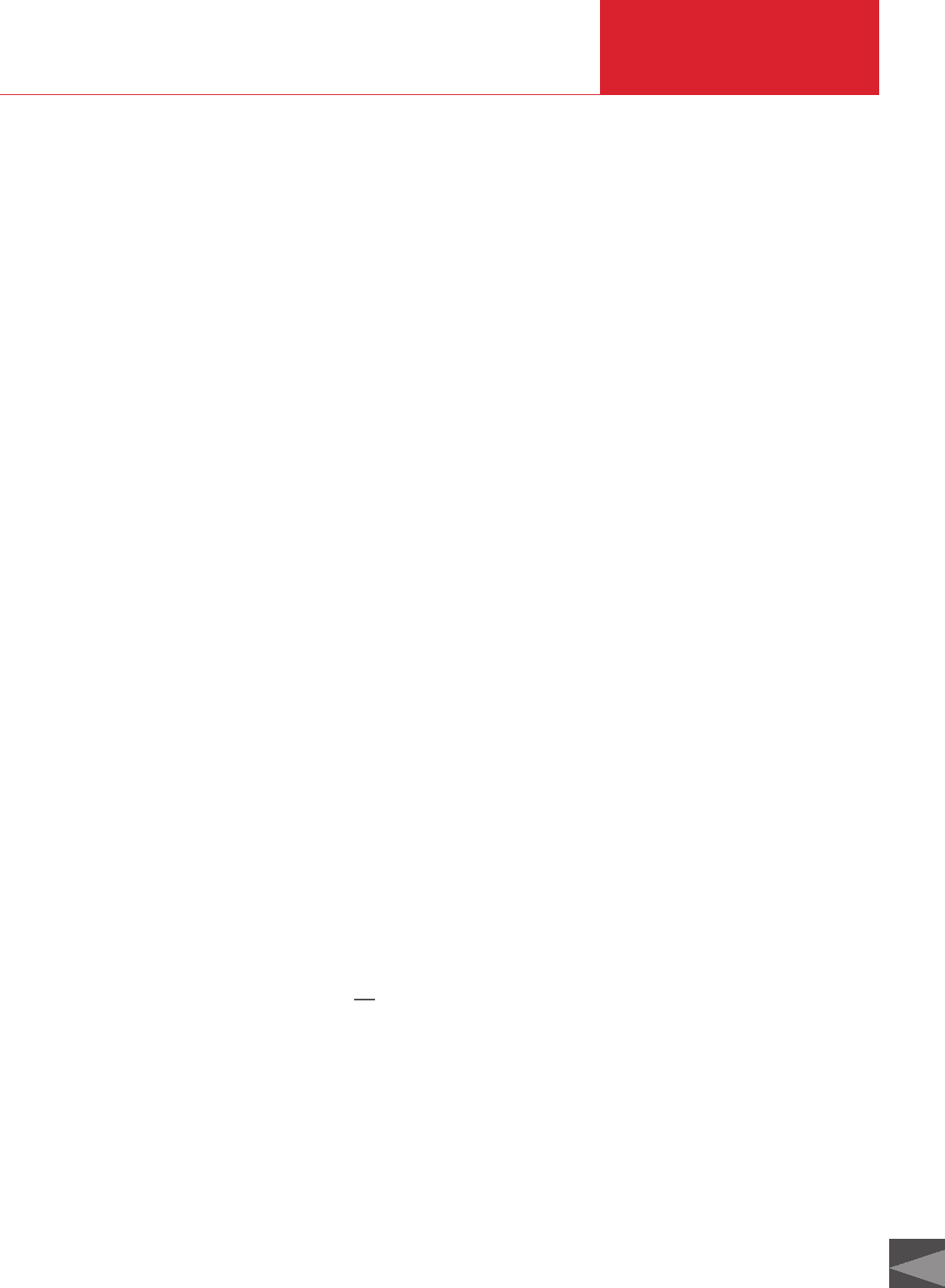
Vacuum Generation
Fundamentals of Vacuum Technology
D00.61
LEYBOLD VACUUM PRODUCTS AND REFERENCE BOOK 2001/2002
rotary vane pumps should be used. The
small amount of oil vapor that back-
streams out of the inlet ports of these
pumps can be almost completely removed
by a sorption trap (see Section 2.1.4)
inserted in the pumping line.
b) Medium vacuum region
(1 to 10
-3
mbar)
For the pumping of large quantities of gas
in this pressure region, vapor ejector
pumps are by far the most suitable. With
mercury vapor ejector pumps, completely
oil-free vacua can be produced. As a pre-
caution, the insertion of a cold trap chilled
with liquid nitrogen is recommended so
that the harmful mercury vapor does not
enter the vessel. With the medium vacuum
sorption traps described under a), it is
possible with two-stage rotary vane
pumps to produce almost oil-free vacua
down to below 10
-4
mbar.
