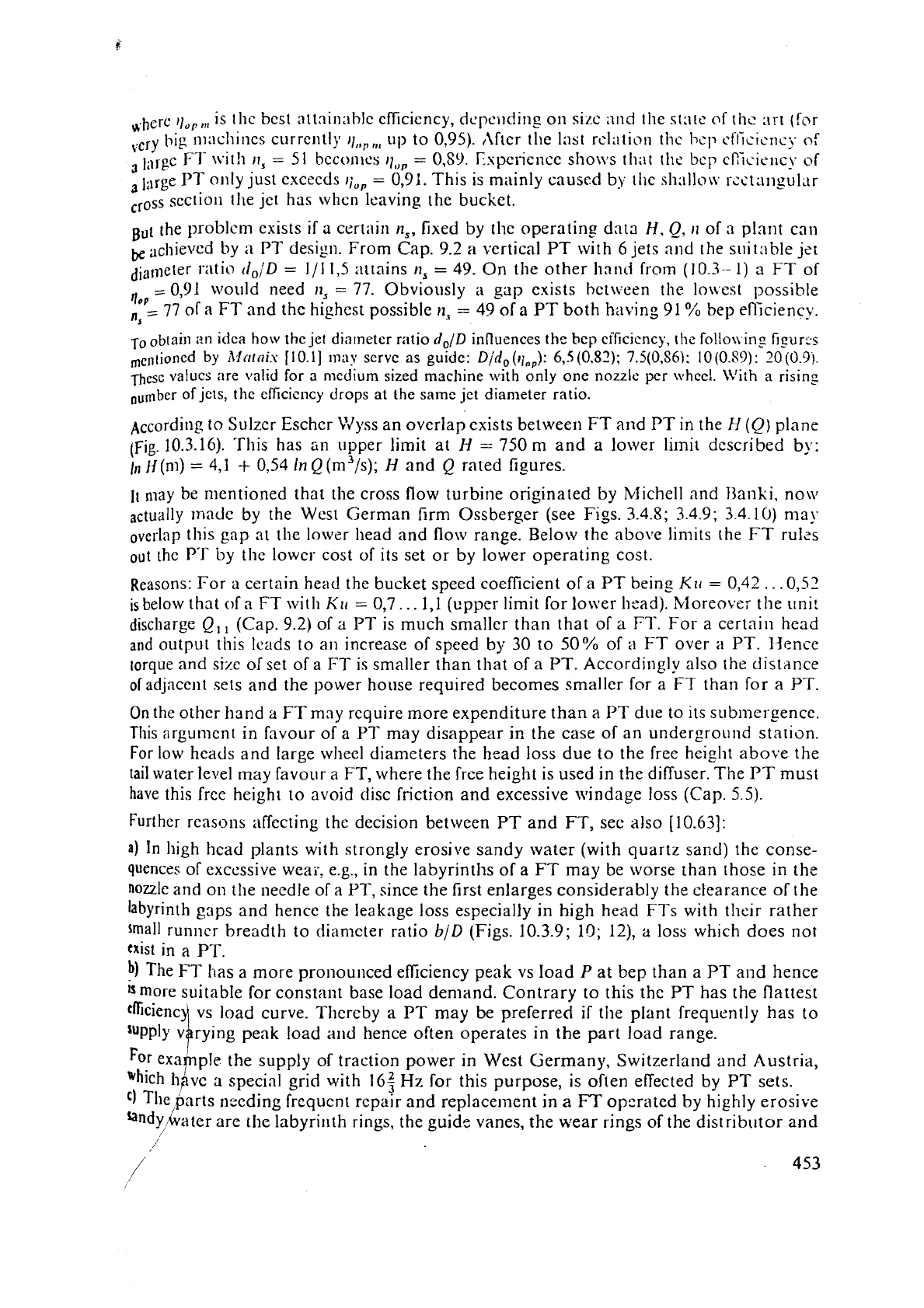
,,.here
rl,,,,,
is thc best attainable eficiency, dcpcnding
011
six
and
the state of thc art (for
,.cry
big
nlacllincs currcntlg
I{,,,,,,,
"11
to 0,95). hftcr tlic Inst rclation llic
I?cp
cfficicnc!.
d
lnrgc
FJ*
\vit!l
11,
=
51
becomes
I!,,,
=
0,s').
hpesiencc sho~i~s that the bcp cBiciency of
a
large I'T ollly just exceeds
I;,,
=
0,9i.
