Подождите немного. Документ загружается.
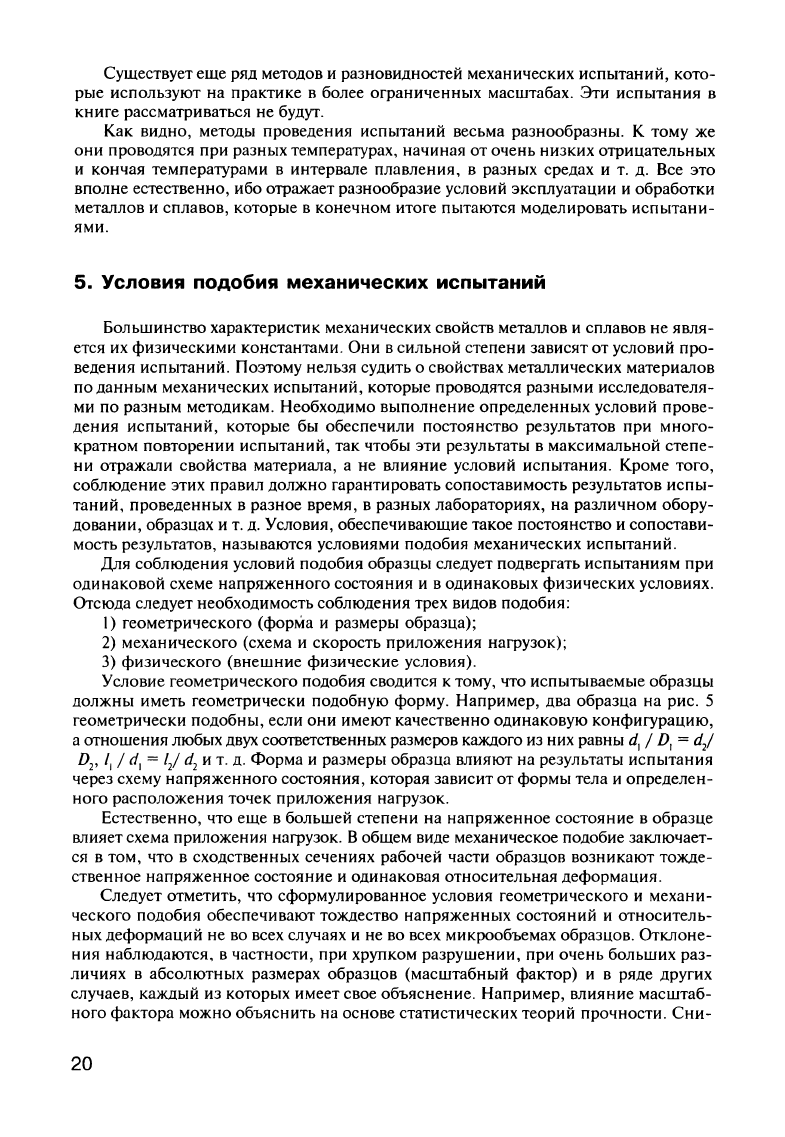
Существует
еще
ряд методов
и
разновидностей
механических
испытаний,
кото
рые
используют
на
практике
в
более
ограниченных
масштабах.
Эти
испытания
в
книге
рассматриваться
не
будут.
Как
видно,
методы
проведения
испытаний
весьма
разнообразны.
К
тому
же
они
проводятся
при
разных
температурах,
начиная
от
очень
низких
отрицательных
и
кончая
температурами
в
интервале
плавления,
в
разных
средах
и
т.
д.
Все
это
вполне
естественно,
ибо
отражает
разнообразие
условий
эксплуатации
и
обработки
металлов и
сплавов,
которые
в
конечном
итоге
пытаются
моделировать
испытани
ями.
5.
Условия
подобия
механических
испытаний
Большинство
характеристик
механических
свойств
металлов
и
сплавов
не
явля
ется
их
физическими
константами.
Они
в
сильной
степени
зависят
от
условий
про
ведения
испытаний.
Поэтому
нельзя судить
о
свойствах
металлических
материалов
по
данным
механических
испытаний,
которые
проводятся
разными
исследователя
ми
по
разным
методикам.
Необходимо
выполнение
определенных
условий
прове
дения
испытаний,
которые
бы
обеспечили
постоянство
результатов
при
много
кратном
повторении
испытаний,
так
чтобы
эти
результаты
в
максимальной
степе
ни
отражали
свойства
материала,
а
не
влияние
условий
испытания.
Кроме
того,
соблюдение
этих
правил
должно
гарантировать
сопоставимость
результатов
испы
таний,
проведенных
в
разное
время,
в
разных
лабораториях,
на
различном
обору
довании,
образцах
и
т.
д.
Условия,
обеспечивающие
такое
постоянство
и
сопостави
мость
результатов,
называются
условиями
подобия
механических
испытаний.
Для
соблюдения
условий
подобия образцы
следует
подвергать
испытаниям
при
одинаковой
схеме
напряженного
состояния
и
в
одинаковых
физических
условиях.
Отсюда
следует
необходимость
соблюдения
трех
видов
подобия:
1)
геометрического
(форма
и
размеры
образца);
2)
механического
(схема
и
скорость
приложения
нагрузок);
3)
физического
(внешние
физические
условия).
Условие
геометрического
подобия
сводится
к
тому,
что
испытываемые
образцы
должны
иметь
геометрически
подобную
форму.
Например,
два
образца
на
рис.
5
геометрически
подобны,
если
они
имеют
качественно
одинаковую
конфигурацию,
а
агношения
любых
двух
соответственных
размеров
каждого
из
них
равны
d)
I
D)
=
d/
D
2
,
1)
I
d)
=
1/
d
2
И
т.
д.
Форма
и
размеры
образца
влияют
на
результаты
испытания
через
схему
напряженного
состояния,
которая зависит
от
формы
тела
и
определен
ного
расположения
точек
приложения
нагрузок.
Естественно,
что
еще
в
большей
степени
на
напряженное
состояние
в
образце
влияет
схема
приложения
нагрузок.
В
общем
виде
механическое
подобие
заключает
ся
в
том,
что
в
сходственных
сечениях
рабочей
части
образцов
возникают
тожде
ственное
напряженное
состояние
и
одинаковая
относительная
деформация.
Следует
отметить,
что
сформулированное
условия
геометрического
и
механи
ческого
подобия
обеспечивают
тождество
напряженных
состояний
и
относитель
ных
деформаций
не
во
всех
случаях
и
не
во
всех
микрообъемах
образцов.
Отклоне
ния
наблюдаются.
в
частности,
при
хрупком
разрушении,
при
очень
больших
раз
личиях
в
абсолютных
размерах
образцов
(масштабный
фактор)
и
в
ряде
других
случаев,
каждый
из
которых
имеет
свое
объяснение.
Например,
влияние
масштаб
ного
фактора
можно
объяснить
на
основе
статистических
теорий
прочности.
