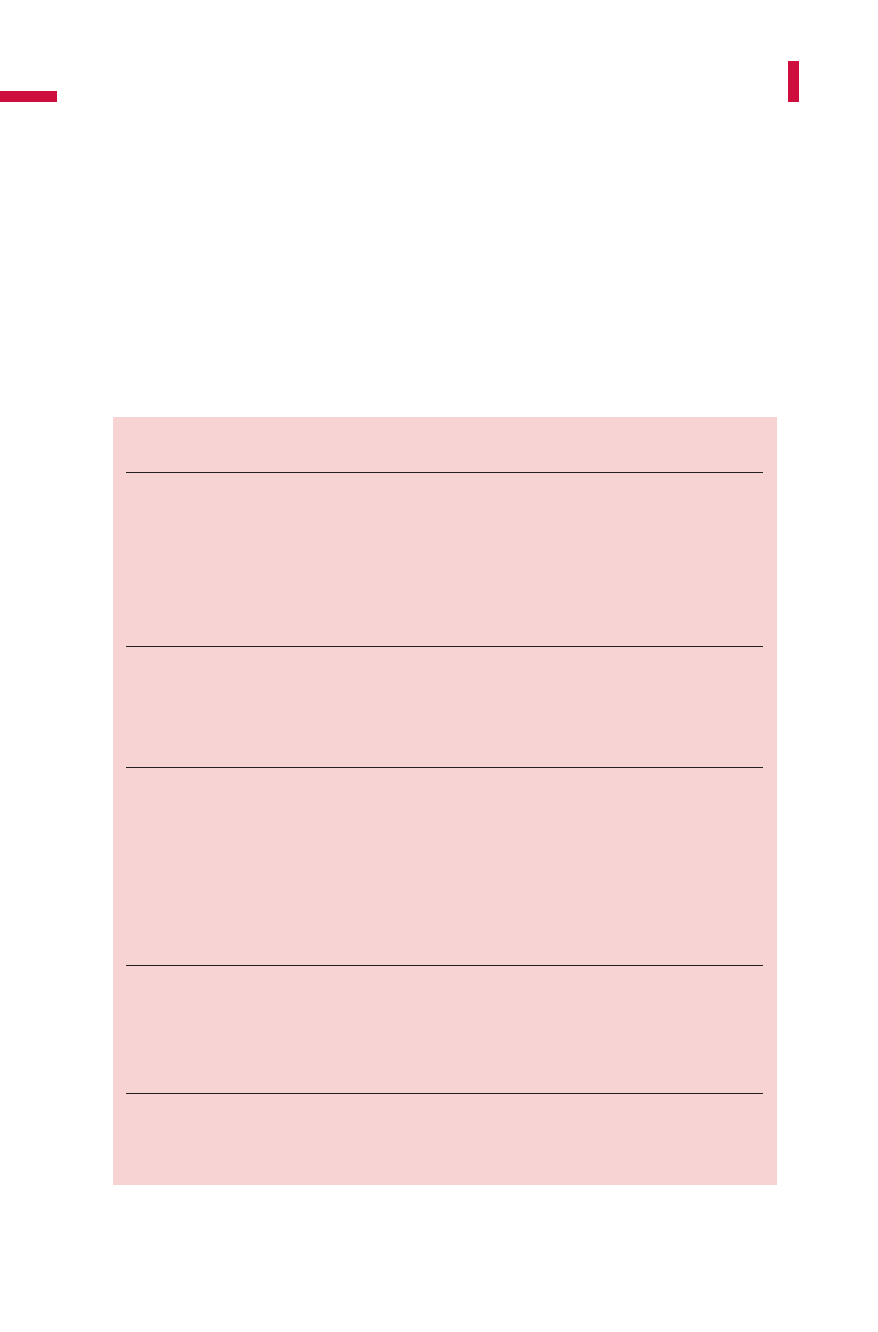
importance of the human factor here, this has been included as a sepa-
rate item in Table 6.2.1. The skill of the press operator is paramount in
the successful operation of the production system. He/she takes the
influencing factors into account and evaluates them.
Tolerances
Achievable ISO tolerances for different types of cold forging and com-
plementary processes are summarized in Table 6.2.2. The “variation
444
Solid forming (Forging)
Table 6.2.1: Classification of process parameters that affect the geometrical accuracy and surface
quality of a forged part
Line: Machine kinematics, stiffness, off-center load
capacity, gib precision, heating behavior
(warm), natural frequency
Automation weight control, careful feed and discharge,
positioning accuracy, transfer, press force
control
Heating type, temperature, temperature control
Cooling temperature control
Billet: Starting material analysis, strength, microstructure
Material form
wire, bar, thick sheet; rolled, peeled or drawn
Manufacturing process shearing, sawing, blanking
Pre-treatment possibly soft-annealing, pickling,
phosphating, coating
Process: Processing sequence
No. of steps single-step, multiple-step, process
combination
Temperature hot (h), cold (c), warm (w)
Intermediate treatment recrystallization, normalization (warm),
pickling, phosphating, coating
Lubrication and cooling additional lubrication, spraying, flooding
(warm), lubricant and coolant (warm)
Clearance for part transport
Die: Precision die concept, details, production process,
adjustment of upper and lower die,
mechanical die deflection, thermal die
expansion
Wear die material, surface, coating, change
interval
Human element: Die designer,
die manufacturer,
operating staff,
training and instruction specialized skills
Metal Forming Handbook / Schuler (c) Springer-Verlag Berlin Heidelberg 1998