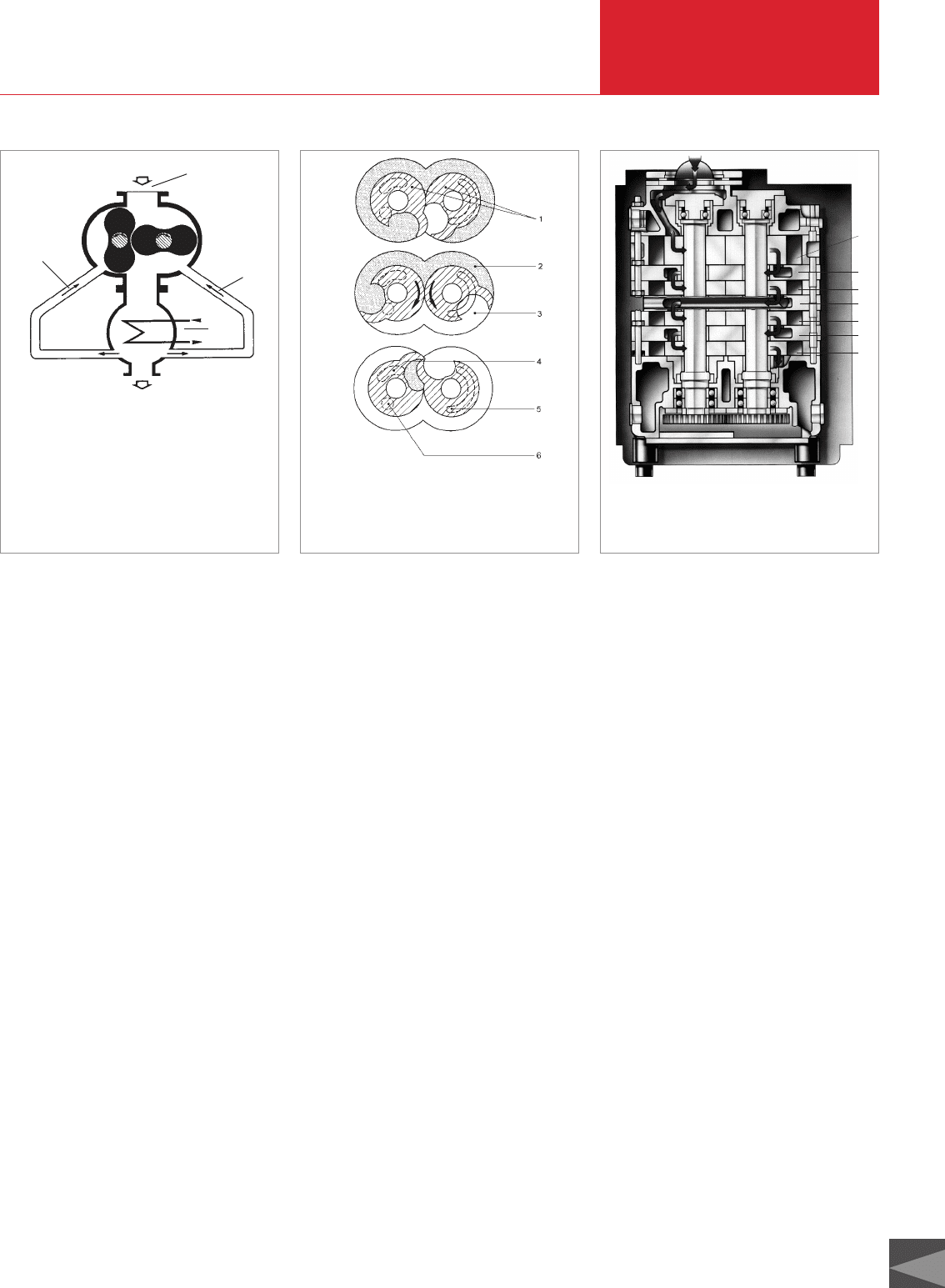
Vacuum Generation
Fundamentals of Vacuum Technology
D00.27
LEYBOLD VACUUM PRODUCTS AND REFERENCE BOOK 2001/2002
pressure difference of the particular pump.