Сни-
20
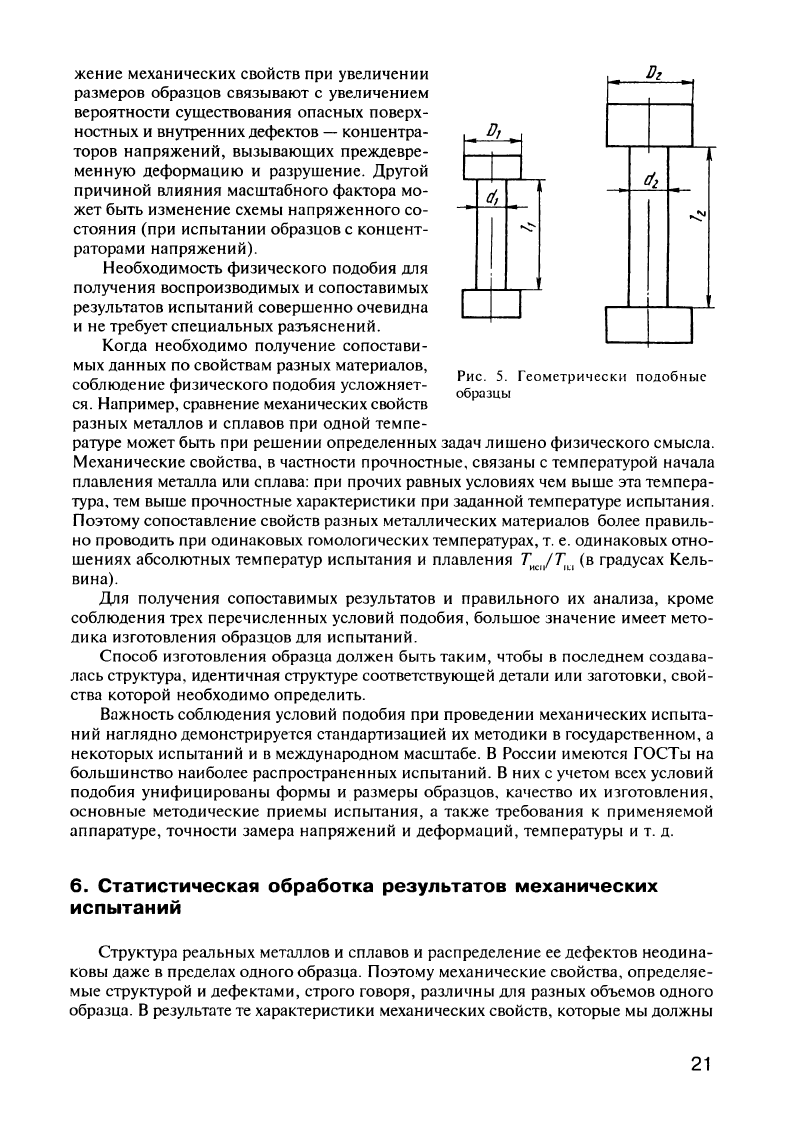
жение
механических
свойств
при
увеличении
размеров
образцов
связывают
с
увеличением
вероятности
существования
опасных
поверх
ностных
и
внутренних
дефектов
-
кониентра
торов
напряжений,
вызывающих
преждевре
менную
деформацию
и
разрушение.
Другой
причиной
влияния
масштабного
фактора
мо
жет быть
изменение
схемы
напряженного
со
стояния
(при
испытании
образцов
с
концент
раторами
напряжений).
Необходимость
физического
подобия
для
получения
воспроизводимых
и
сопоставимых
результатов
испытаний
совершенно
очевидна
и
не
требует
спеuиальных
разьяснениЙ.
Когда
необходимо
получение
сопостuви
мых
данных
по
свойствам
разных
материалов,
соблюдение
физического
подобия
усложняет
ся.
Например,
сравнение
механических
свойств
разных
металлов и
сплавов
при
одной
темпе-
О!
tIZ
d,
~
Рис.
5.
ГеомеТРИ'lеСКII
подобные
образцы
ратуре
может
быть
при
решении
определенных
задач
лишено
физического
смысла.
Механические
свойства,
в
частности
прочностные,
связаны
с
температурой
начала
плавления
металла
или
сплава:
при
прочих
равных
условиях
чем
выше
эта
темпера
тура,
тем
выше
прочностные
характеристики
при
заданной
температуре
испытания.
Поэтому
сопоставление
свойств
разных
металлических
материалов
более
правиль
но
проводить
при
одинаковых
гомологических
температурах,
т. е.
одинаковых
отно
шениях
абсолютных
температур
испытания
и
плавления
ТИС/Т'"
(в
градусах
Кель
вина).
Для
получения
сопоставимых
результатов
и
правильного
их
анализа,
кроме
соблюдения
трех
перечисленных
условий
подобия,
большое
значение
имеет
мето
дика
изготовления
образцов
для
испытаний.
Способ
изготовления
образца
должен
быть
таким,
чтобы
в
последнем
создава
лась
структура,
идентичная
структуре
соответствуюшей
детали
или
заготовки,
свой
ства
которой
необходимо
определить.
Важность
соблюдения
условий
подобия
при
проведении
механических
испыта
ний
наглядно
демонстрируется
стандартизацией
их
методики
в
государственном,
а
некоторых
испытаний
и
в
международном
масштабе.
В
России
имеются
ГОСТы
на
большинство
наиболее
распространенных
испытаний.
В
них
с
учетом
всех
условий
подобия
унифицированы
формы
иразмеры
образцов,
качество
их
изготовления,
основные
методические
приемы
испытания,
а
также
требования
к
применяемой
аппаратуре,
точности
замера
напряжений
и
деформаций,
температуры
и
т.
д.
б.
Статистическая
обработка
результатов
механических
испытаний
Структура
реальных
металлов
и
сплавов
и
распределение
ее
дефектов
неодина
кьвы
даже
в
пределах
одного
образца.
Поэтому
механические
свойства,
определяе
мые
структурой
и
дефектами,
строго
говоря,
различны
для
разных
объемов
одного
образца.
В
результате
те
характеристики
механических
свойств,
которые
мы
должны
21
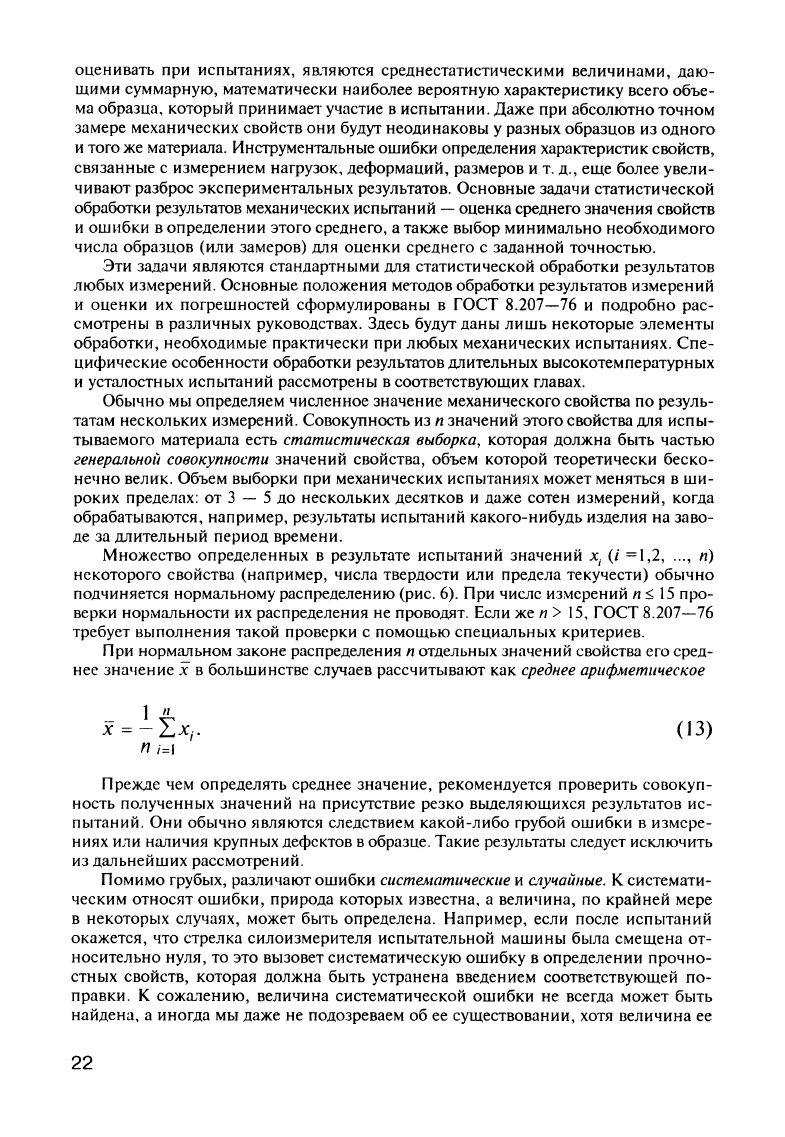
оценивать
при
испытаниях,
являются
среднестатистическими
величинами,
даю
щими
суммарную,
математически
наиболее
вероятную
характеристику
всего
объе
ма
образца,
который
принимает
участие
в
испытании.