Absolutely oil-free vacua may be produced
in the medium vacuum region with
adsorption pumps. Since the pumping
action of these pumps for the light noble
gases is only small, vessels initially filled
with air can only be evacuated by them to
about 10
-2
mbar. Pressures of 10
-3
mbar
or lower can then be produced with
adsorption pumps only if neither neon nor
helium is present in the gas mixture to be
pumped. In such cases it can be useful to
expel the air in the vessel by first flooding
with nitrogen and then pumping it away.
c) High- and ultrahigh vacuum region
(< 10
-3
mbar)
When there is significant evolution of gas
in the pressure regions that must be pum-
ped, turbomolecular pumps, or cryo-
pumps should be used. A sputter-ion
pump is especially suitable for maintaining
the lowest possible pressure for long
periods in a sealed system where the
process does not release large quantities
of gas. Magnetically-suspended turbomo-
lecular pumps also guarantee hydrocar-
bon-free vacua. However, while these
pumps are switched off, oil vapors can
enter the vessel through the pump. By
suitable means (e.g., using an isolating
valve or venting the vessel with argon),
contamination of the vessel walls can be
impeded when the pump is stationary. If
the emphasis is on generating a “hydroc-
arbon-free vacuum” with turbomolecular
pumps, then hybrid turbomolecular
pumps with diaphragm pumps or classic
turbomolecular pumps combined with
scroll pumps should be used as oil-free
backing pumps.
2.2.6 Ultrahigh vacuum
working Techniques
The boundary between the high and ultra-
high vacuum region cannot be precisely
defined with regard to the working me-
thods. In practice, a border between the
two regions is brought about because
pressures in the high vacuum region may
be obtained by the usual pumps, valves,
seals, and other components, whereas for
pressures in the UHV region, another
technology and differently constructed
components are generally required. The
“border” lies at a few 10
-8
mbar. Therefore,
pressures below 10
-7
mbar should ge-
nerally be associated with the UHV region.
The gas density is very small in the UHV
region and is significantly influenced by
outgasing rate of the vessel walls and by
the tiniest leakages at joints. Moreover, in
connection with a series of important
technical applications to characterize the
UHV region, generally the monolayer time
(see also equation 1.21) has become
important. This is understood as the time t
that elapses before a monomolecular or
monatomic layer forms on an initially
ideally cleaned surface that is exposed to
the gas particles. Assuming that every gas
particle that arrives at the surface finds a
free place and remains there, a convenient
formula for τ is
(p in mbar)
Therefore, in UHV (p < 10
-7
mbar) the
monolayer formation time is of the order
of minutes to hours or longer and thus of
the same length of time as that needed for
experiments and processes in vacuum.
The practical requirements that arise have
become particularly significant in solid-
state physics, such as for the study of thin
films or electron tube technology. A UHV
system is different from the usual high
vacuum system for the following reasons:
a) the leak rate is extremely small (use of
metallic seals),
b) the gas evolution of the inner surfaces
of the vacuum vessel and of the
attached components (e.g., connecting
tubulation; valves, seals) can be made
extremely small,
c) suitable means (cold traps, baffles) are
provided to prevent gases or vapors or
their reaction products that have origi-
nated from the pumps used from
reaching the vacuum vessel (no
backstreaming).
To fulfill these conditions, the individual
components used in UHV apparatus must
be bakeable and extremely leaktight.
Stainless steel is the preferred material for
UHV components.
The construction, start-up, and operation
of an UHV system also demands special
care, cleanliness, and, above all, time. The
assembly must be appropriate; that is, the
individual components must not be in the
least damaged (i.e. by scratches on
precision-worked sealing surfaces). Fun-
damentally, every newly-assembled UHV
apparatus must be tested for leaks with a
helium leak detector before it is operated.
Especially important here is the testing of
demountable joints (flange connections),
glass seals, and welded or brazed joints.
After testing, the UHV apparatus must be
baked out. This is necessary for glass as
well as for metal apparatus. The bake-out
extends not only over the vacuum vessel,
but frequently also to the attached parts,
particularly the vacuum gauges. The
individual stages of the bake-out, which
can last many hours for a larger system,
and the bake-out temperature are arranged
according to the kind of plant and the
ultimate pressure required. If, after the
apparatus has been cooled and the other
necessary measures undertaken (e.g.,
cooling down cold traps or baffles), the
ultimate pressure is apparently not
obtained, a repeated leak test with a
helium leak detector is recommended.
Details on the components, sealing
methods and vacuum gauges are provided
in our catalog.
D00
D00 E 19.06.2001 21:38 Uhr Seite 61