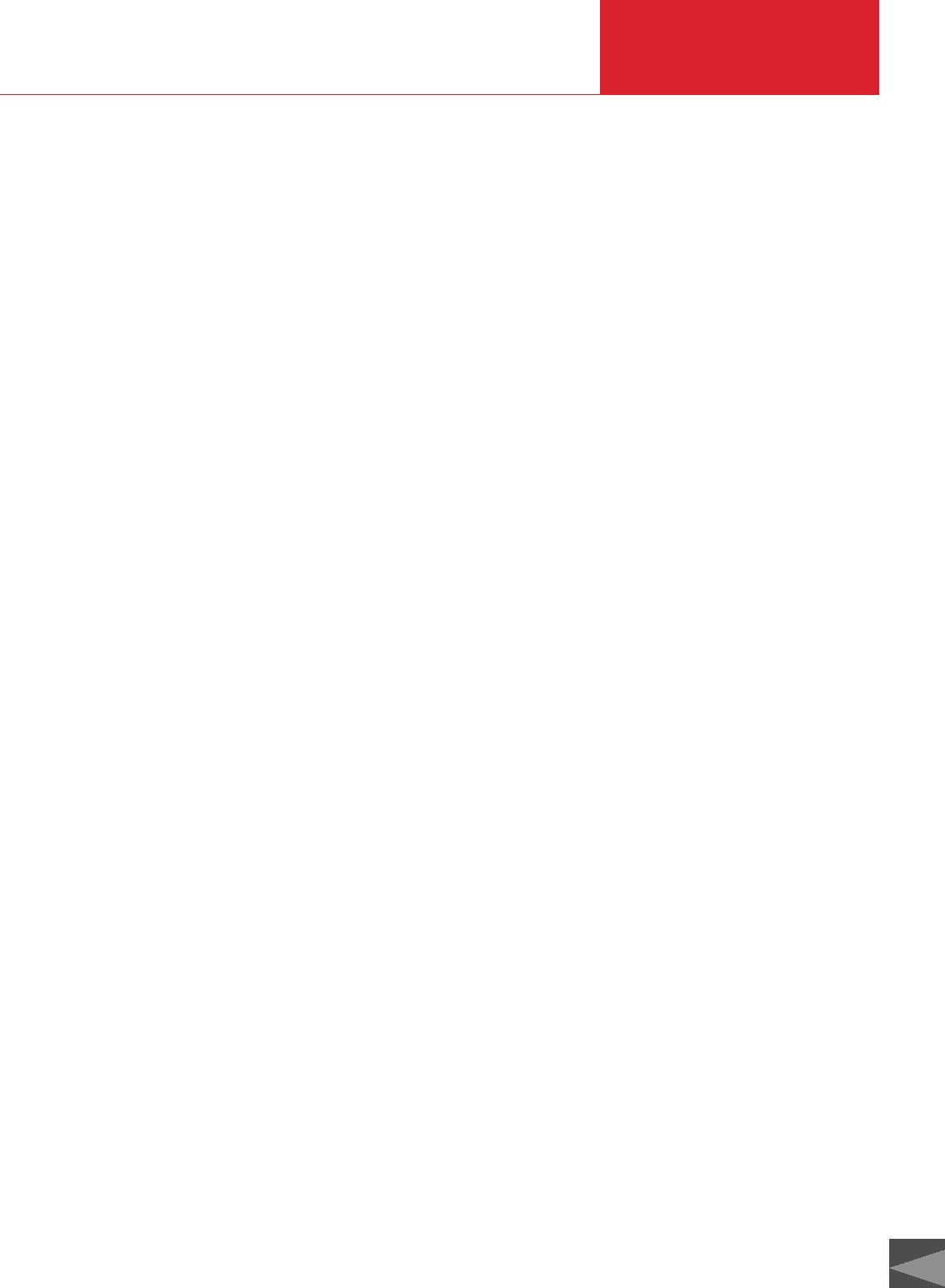
Vacuum Generation
Fundamentals of Vacuum Technology
D00.35
LEYBOLD VACUUM PRODUCTS AND REFERENCE BOOK 2001/2002
of the condenser, the water vapor partial
pressure p
v2
lies more or less above the
saturation pressure p
S
which corresponds
to the temperature of the refrigerant. (By
cooling with water at 12 °C, p
S
, would be
15 mbar (see Table XIII in Section 9)).
Correspondingly, the partial air pressure
p
p2
that prevails at the condenser exit also
varies. With a large condenser,
p
v2
≈ p
S
, the air partial pressure p
p,2
is thus
large, and because p
p
· V = const, the
volume of air involved is small. Therefore,
only a relatively small gas ballast pump is
necessary. However, if the condenser is
small, the opposite case arises:
p
v2
> p
S
· p
p2
, is small. Here a relatively
large gas ballast pump is required. Since
the quantity of air involved during a
pumping process that uses condensers is
not necessarily constant but alternates
within more or less wide limits, the
considerations to be made are more
difficult. Therefore, it is necessary that the
pumping speed of the gas ballast pump
effective at the condenser can be regulated
within certain limits.