Даже
при
абсолютно
точном
замере
механических
свойств
они
будут
неодинаковы
у
разных
образцов
из
одного
и
того
же
материала.
Инструментальные
ошибки
определения
характеристик
свойств,
связанные
с
измерением
нагрузок,
деформаций,
размеров
и
т.
д.,
еще
более
увели
чивают
разброс
экспериментальных
результатов.
Основные
задачи
статистической
обработки
результатов
механических
испытаний
-
оценка
среднего
значения
свойств
и
ошибки
в
определении
этого
среднего,
а
также
выбор
минимально
необходимого
числа
обра.зцов
(или замеров)
для
оценки
среднего
с
заданной
точностью.
Эти
задачи
являются
стандартными
для
статистической
обработки
результатов
любых
измерений.
Основные
положения
методов
обработки
результатов
измерений
и
оценки
их
погрешностей
сформулированы
в
ГОСТ
8.207-76
и
подробно
рас
смотрены
в
различных
руководствах.
Здесь будут
даны
лишь
некоторые
элементы
обработки,
необходимые
практически
при
любых
механических
испытаниях.
Спе
цифические
особенности
обработки
результатов
длительных
высокотемпературных
и
усталостных
испытаний
рассмотрены
в
соответствующих
главах.
Обычно
мы
определяем
численное
значение
механического
свойства
по
резуль
татам
нескольких
измерений.
Совокупность
из
n
значений
этого
свойства
для
испы
тываемого
материала
есть
статистическая
выборка,
которая
должна
быть
частью
генеральной
совокупности
значений
свойства,
объем
которой
теоретически
беско
нечно
велик.
Объем
выборки
при
механических
испытаниях
может
меняться
в
ши
роких
пределах:
от
3 - 5
до
нескольких
десятков
и
даже
сотен
измерений,
когда
обрабатываются,
например,
реЗУ,lьтаты
испытаний
какого-нибудь
изделия
на
заво
де
за
длительный
период
времени.
Множество
определенных
в
результате
испытаний
значений
Х
;
(i
=1,2, ... , n)
нскоторого
свойства
(например,
числа
твердости
или
предела
текучести)
обычно
подчиняется
нормальному
распределению
(рис.
6).
При
числс
измсрений
n
~
15
про
верки
нормальности
их
распределения
не
проводят.
Если
же
n >
15,
ГОСТ
8.207-76
требует
выполнения
такой
проверки
с
помощью
специальных
критериев.
При
нормальном
законе
распределения
n
отдельных значений
свойства
его
сред
нее
значение
х
в
большинстве
случаев
рассчитывают
как
среднее
арифметическое
1 n
Х
= -
Lx;.
n
;=1
(13)
Прежде
чем
определять
среднее
значение,
рекомендуется
проверить
совокуп
ность
полученных
значений
на
присутствие
резко
выделяющихся
результатов
ис
пытаний.
Они
обычно
являются
следствием
какой-либо
грубой
ошибки
в
измере
ниях
или
наличия
крупных
дефектов
в
образце.
Такие
результаты
следует
исключить
из
дальнейших
рассмотрений.
Помимо
грубых,
разлИ'IaЮТ
ошибки
систематичеСКllе
и случайные.
К
системати
ческим
относят
ошибки,
природа которых
известна,
а
величина,
по
крайней
мере
в
некоторых
случаях,
может
быть
определена.
Например,
если
после
испытаний
окажется, что
стрелка
силоизмерителя
испытательной
машины
была
смещена
от
носительно
нуля,
то
это
вызовет
систематическую
ошибку
в
определении
прочно
стных
свойств,
которая
должна
быть
устранена
введением
соответствующей
по
правки.
К
сожалению,
величина
систематической
ошибки
не
всегда
может
быть
найдена,
а
иногда
мы
даже
не
подозреваем
об
ее
существовании,
хотя
величина
ее
22
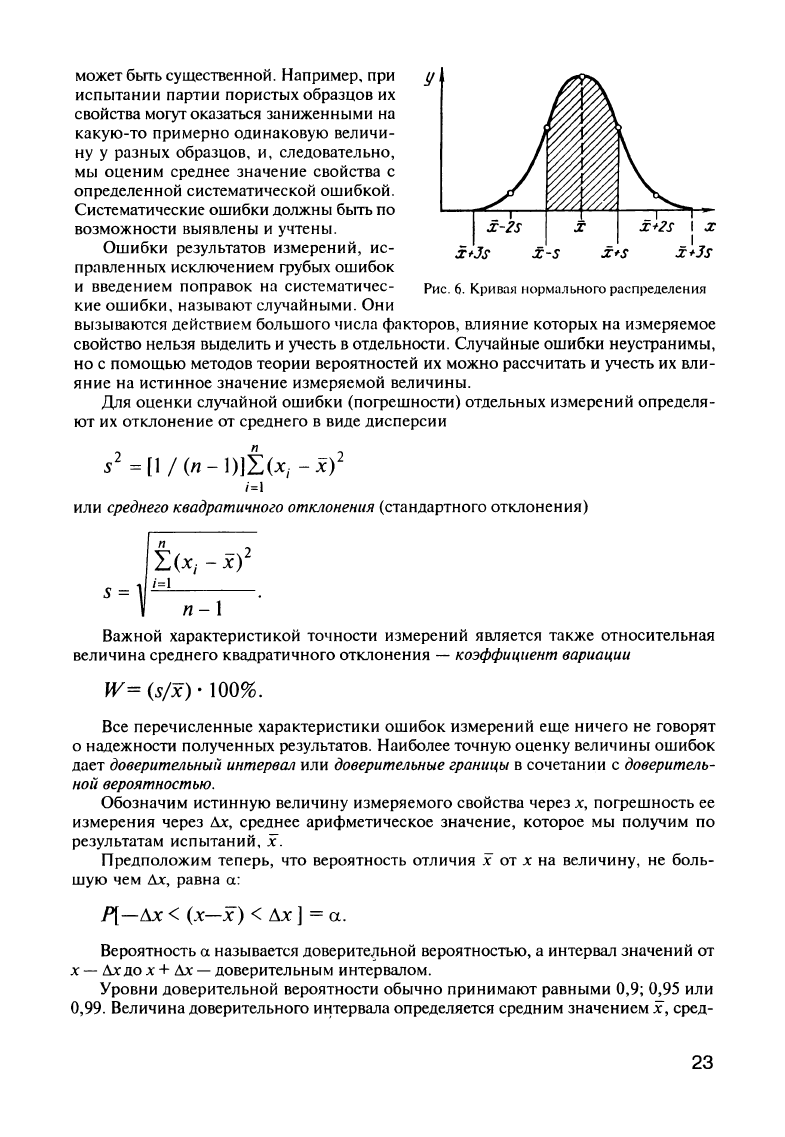
может
бьггь
существенной.
