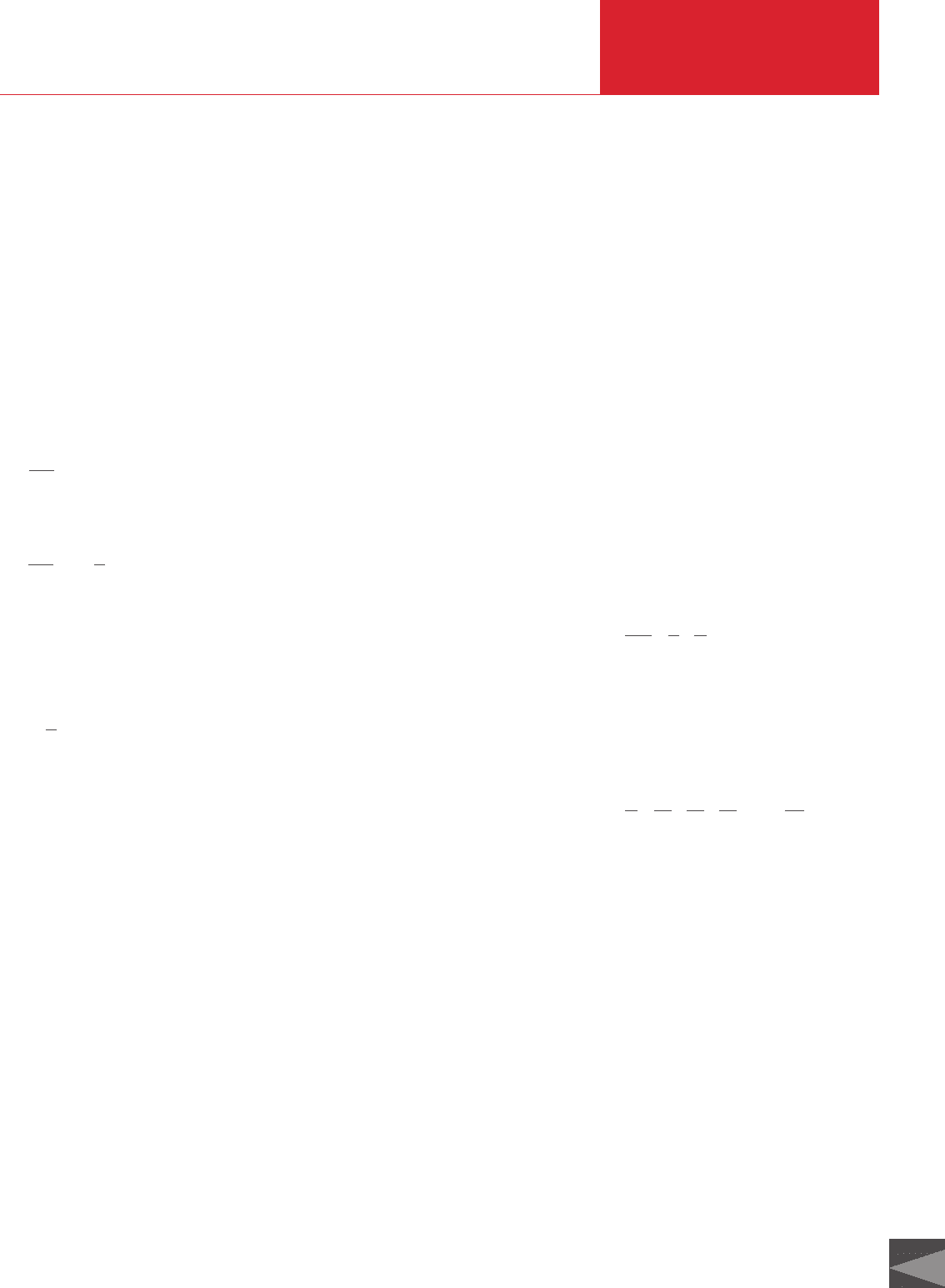
Vacuum Physics
Fundamentals of Vacuum Technology
D00.13
LEYBOLD VACUUM PRODUCTS AND REFERENCE BOOK 2001/2002
Knudsen flow
The transitional range between viscous
flow and molecular flow is known as Knud-
sen flow. It is prevalent in the medium
vacuum range: λ ≈ d.
The product of pressure p and pipe diame-
ter d for a particular gas at a certain tem-
perature can serve as a characterizing
quantity for the various types of flow.