This is mainly caused by ~hc sh:lllow rxtangular
cross section the jet has wllcn leaving the bucket.
gut the problcm exists
if
a
certain
rt,,
fixed by the operating data
H,
Q,
11
of
3
plant can
be
by
a
PT
design. From Cap. 9.2
a
vertical
PT
with
6
jets and the suit:ible
jet
dialneter ratio
do/D
=
111
1,5
atrains
n,
=
49.
On
the other hand from
(10.3.-
1)
a
FT
of
=
0,91
would need
11,
=
77. Obviously
a
gap exists bct~veen the lo\vest possible
~OP
n*
=
77
of a FT and the highest possible
n,
=
49 of a
PT
both having 91
%
be13 efiiciency.
T,
obtain
an
idca how
the
jet diameter ratio
d,/D
influences the
hcp
cificicnc~,
the
fol!o\\
in?
fi_rurzs
by
~~.lnruis
[10.1]
may
scrvc as
guide:
Djd,(rl,,):
6,5(0,82):
7.5(O.S6):
lO(O.89):
20(0.9!.
~hesc
values
:Ire
valid
for
a
nicdium
sized machine
with
only one
nozzle
per nchce!.
\trith
a risins
number
of
jets,
the
efficiency drops at the same jet diameter ratio.
~ccordillg to Sulzer Escher VJyss an overlap exists between
FT
and
PT
in the
H
(Q)
plane
(Fig.
10.3.16).
'This has
sn
upper limit at
H
=
750 m and
a
lower limit described by:
In
11
(nl)
=
4,l
+
0,54
In
Q
(rn3/s);
H
and
Q
rated figures.
11
may be mentioned that the cross flow turbine originated by Michell and Tjanki, nou1
actually ]made by the West German firm Ossberger (see Figs. 3.4.5; 3.4.9; 3.4.10) may
overlap this gap
at
the lower head and flow range. Below the above limits the
FT
rules
out the P7'
by
the lowcr cost
of
its set or by lower operating cost.
Reasons: For
a
certain head the bucket speed coefficient of a PT being
Klr
=
0,42..
.0,52
is
below that
of
a
FT
wit11
Klr
=
0,7..
.
1,l (upper limit for loiver head). bloreove: the unit
discharge
Q,,
(Cap. 9.2) of
a
PT is much smaller than that of
a
FT.
For a certain head
and
output this leads to
an
increase of speed by 30 to 50% of
a
FT
over
:I
PT. Hence
torque and size of set of a FT is smaller than that of
a
PT.
Accordiilgly also the distance
of adjacel~t sets and the power house required becomes smaller for a
FT
than for
a
PT.
On
the other hand
a
FT
may require more expenditure than a
PT
due to its submergence.
This argument in favour of a PT may disappear in the case of an underground station.
For low heads and large wheel diameters the head loss due to the free height above the
tail water level may favour
a
FT,
where the free height
is
used in the diffuser. The
PT
must
have this free height to avoid disc friction and excessive windage loss (Cap.
5.5).
Further reasons affecting the decision between
PT
and
FT,
see also [10.63]:
a)
In
high head plants with strongly erosive sandy water (with quartz sand) the conse-
quences of excessive
wear,
e.g.,
in the labyrinths of a
FT
may
be worse than those in the
nozzle and
oil the needle of a
PT,
since the first enlarges considerably the clearance
of
the
labyrinth gaps and hence the leakage loss especially in high head
FTs with their rather
small ruilner breadth to tiianicter ratio
b/D
(Figs. 10.3.9;
10;
12),
a loss which does not
exist in
a
PT.
6)
The
FT
has a more pronounced efficiency peak vs load
P
at bep than a
PT
and hence
&more suitable for constant base load demand. Contrary to this the
PT
has the flattest
tficienc) vs load curve. Thereby
a
PT
may be preferred if tile plant frequently has to
Su~ply v rying peak load and hence often operates in the part load range.
b
For
exahple the supply of traction power in West Germany, Switzerland and Austria,
which h~vc a special grid with
163
Hz
for this purpose, is often effected by
PT
sets.
The
harts
needing
frequent repair and replacelnent in
a
FT
opcrated by highly erosive
"nd$ater are
[he
labyrillth rings, the guidz vanes, the wear rings of the distributor and