Например,
при
у
испытании
партии
пористых
образцов их
свойства могут
оказаться
заниженными
на
какую-то
примерно
одинаковую
величи-
ну
у
разных
образцов,
и,
следовательно,
мы
оценим
среднее
значение
свойства
с
определенной
систематической
ощибкоЙ.
Систематические
ошибки должны
БЬffb
ПО
возможности
выявлены
и
учтены.
Ошибки
результатов
измерений,
ис
правленных
исключением
грубых
ошибок
x-s
и
введением
поправок
на
систематичес-
Рис.
6.
Кривая
нормального
распределения
кие
ошибки,
называют
случайными.
Они
вызываются
действием
большого
числа
факторов,
влияние
которых
на
измеряемое
свойство
нельзя
выделить
и
учесть
в
отдельности.
Случайные
ошибки
неустранимы,
но
с
помощью
методов
теории
вероятностей
их
можно
рассчитать
и
учесть
их
вли
яние
на
истинное
значение
измеряемой
величины.
Для
оценки
случайной
ошибки
(погрешности)
отдельных
измерений
определя-
ют
их
отклонение
от
среднего
в
виде
дисперсии
2 n 2
S =
[1
j (n - 1)]L(X; -
х)
;=1
или
среднего
квадратичного
отклонения
(стандартного
отклонения)
s=
n
-1
Важной
характеристикой
точности
измерений
является
также
относительная
величина
среднего
квадратичного
отклонения
-
коэффициент
вариации
w=
(sjX)·
100%.
Все
перечисленные
характеристики
ошибок
измерений
еще
ничего
не
говорят
о
надежности
полученных
результатов.
Наиболее
точную
оценку
величины
ошибок
дает
доверительный
интервал
или
доверительные
границы
в
сочетании
с
доверитель
ной
вероятностью.
Обозначим
истинную
величину
измеряемого
свойства
через
Х,
погрешность
ее
измерения
через
М,
среднее
арифметическое
значение,
которое
мы
получим
по
результатам
испытаний,
Х.
Предположим
теперь,
что
вероятность
отличия
х
от
х
на
величину,
не
боль
шую
чем
м,
равна
а:
р[-М<
(х-х)
<
М]
=
а.
Вероятность
а
называется
доверите{lЬНОЙ
вероятностью,
а
интервал
значений
от
х
-
м
до х
+
м
-
доверительным
интервалом.
Уровни
доверительной
вероятности
обычно
принимают
равными
0,9; 0,95
или
0,99.
Величина
доверительного
ю,!тервала
определяется
средним
значением
х,
сред-
23
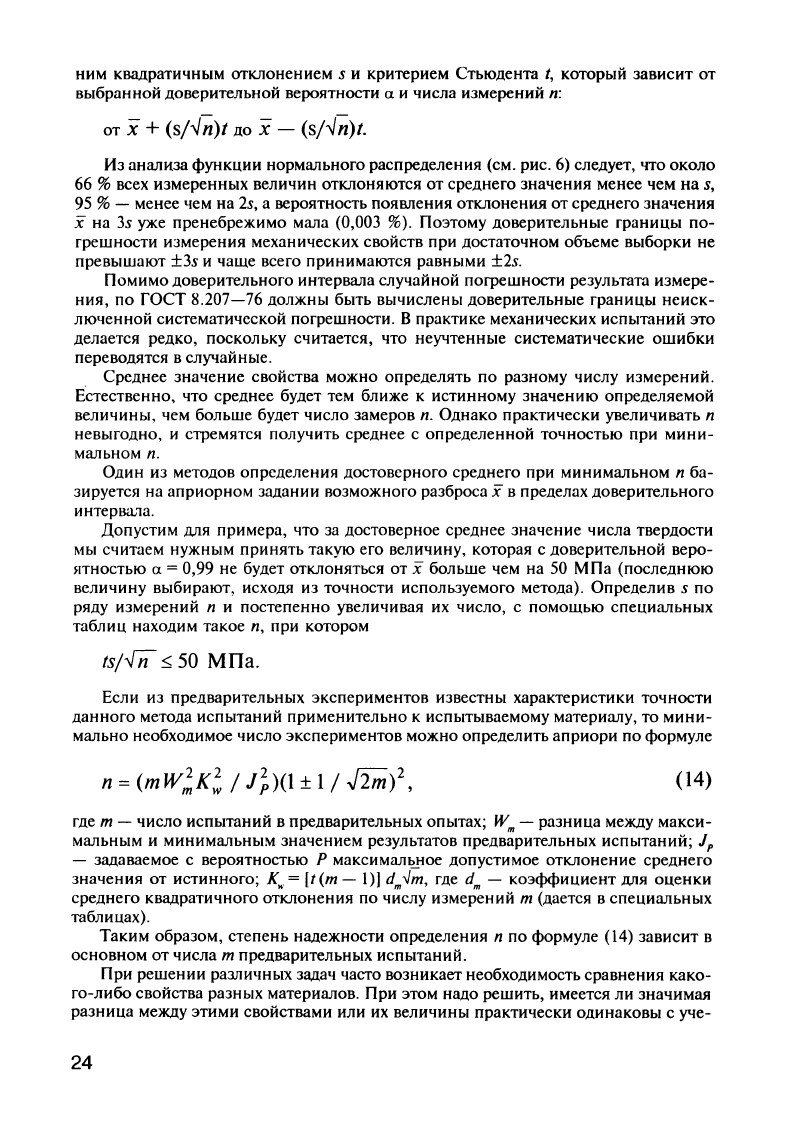
ним
квадратичным
отклонением
s
и
критерием
Стьюдента
t,
который
зависит
от
выбранной
доверительной
вероятности
а
И
числа
измерений
n:
Из
анализа
функции
нормального
распределения
(см.
рис.
6)
следует,
что
около
66
%
всех
измеренных
величин
отклоняются
от среднего
значения
менее
чем
на
s,
95
% -
менее
чем
на
2s,
а
вероятность
появления
отклонения
от
среднего
значения
хна
3s
уже
пренебрежимо
мала
(0,003 %).
Поэтому
доверительные
границы
по
грешности измерения
механических
свойств
при
достаточном
объеме
выборки
не
превышают
±3s
и
чаще
всего
принимаются
равными
±2s.
Помимо
доверительного
интервала
случайной
погрешности
результата
измере
ния,
по
ГОСТ
8.207-76
должны
быть
вычислены
доверительные
границы
неиск
люченной
систематической
погрешности.
В
практике
механических
испытаний
это
делается
редко,
поскольку
считается,
что
неучтенные
систематические
ошибки
переводятся
в
случайные.
Среднее
значение
свойства
можно
определять
по
разному
числу
измерений.