Using the numerical values provided in
Table III, Chapter 9, the following equiva-
lent relationships exist for air at 20 °C:
Rough vacuum – Viscous flow
⇔ p ⋅ d > 6.0 ⋅ 10
-1
mbar ⋅ cm
Medium vacuum – Knudsen flow
⇔
⇔ 6 ⋅ 10
-1
> p ⋅ d > 1.3 ⋅ 10
-2
mbar ⋅ cm
High and ultrahigh vacuum – Molecular
flow
⇔ p ⋅ d < 1.3 ⋅ 10
-2
mbar · cm
In the viscous flow range the preferred
speed direction for all the gas molecules
will be identical to the macroscopic direc-
tion of flow for the gas. This alignment is
compelled by the fact that the gas particles
are densely packed and will collide with
one another far more often than with the
boundary walls of the apparatus. The
macroscopic speed of the gas is a “group
velocity” and is not identical with the “ther-
mal velocity” of the gas molecules.
In the molecular flow range, on the other
hand, impact of the particles with the walls
predominates. As a result of reflection (but
also of desorption following a certain resi-
dence period on the container walls) a gas
particle can move in any arbitrary direction
in a high vacuum; it is no longer possible
to speak of “flow” in the macroscopic
sense.
It would make little sense to attempt to
determine the vacuum pressure ranges as
a function of the geometric operating
situation in each case. The limits for the
individual pressure regimes (see Table IX
in Chapter 9) were selected in such a way
that when working with normal-sized labo-
ratory equipment the collisions of the gas
particles among each other will predomi-
nate in the rough vacuum range whereas
in the high and ultrahigh vacuum ranges
impact of the gas particles on the contai-
ner walls will predominate.
In the high and ultrahigh vacuum ranges
the properties of the vacuum container
wall will be of decisive importance since
below 10
-3
mbar there will be more gas
molecules on the surfaces than in the
chamber itself. If one assumes a mono-
molecular adsorbed layer on the inside
wall of an evacuated sphere with 1 l volu-
me, then the ratio of the number of
adsorbed particles to the number of free
molecules in the space will be as follows:
at 1 mbar 10
-2
at 10
-6
mbar 10
+4
at 10
-11
mbar 10
+9
For this reason the monolayer formation
time t (see Section 1.1) is used to charac-
terize ultrahigh vacuum and to distinguish
this regime from the high vacuum range.
The monolayer formation time τ is only a
fraction of a second in the high vacuum
range while in the ultrahigh vacuum range
it extends over a period of minutes or
hours. Surfaces free of gases can therefo-
re be achieved (and maintained over lon-
ger periods of time) only under ultrahigh
vacuum conditions.
Further physical properties change as
pressure changes. For example, the ther-
mal conductivity and the internal friction of
gases in the medium vacuum range are
highly sensitive to pressure. In the rough
and high vacuum regimes, in contrast,
these two properties are virtually indepen-
dent of pressure.
Thus, not only will the pumps needed to
achieve these pressures in the various
vacuum ranges differ, but also different
vacuum gauges will be required. A clear
arrangement of pumps and measurement
instruments for the individual pressure
ranges is shown in Figures 9.16 and 9.16a
in Chapter 9.
1.5.2 Calculating
conductance values
The effective pumping speed required to
evacuate a vessel or to carry out a process
inside a vacuum system will correspond to
the inlet speed of a particular pump (or the
pump system) only if the pump is joined
directly to the vessel or system. Practically
speaking, this is possible only in rare situa-
tions. It is almost always necessary to
include an intermediate piping system com-
prising valves, separators, cold traps and
the like. All this represents an resistance to
flow, the consequence of which is that the
effective pumping speed S
eff
is always less
than the pumping speed S of the pump or
the pumping system alone. Thus to ensure
a certain effective pumping speed at the
vacuum vessel it is necessary to select a
pump with greater pumping speed. The
correlation between S and S
eff
is indicated
by the following basic equation:
(1.24)
Here C is the total conductance value for
the pipe system, made up of the individual
values for the various components which
are connected in series (valves, baffles,
separators, etc.):
(1.25)
Equation (1.24) tells us that only in the
situation where C = ∞ (meaning that the
flow resistance is equal to 0) will S = S
eff
.
A number of helpful equations is available
to the vacuum technologist for calculating
the conductance value C for piping sec-
tions. The conductance values for valves,
cold traps, separators and vapor barriers
will, as a rule, have to be determined empi-
rically.
It should be noted that in general that the
conductance in a vacuum component is
not a constant value which is independent
of prevailing vacuum levels, but rather
depends strongly on the nature of the flow
(continuum or molecular flow; see below)
and thus on pressure. When using con-
ductance indices in vacuum technology
calculations, therefore, it is always neces-
sary to pay attention to the fact that only
the conductance values applicable to a cer-
tain pressure regime may be applied in
that regime.
1 1 1 1 1
1 2 3
C C C C C
n
= + + + . . .
D00
D00 E 19.06.2001 21:35 Uhr Seite 13