particular sharp-edged impressions created by
clamping jaws, may lead to premature bursting of the component. The
tolerance for the straight ends, as for cutting, is +/– 0.5 mm. Bending
errors, such as wrinkles on inside bends, impressions left by clamping
jaws or drawing grooves must be avoided, particularly in the case of
thin-walled tubular blanks.
Reduction and expansionprocesses are used where large peripheral dif-
ferences are required on long elongated components or in case of par-
tial oversize of the used tube in the central section. Here, too, process-
specific defects such as grooves, impressions etc. could have a detri-
mental effect.
Pre-forming in the hydroform dierepresents an ideal solution if it can
eliminate any other pre-forming steps required on the straight tube.
Pre-forming is also carried out on parts which have been previously
bent, expanded or reduced.
Pre-forming in the dieis used in the case of complex geometries, where
the above processes fail to produce satisfactory results.
Special processes also exist for tapered, welded tubes, welded tubes
with non-round sections, deep-drawn half shells, extruded sections and
joined tubes. In the case of complex components, several pre-forming
steps can be necessary.
425
Materials and preforms for producing hydroformed components
Metal Forming Handbook / Schuler (c) Springer-Verlag Berlin Heidelberg 1998