Естественно,
что
среднее
будет
тем
ближе
к
истинному
значению
определяемой
величины,
чем
больше
будет
число
замеров
n.
Однако
практически
увеличивать
n
невыгодно,
и
стремятся
получить
среднее
с
определенной
точностью
при
мини
мальном
n.
Один
из
методов
определения
достоверного
среднего
при
минимальном
n
ба
зируется на
априорном
задании
возможного
разброса
х
в
пределах
доверительного
интервала.
Допустим
для
примера,
что
за
достоверное
среднее
значение
числа
твердости
мы
счиr<lем
нужным
принять
такую
его
величину,
которая
с
доверительной
веро
ятностью
а
= 0,99
не
будет
отклоняться
от
х
больше
чем
на
50
МПа
(последнюю
величину
выбирают,
исходя
из
точности
используемого
метода).
Определив
s
по
ряду
измерений
n
и
постепенно
увеличивая
их
число,
с
помощью
специальных
таблиц
находим
такое
n,
при
котором
ts/Гп
~
50
МПа.
Если
из
предварительных
экспериментов
известны
характеристики
точности
данного
метода
испытаний
применительно
к
испытываемому
материалу,
то
мини
мально
необходимое
число
экспериментов
можно
определить
априори
по
формуле
(14)
где
т -
число
испытаний
в
предварительных
опытах;
W
m
-
разница
между
макси
мальным
и
минимальным
значением
результатов
предварительных
испытаний;
J
p
-
задаваемое
с
вероятностью
Р
максимал~ное
допустимое отклонение
среднего
значения
от
истинного;
K
w
=
[t(m
-
1)]
d
m
...Jm,
где
d
m
-
коэффициент
для
оценки
среднего
квадратичного
отклонения
по
числу
измерений
т
(дается
в
специальных
таблицах).
Таким
образом,
степень
надежности
определения
n
по
формуле
(14)
зависит
в
основном
от
числа
т
предварительных
испытаний.
При
решении
различных
задач
часто
возникает
необходимость
сравнения
како
го-либо
свойства
разных
материалов.
При
этом
надо
решить, имеется
ли
значимая
разница
между
этими
свойствами
или
их
величины
практически
одинаковы
с
уче-
24
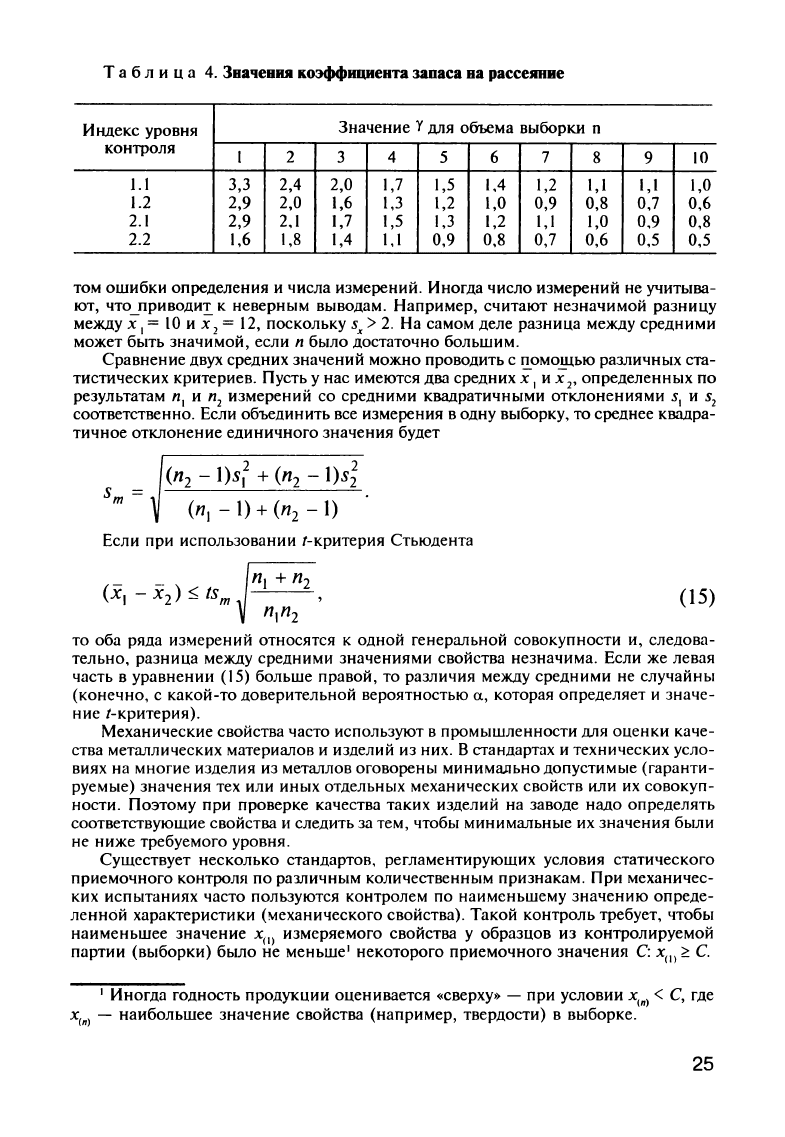
Т
а
б л и
ц
а
4.
ЗначенВJI
коэффициента
запаса
на
рассепне
Индекс
уровня
Значение
у
для
объема
выборки
n
контроля
1
2
3 4 5 6 7
8
9
10
1.1
3,3 2,4 2,0
1,7
1,5
1,4
1,2
1,1
1,1
1,0
1.2
2,9 2,0
1,6
1,3
1,2
1,0 0,9 0,8 0,7 0,6
2.1
2,9
2,1
1,7
1,5
1,3
1,2
1,1
1,0 0,9 0,8
2.2
1,6
1,8
1,4
1,1
0,9 0,8 0,7 0,6 0,5 0,5
том
ошибки
определения
и
числа измерений.
Иногда
число
измерений
не
учитыва
ют,
что_приводи!
к
неверным
выводам.
Например,
считают
незначимой
разницу
между
Х
I = 1
О
и
Х
2 =
12,
поскольку
S.
>
2.
На
самом
деле
разница
между
средними
может
быть
значимой,
если
n
было
достаточно
большим.
Сравнение
двух
средних
значений
можно
проводить
с
помошью
различных
ста
тистических
критериев.
Пусть
у
нас
имеются
два
средних
Х
1
И
Х
2
,
определенных
по
результатам
n
l
и
n
2
измерений
со
средними
квадратичными
отклонениями
SI
и
S2
соответственно.
Если
объединить
все
измерения
в
одну
выборку,
то
среднее
квадра
тичное
отклонение
единичного
значения
будет
s =
т
(n
2
-l)s~
+
(n
2
-
1)si
(n
l
-
1)
+ (n
2
-
1)
Если
при
использовании
t-критерия
Стьюдента
n
l
+ n
2
n'n
2
(15)
то
оба
ряда
измерений
относятся
к
одной
генеральной
совокупности
и,
следова
тельно,
разница
между
средними
значениями
свойства
незначима.
Если
же
левая
часть
в
уравнении
(15)
больше
правой,
то
различия
между
средними
не
случайны
(конечно,
с
какой-то
доверительной
вероятностью
а.,
которая
определяет
и
значе
ние
t-критерия).
Механические
свойства
часто
используют
в
промышленности
для
оценки
каче
ства
металлических
материалов
и
изделий
из
них.