This ensures that the Roots pump is not
overloaded and that it may be operated in
any pressure range. In practice this means
that the Roots pump can be switched on,
together with the backing pump, at
atmospheric pressure. In the process any
pressure increases will not adversely affect
combined operation, i.e. the Roots pump
is not switched off in such circumstances.
Pre-admission cooling (Fig. 2.22)
In the case of Roots pumps with pre-
admission cooling, the compression pro-
cess basically is the same as that of a nor-
mal Roots pump. Since greater pressure
differences are allowed more installed
power is needed, which at the given speed
and the pressure difference between inlet
and discharge port is directly proportional
and is composed of the theoretical work
done on compression and various power
losses. The compression process ends
normally after opening of the pumping
chamber in the direction of the discharge
port. At this moment warmed gas at higher
pressure flows into the pumping chamber
and compresses the transported volume of
gas. This compression process is perfor-
med in advance in the case of pre-admis-
sion cooling. Before the rotor opens the
pumping chamber in the direction of the
discharge port, compressed and cooled
gas flows into the pumping chamber via
the pre-admission channel. Finally the
rotors eject the pumped medium via the
discharge port. The cooled gas, which in
the case of single-stage compression is
taken from the atmosphere and admitted
from the pre-admission cooler, and which
in the case of multi-stage pump systems is
taken from downstream gas coolers,
performs a pre-compression and removes
by “inner cooling” the heat of compression
at the point of time it occurs.
2.1.3.2 Claw pumps
Like Roots pumps, claw pumps belong to
the group of dry compressing rotary
piston vacuum pumps (or rotary vacuum
pumps). These pumps may have several
stages; their rotors have the shape of
claws.
The design principle of a claw pump is
explained by first using an example of a
four-stage design. The cross section inside
the pump’s casing has the shape of two
partly overlapping cylinders (Fig. 2.23).
Within these cylinders there are two freely
rotating rotors in each pump stage: (1)
with their claws and the matching recesses
rotating in opposing directions about their
vertical axes. The rotors are synchronized
by a gear just like a Roots pump. In order
to attain an optimum seal, the clearance
between the rotor at the center of the
casing and the amount of clearance with
respect to the inside casing wall is very
small; both are in the order of magnitude
of a few 0.01 mm. The rotors periodically
open and close the intake and discharge
slots (5) and (4). At the beginning of the
work cycle in position a, the right rotor just
opens the intake slot (5). Gas now flows
into the continually increasing intake space
(3) in position b until the right rotor seals
off the intake slot (5) in position c. After
both claws have passed through the center
position, the gas which has entered is then
compressed in the compression chamber
(2) (position a) so long until the left rotor
releases the discharge slot (4) (position b)
thereby discharging the gas. Immediately
after the compression process has started
(position a) the intake slot (5) is opened
simultaneously and gas again flows into
the forming intake space (3) (position b).
Influx and discharge of the gas is
performed during two half periods. Each
rotor turns twice during a full work cycle.
Located between the pumping stages are
intermediate discs with flow channels
which run from the discharge side of the
upper stage to the intake side of the next
stage, so that all inlet or exhaust sides are
arranged vertically above each other (Fig.
2.24). Whereas in a Roots pump the in-
coming gas is pumped through the pump
at a constant volume and compression is
only performed in the forevacuum line
(see Section 2.1.3.1), the claw pump
compresses the gas already within the
pumping chamber until the rotor releases
the discharge slot. Shown in Fig. 2.25 are
the average pressure conditions in the
individual pumping stages of a DRYVAC at
an intake pressure of 1 mbar. In order to
meet widely differing requirements
LEYBOLD manufactures two different
D00
Fig. 2.22 Diagram of a Roots pump with pre-admis-
sion cooling
1 Intake port
2 Discharge port
3 Gas cooler
4 Flow of cold gas
1
2
3
4
4
Fig. 2.23 Principle of operation
a
b
c
1 Rotors
2 Compression
chamber
3 Intake space
4 Exhaust slot
5 Intake slot
6 Intermediate stage purge
gas
Fig. 2.24 Arrangement of the pumps and guiding of
the gas flow. P = Pump stage Z = Interme-
diate ring
D00 E 19.06.2001 21:36 Uhr Seite 27