In practice, the following measures are
usual:
a) A throttle section is placed between the
gas ballast pump and the condenser,
which can be short-circuited during
rough pumping. The flow resistance of
the throttle section must be adjustable
so that the effective speed of the pump
can be reduced to the required value.
This value can be calculated using the
equations given in Section 2.2.3.
b) Next to the large pump for rough pum-
ping a holding pump with low speed is
installed, which is of a size corres-
ponding to the minimum prevailing gas
quantity. The objective of this holding
pump is merely to maintain optimum
operating pressure during the process.
c) The necessary quantity of air is ad-
mitted into the inlet line of the pump
through a variable-leak valve. This
additional quantity of air acts like an
enlarged gas ballast, increasing the
water vapor tolerance of the pump.
However, this measure usually results
in reduced condenser capacity. More-
over, the additional admitted quantity of
air means additional power consump-
tion and (see Section 8.3.1.1) increased
oil consumption. As the efficiency of the
condenser deteriorates with too great a
partial pressure of air in the condenser,
the admission of air should not be in
front, but generally only behind the
condenser.
If the starting time of a process is shorter
than the total running time, technically the
simplest method – the roughing and the
holding pump – is used. Processes with
strongly varying conditions require an
adjustable throttle section and, if needed,
an adjustable air admittance.
On the inlet side of the gas ballast pump a
water vapor partial pressure p
v2
is always
present, which is at least as large as the
saturation vapor pressure of water at the
coolant temperature. This ideal case is
realizable in practice only with a very large
condenser (see above).
With a view to practice and from the stated
fundamental rules, consider the two
following cases:
1. Pumping of permanent gases with
small amounts of water vapor. Here the
size of the condenser – gas ballast pump
combination is decided on the basis of the
pumped-off permanent gas quantity. The
condenser function is merely to reduce the
water vapor pressure at the inlet port of
the gas ballast pump to a value below the
water vapor tolerance.
2. Pumping of water vapor with small
amounts of permanent gases. Here, to
make the condenser highly effective, as
small as possible a partial pressure of the
permanent gases in the condenser is
sought. Even if the water vapor partial
pressure in the condenser should be
greater than the water vapor tolerance of
the gas ballast pump, a relatively small gas
ballast pump is, in general, sufficient with
the then required throttling to pump away
the prevailing permanent gases.
Important note: During the process, if the
pressure in the condenser drops below the
saturation vapor pressure of the conden-
sate (dependent on the cooling water
temperature), the condenser must be
blocked out or at least the collected
condensate isolated. If this is not done, the
gas ballast pump again will pump out the
vapor previously condensed in the
condenser
2.1.6 Fluid-entrainment pumps
Basically, a distinction is made between
ejector pumps such as water jet pumps
(17 mbar < p < 1013 mbar), vapor ejector
vacuum pumps
(10
-3
mbar < p < 10
-1
mbar) and diffusion
pumps (p < 10
-3
mbar). Ejector vacuum
pumps are used mainly for the production
of medium vacuum. Diffusion pumps
produce high and ultrahigh vacuum. Both
types operate with a fast-moving stream of
pump fluid in vapor or liquid form (water
jet as well as water vapor, oil or mercury
vapor). The pumping mechanism of all
fluid-entrainment pumps is basically the
same. The pumped gas molecules are
removed from the vessel and enter into the
pump fluid stream which expands after
passing through a nozzle. The molecules
of the pump fluid stream transfer by way
of impact impulses to the gas molecules in
the direction of the flow. Thus the gas
which is to be pumped is moved to a space
having a higher pressure.
In fluid-entrainment pumps corresponding
vapor pressures arise during operation
depending on the type of pump fluid and
the temperature as well as the design of
the nozzle. In the case of oil diffusion
pumps this may amount to 1 mbar in the
boiling chamber. The backing pressure in
the pump must be low enough to allow the
vapor to flow out. To ensure this, such
pumps require corresponding backing
pumps, mostly of the mechanical type. The
vapor jet cannot enter the vessel since it
condenses at the cooled outer walls of the
pump after having been ejected through
the nozzle.
Wolfgang Gaede was the first to realize
that gases at comparatively low pressure
can be pumped with the aid of a pump
fluid stream of essentially higher pressure
and that, therefore, the gas molecules
from a region of low total pressure move
into a region of high total pressure. This
apparently paradoxical state of affairs
develops as the vapor stream is initially
entirely free of gas, so that the gases from
a region of higher partial gas pressure (the
vessel) can diffuse into a region of lower
partial gas pressure (the vapor stream).
This basic Gaede concept was used by
Langmuir (1915) in the construction of the
first modern diffusion pump. The first
diffusion pumps were mercury diffusion
pumps made of glass, later of metal. In the
Sixties, mercury as the medium was
D00
D00 E 19.06.2001 21:36 Uhr Seite 35