В
стандартах
и
технических
усло
виях
на
многие
изделия
из
металлов
оговорены
минимально
допустимые
(гаранти
руемые)
значения
тех
или
иных
отдельных
механических
свойств
или
их
совокуп
ности.
Поэтому
при
проверке
качества
таких
изделий
на
заводе
надо
определять
соответствуюшие
свойства
и
следить
за
тем,
чтобы
минимальные
их
значения
были
не
ниже
требуемого
уровня.
Сушествует
несколько
стандартов,
регламентируюших
условия
статического
приемочного
контроля
по
различным
количественным
признакам.
При
механичес
ких
испытаниях
часто
пользуются
контролем
по
наименьшему
значению
опреде
ленной
характеристики
(механического
свойства).
Такой
контроль
требует,
чтобы
наименьшее
значение
X(I)
измеряемого
свойства
у
образцов
из
контролируемой
партии
(выборки)
было
не
меньше
l
некоторого
приемочного
значения
с:
X(I)
~
С.
I
Иногда
годность
продукции
оценивается
«сверху.
-
при
условии
Х(n)
<
С,
где
Х(n)
-
наибольшее
значение
свойства
(например,
твердости)
в
выборке.
25
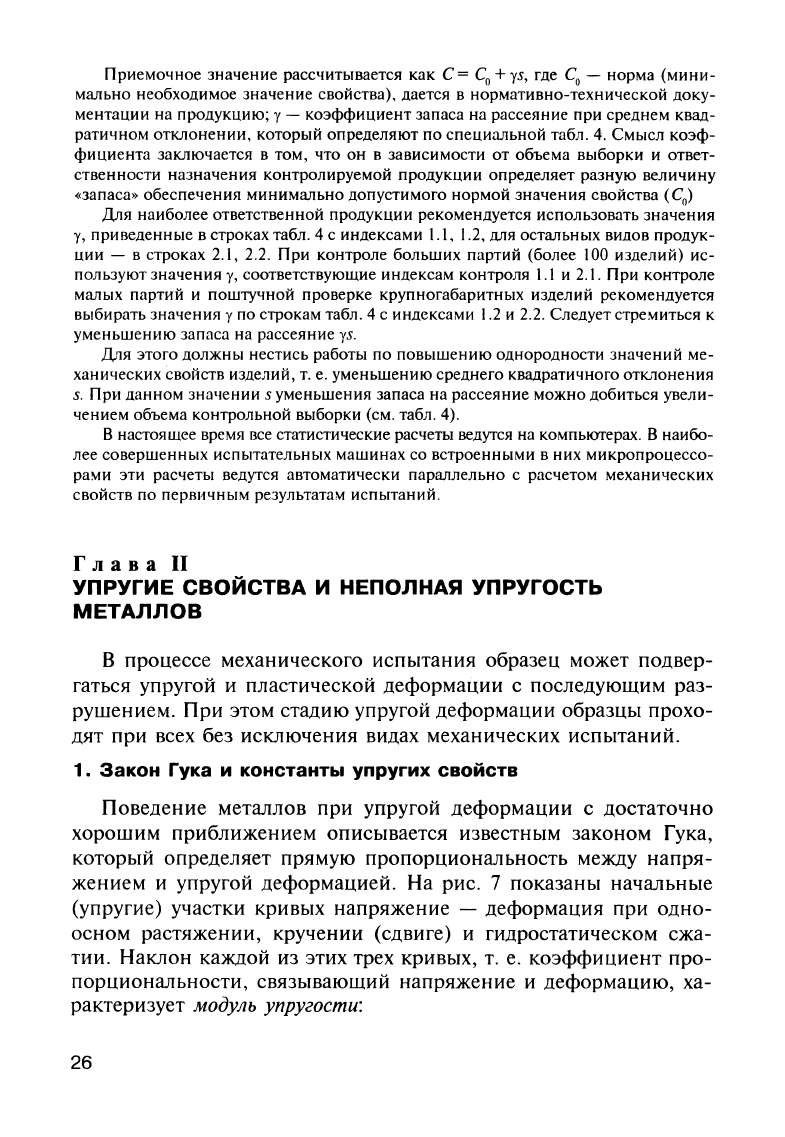
Приемочное
значение
рассчитывается
как
с=
СО
+
ys,
где
СО
-
норма
(мини
мально
необходимое
значение
свойства),
дается
в
нормативно-технической
доку
ментации
на
продукцию;
у
-
коэффициент
запаса
на
рассеяние
при
среднем
квад
ратичном
отклонении,
который
определяют по
специальной
табл.
4.
Смысл
коэф
фициента
заключается
в
том,
что
он
в
зависимости
от
объема
выборки
и
ответ
ственности
назначения
контролируемой
продукции
определяет
разную
величину
«запаса»
обеспечения
минимально
допустимого
нормой
значения
свойства
(Со)
Для
наиболее
ответственной
продукции
рекомендуется
использовать
значения
у,
приведенные
в
строках
табл.
4
с
индексами
1.1,
1.2,
для
остальных
видов
продук
ции
-
в
строках
2.1,2.2.
При
контроле
больших
партий
(более
100
изделий)
ис
пользуют
значения
у,
соответствующие
индексам
контроля
1.1
и
2.1.
При
контроле
малых
партий
и
поштучной
проверке
крупногабаритных
изделий
рекомендуется
выбирать
значения
у
по
строкам
табл.
4
с
индексами
1.2
и
2.2.
Следует
стремиться
к
уменьшению
запаса
на
рассеяние
ys.
Для
этого
должны
нестись
работы
по
повышению
однородности
значений
ме
ханических
свойств
изделий,
т.
е.
уменьшению
среднего
квадратичного
отклонения
s.
При
данном
значении
s
уменьшения
запаса
на
рассеяние
можно
добиться
увели
чением
объема
контрольной
выборки
(см.
табл.
4).
В
настоящее
время
все
статистические
расчеты
ведутся
на
компьютерах.
В
наибо
лее
совершенных
испытательных
машинах
со
встроенными
в
них
микропроцессо
рами
эти
расчеты
ведутся
автоматически
параллельно
с
расчетом
механических
свойств
по
первичным
результатам
испытаний.
Глава
11
УПРУГИЕ
СВОЙСТВА
И
НЕПОЛНАЯ
УПРУГОСТЬ
МЕТАЛЛОВ
в
процессе
механического
испытания
образец
может
подвер
гаться
упругой
и
пластической
деформации
с
последующим
раз
рушением.
При
этом
стадию
упругой
деформации
образцы
прохо
дят
при
всех
без
исключения
видах
механических
испытаний.
1.
Закон
Гука и
константы
упругих
свойств
Поведение
металлов
при
упругой
деформации
с
достаточно
хорошим
приближением
описывается
известным
законом
Гука,
который
определяет
прямую
пропорциональность
между
напря
жением
и
упругой
деформацией.
На
рис.
7
показаны
начальные
(упругие)
участки
кривых
напряжение
-
деформация
при
одно
осном
растяжении,
кручении
(сдвиге)
и
гидростатическом
сжа
тии.
Наклон
каждой
из
этих
трех
кривых,
т. е.
