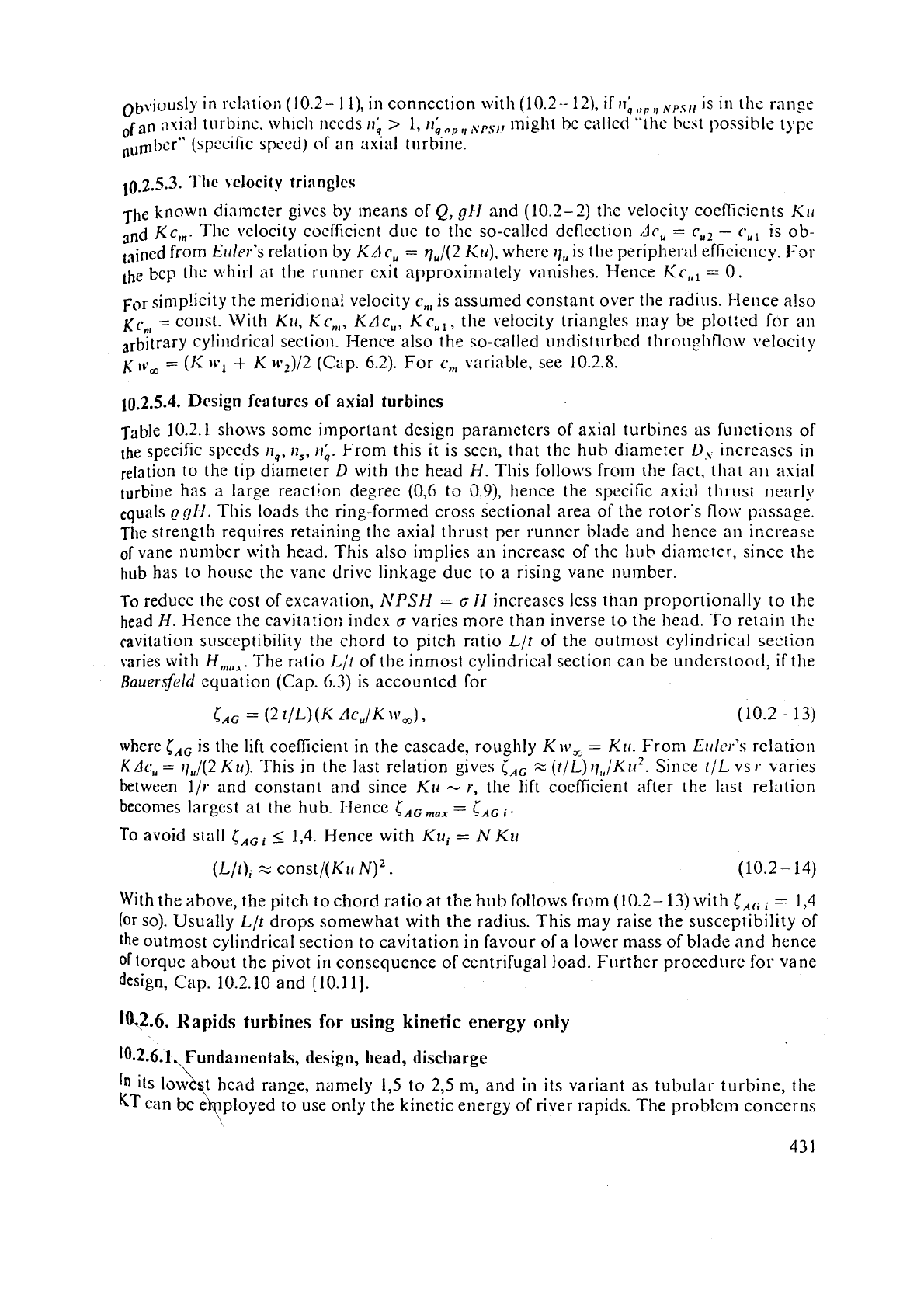
.
.
Obvio~Sly in rclittion (10.2-
I
l),
in connection n-it11 (10.2-
121,
if
n~,lp,,.,s,,
IS
In
111,:
riln$e
;lxinl turbine. which ilccds
r(,
>
l~z~,,,,~,,,,, might be callcd
"the
he51
possible tgpc
nu&cr" (specific speed) of
an
axial turbirie.
The known diameter gives by lneans of
Q,
gH
and (10.2-2) thc velocity coeficients Klr
and
Kc,,.
The velocity coefticicnt due to thc so-called deflection
dc,
=
cU2
-
c,,
is ob-
t3ined from E~lev's relation by
KA
c,
=
q,/(2
Ku),
where I!,, is the peripheral efficiency. For
the bcp the whirl at the runner exit approxirnately vanishes. Hence
Kc,,,
=
0.
for sin~p!icity the meridional velocity
c,,
is assumed constant over the radius. Hence a!so
KC",
=
COIIS~.
With
KII,
KC,,,,
KAc,,,
Kc,,
,
the velocity triangles may be p1ot:ed for
an
cylindrical section. I-Ience also the so-called undisturbed throu~hflo\v velocity
K
=
(1;
lvl
+
K
1v2)/2
(Cap. 6.2). For
c,,,
variable, see 10.2.8.
10.2.5.4.
Design
features
of
axial
turbines
Table 10.2.1 shows some i~nporlant design parameters of axial turbines as filnctions of
the specific spccds
I],,
II,,
11;.
From this it is seen, that the hub diameter
D,
increases in
relation to the tip diameter
L)
with the head
H.
This follows from the fact, that all axial
turbine has a large reaction degree (0,6 to
O.9),
hence the specific axial thl.ust nearly
equals
@OH.
This loads the ring-formed cross sectional area of the rotor's
flow
passage.
The strength requires retaining
the axial thrust per runncr blade and hence an increase
of
vane number with head. This also implies an increase of thc
hub
diamcter, since the
hub has to house the vane drive linkage due to a rising vane number.
To reduce the cost of excavation,
NPSH
=
G
H
increases less than proportionally
to
the
head
H.
Hence the cavitntiori index
a
varies more than inverse to the head. To retain the
cavitation susceptibility the chord to pitch ratio
Llt of the outmost cylindrical section
varies with
H,,,,,.
The ratio
I,/t
of the inmost cylindrical section can be unders~oncl, if the
Bauersjkld
equation (Cap.
6.3)
is accounted for
where
c,,
is the lift coefficient in the cascade, roughly
K
~r?,
=
Ku.
From
Errlcr's
relation
K
Ac,
=
11,,/(2
Ku).
This in
the
last relation gives
iAG
%
(t/L)
rl,,/~~r2.
Since tlL vs
r-
varies
between
1/r and constant and since
Ktr
-
I., the lift coefficient after the last relation
-
becomes largest at the hub. I-Ience
CAG
,,,,
-
I,,
,.
To avoid stall
CAGi
I
1,4. Hence with
Ku,
=
N
Ku
With the above, the pitch to chord ratio at the hub follows from
(10.2-
13)
with
lAG
=
1,4
(or
so). Usually Llt drops somewhat with the radius. This may raise the susceptibility of
the outmost cylindrical section to cavitation in favour of a lower mass of blade and hence
of
torque about the pivot
iri
consequence of centrifugal load. Ftirther procedure for vane
design, Cap.
10.2.10 and [10.11].
ra2.6.
Rapids
turbines
for
using
kinetic energy
only
10.2.6.1,~undamcntals,
design,
head,
discharge
\
In
its 1owef;t head range, namely
1,5
to
2,5
rn,
and in its variant as tubular turbine, the
KT
can be ekpployed to use only the kinetic energy of river rapids. The problc~n concerns
\