коэффициент
про
порциональности,
связывающий
напряжение
и
деформацию,
ха
рактеризует
модуль
упругости:
26
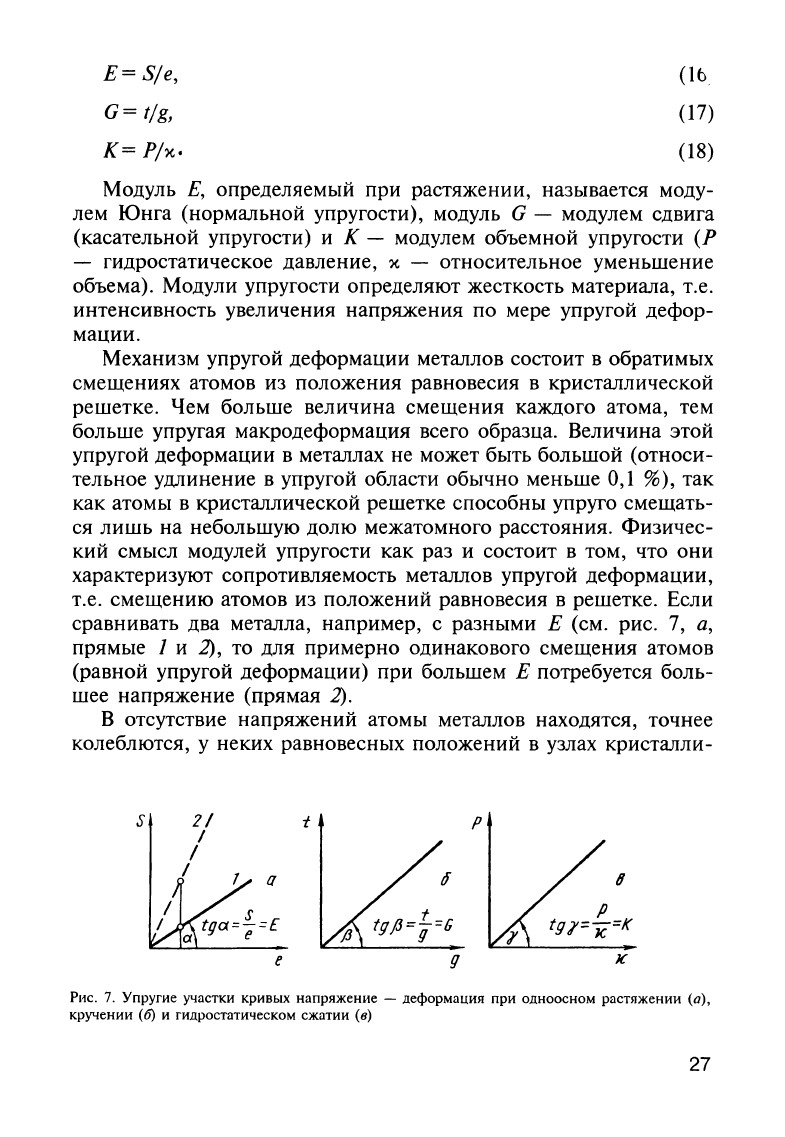
Е=
S/e,
G=
t/g,
К=
Р/х.
(l()
(17)
(18)
Модуль
Е,
определяемый
при
растяжении,
называется моду
лем
Юнга
(нормальной
упругости),
модуль
G -
модулем
сдвига
(касательной
упругости)
и
К -
модулем
объемной
упругости
(Р
-
гидростатическое
давление,
х
-
относительное
уменьшение
объема).
Модули
упругости
определяют
жесткость
материала,
т.е.
интенсивность
увеличения
напряжения
по
мере
упругой
дефор
мации.
Механизм
упругой
деформации
металлов
состоит
в
обратимых
смещениях
атомов
из
положения
равновесия
в
кристаллической
решетке.
Чем
больше
величина
смещения
каждого
атома,
тем
больше
упругая
макродеформация
всего
образца.
Величина
этой
упругой
деформации
в
металлах
не
может
быть
большой
(относи
тельное
удлинение
в
упругой
области
обычно
меньше
0,1
%),
так
как
атомы
в
кристаллической
решетке
способны
упруго
смещать
ся
лишь
на
небольшую
долю
межатомного
расстояния.
Физичес
кий
смысл
модулей
упругости
как
раз
и
состоит
в
том,
что
они
характеризуют
сопротивляемость
металлов
упругой
деформации,
т.е.
смещению
атомов
из
положений
равновесия
в
решетке.
Если
сравнивать
два
металла,
например,
с
разными
Е
(см.
рис.
7,
а,
прямые
1
и
2),
то
для
примерно
одинакового
смещения
атомов
(равной
упругой
деформации) при
большем
Е
потребуется
боль
шее
напряжение
(прямая
2).
в
отсутствие
напряжений
атомы
металлов
находятся,
точнее
колеблются,
у
неких
равновесных
положений
в
узлах
кристалли-
s
2/
/
/
/
q
е
f
р
6
р
tg}'=li=K
Рис.
7.
Упругие
участки
кривых
напряжение
-
деформация
при
одноосном
растяжении
(о),
кручении
(6)
и
гидростатическом
сжатии
(8)
27
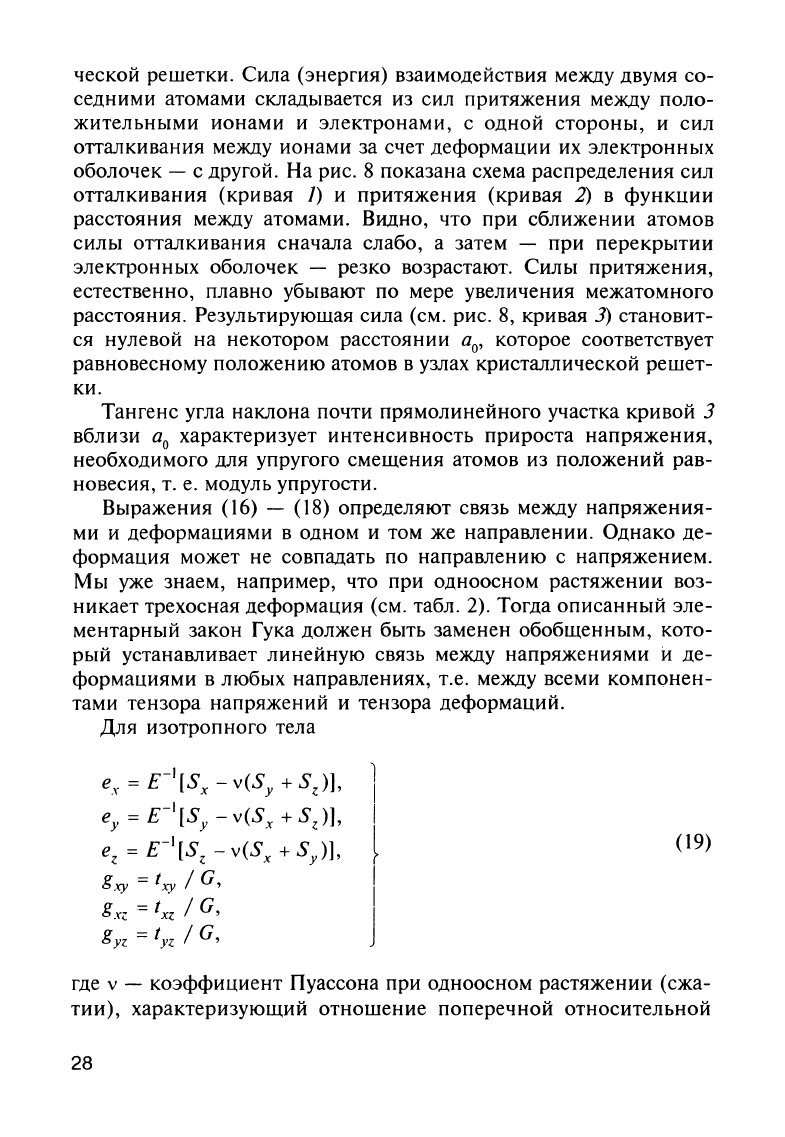
ческой
решетки.
Сила
(энергия)
взаимодействия
между
двумя
со
седними
атомами
складывается
из
сил
притяжения
между
поло
жительными
ионами
и
электронами,
с
одной
стороны,
и
сил
отталкивания
между
ионами
за
счет
деформации
их
электронных
оболочек
-
с
другой.
На
рис.
8
показана
схема
распределения
сил
отталкивания
(кривая
1)
и
притяжения
(кривая
2)
в
функции
расстояния
между
атомами.
Видно,
что
при
сближении
атомов
силы
отталкивания
сначала
слабо,
а
затем
-
при
перекрытии
электронных
оболочек
-
резко
возрастают.
Силы
притяжения,
естественно,
плавно
убывают
по
мере
увеличения
межатомного
расстояния.
Результирующая
сила
(см.
рис.
8,
кривая
З)
становит
ся
нулевой
на
некотором
расстоянии
00'
которое
соответствует
равновесному
положению
атомов
в
узлах
кристаллической
решет
ки.
Тангенс
угла
наклона
почти
прямолинейного
участка
кривой
3
вблизи
00
характеризует
интенсивность
прироста
напряжения,
необходимого
дЛя
упругого
смещения
атомов
из
положений
рав
новесия,
т. е.
модуль
упругости.
Выражения
(16) - (18)
определяют
связь
между
напряжения
ми
и
деформациями
в
одном
и
том
же
направлении.
Однако
де
формация
может
не
совпадать
по
направлению
с
напряжением.
Мы
уже
знаем,
например,
что
при
одноосном
растяжении
воз
никает
трехосная
деформация
(см.
табл.
2).
Тогда
описанный
эле
ментарный
закон
Гука
должен
быть
заменен
обобщенным,
кото
рый
устанавливает
линейную
связь
между
напряжениями
и
де
формациями
в
любых
направлениях,
т.е.
между
всеми
компонен
тами
тензора
напряжений
и
тензора
деформаций.
Для
изотропного
тела
е'(
= E-1[Sx -
v(Sy
+ Sz)],
1,'
е
у
= E-1[Sy
-v(Sх
+sz)],
e
z
= E-1[Sz -
v(Sx
+ Sy)],
,~
gxy
=
(ху
/ G,
gxz
=lxz
/G,
J'
gyz=lyz/G,
(19)
где
v -
коэффициент
Пуассона
при
одноосном
растяжении
(сжа
тии),
характеризующий
отнощение
поперечной
относительной
28
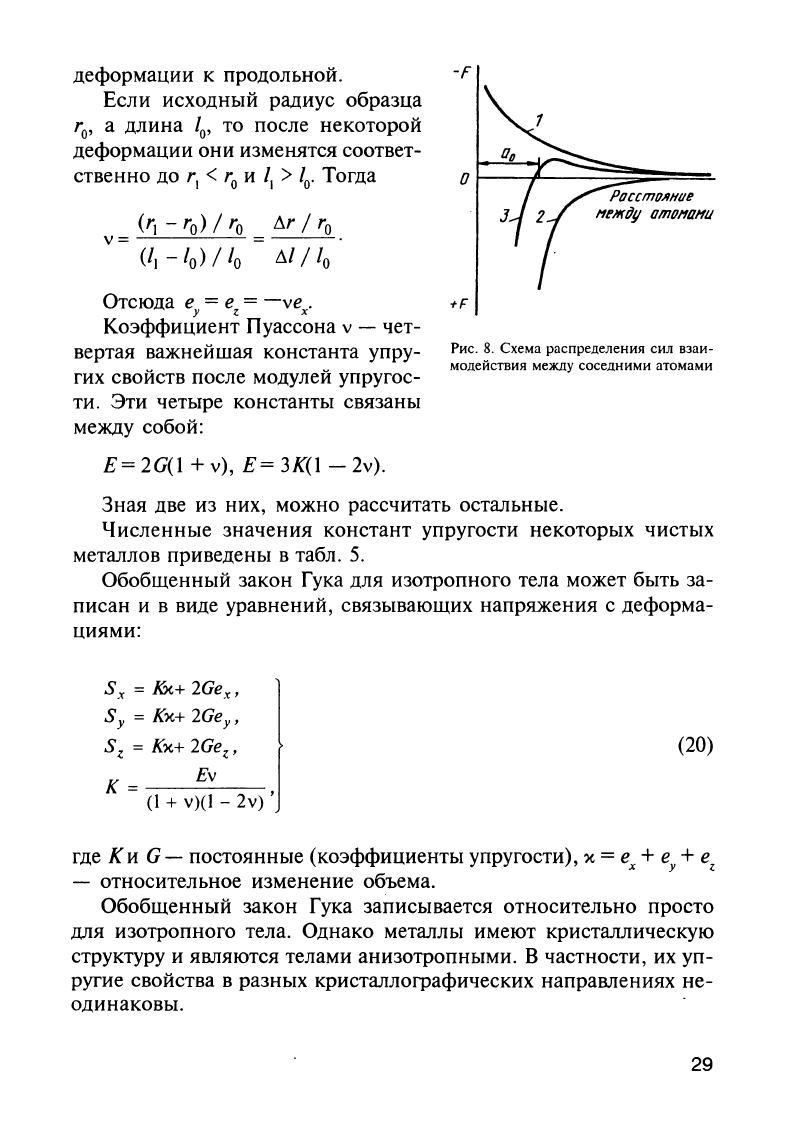
деформации
к
продольной.
-F
Если
исходный
радиус
образца
го'
а
длина
10'
то
после
некоторой
деформации
они
изменятся
соответ-
ственно
дО
Г\
<
ГО
И
1\
>
10.
Тогда
о
I=:::::~:::::::::;~=~==-
Отсюда
е
=
е
=
-ve
.
у z х
Коэффициент
Пуассона
v -
чет-
вертая
важнейшая
константа
упру
гих
свойств
после
модулей
упругос
ти.
Эти
четыре
константы
связаны
между
собой:
Е=
2G(1 + v), Е=
3К(1
- 2v).
+F
РоссmО.llнuе
Hl'lКtJy
оmононu
Рис.
8.
Схема
распределения
сил
взаи
модействия
между
соседними
атомами
Зная
две
из
них,
можно
рассчитать
остальные.
Численные
значения
констант
упругости
некоторых
чистых
металлов
приведены
в
табл.
5.
Обобщенный
закон
Гука
для
изотропного
тела
может
быть
за
писан
и
в
виде
уравнений,
связывающих
напряжения
с
деформа
циями:
Sx
=
Кх+
2Ge
x
,
Sy
=
Кх+
2Ge
y
,
Sz
=
Кх+
2Ge
z
'
К
= Ev ,
(1
+ v)(l -
2v)
(20)
где
Ки
G-
постоянные
(коэффициенты
упругости),
х
=
е
х
+
е
у
+ e
z
-
относительное
изменение
объема.
Обобщенный
закон
Гука
записывается
относительно
просто
для
изотропного
тела.
Однако
металлы
имеют
кристаллическую
структуру
и
являются
телами
анизотропными.
В
частности,
их
уп
ругие
свойства
в
разных
кристаллографических
направлениях
не
одинаковы.
29