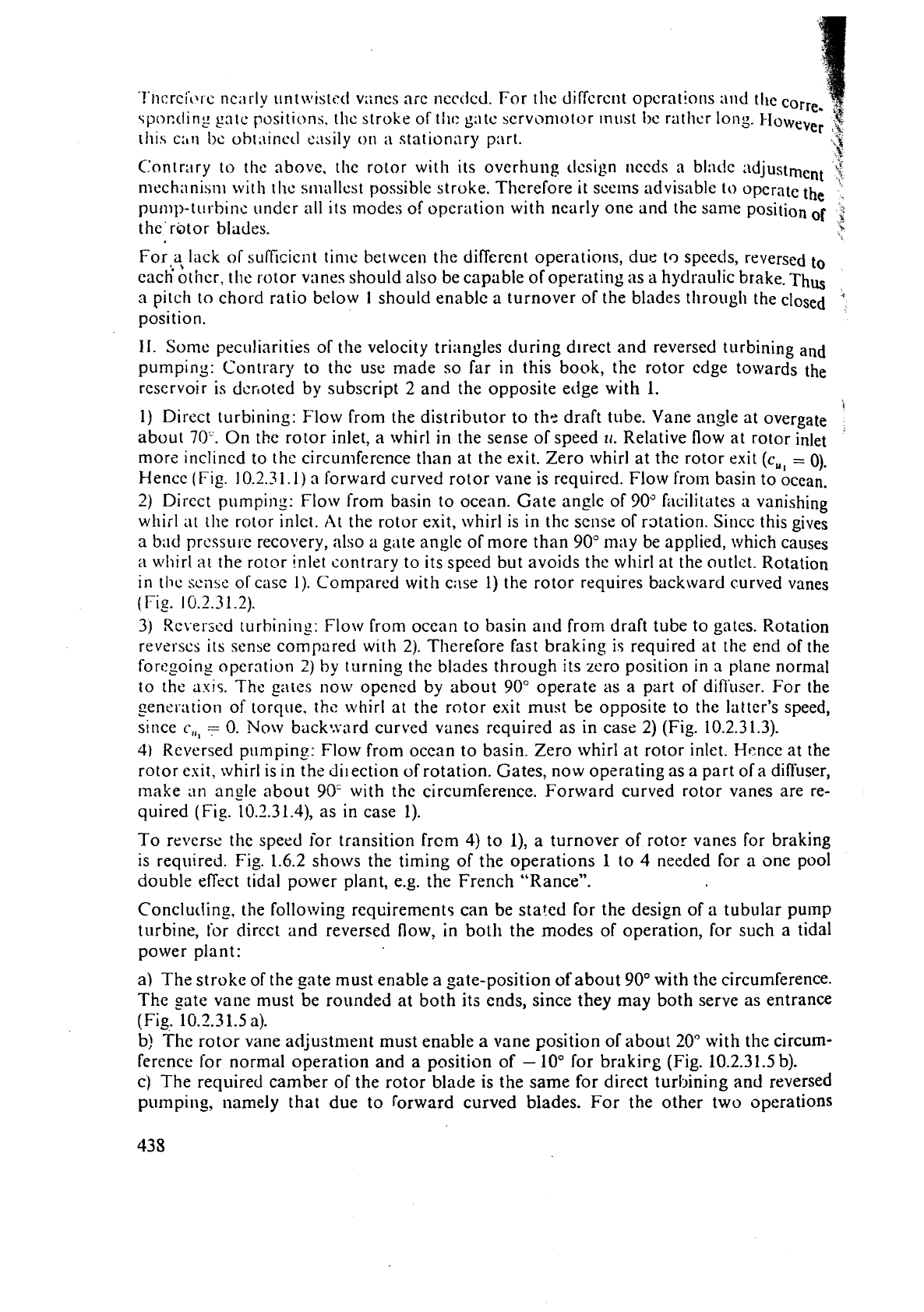
.T'tic:rci;~rc nearly untwistt-cl v;;ncs arc nectlcd. For tlie diffcrc~it operations :lnd
tile
,-orre.
spol:ding g:rtc positions. tl~c stroke of t:ic g;rtc
servomotor
~niist
IIC
ratlicr loiig. I-lowever
*,
this c:ln I)c oh[,linccl e,lsily on
a
stationary part.
3
*
r*
C:ontr:iry to the above. the rotor with its overhung design nceds
a
b1:ldc ildjustment
di
mech;lni\ni with tlic s~iiollest possible stroke. Thcrefore
it
scelns ;ldvis;lble to operate the
pump-turbinc under all its modes of operation with ncarly one and the same position
of
3
the rotor blades.
For a lack of sufficient
tinic between the different operations, due t9 speeds, reversed
to
each' btiier, the rotor vanes should also be capable of operating as
a
hydraulic brake. rhus
a
pitch to chord ratio below
1
should enable a turnover of the blades through the closed
'
position.
11.
Some peculiarities of tlie velocity triangles during dlrect and reversed turbining and
pumping: Contrary to thc use made so far in this book, the rotor edge towards the
reservoir is dcr,oted by subscript 2 and the opposite edge with
1.
I
1)
Direct turbining: Flow from the distributor to thc: draft tube. Vane arlgle at overgate
about
70-.
On the rotor inlet,
a
whirl in the sense of speed
ti.
Relative flow at rotor inlet
more inclined to the circunlfcrence than at the exit. Zero whirl at the rotor exit
(c,,
=
0).
Hence (Fig. 10.2.3
1.1)
n
forward curved rotor vane is required. Flow from basin to ocean.
2) Direct pumping: Flow from basin to ocean. Gate angle of 90" frrcilitates
a
vanishing
whirl at the rotor inlet. At the rotor exit, whirl is in
the setlse of ratation. Sirice this gives
a bad prcssille recovery, :dso
a
gate angle of more than
90"
may be applied, which causes
a whirl
at
the rotor Inlet contrary to its speed but avoids the whirl at the outlet. Rotation
in
tlic scilst. of casc
1).
Compared with c;ise 1) the rotor requires backward curved vanes
(Fis.
10.2.31.2).
3)
licver;t.d turhining: Flow from ocean to basin and from draft tube to gates. Rotation
reverses its sense compared with 2). Therefore fast
brakin2 is required at the end of the
foregoing operation
2)
by
turning the blades through its zero position in a plane normal
to the
axis.
The
gates
now opened by about 90" operate as a part of diffuser. For the
generation of torque, thc whirl at the rotor exit must be opposite to the latter's speed,
since
c,,,
=
0.
Now
back:vard curved vanes required as in case
2)
(Fig. 10.2.31.3).
4)
Reversed pumping: Flow from ocean to basin. Zero whirl at rotor inlet. Hcnce at the
rotor
exit, whirl is in the di~ection of rotation. Gates, now operating as a part ofa diffuser,
make
an
angle about 90' with the circumference. Forward curved rotor vanes are re-
quired
(Fiz. 10.2.31.4), as in case 1).
To reverse the
speed for transition frcm
4)
to l),
a
turnover of rotor vanes for braking
is required.
Fig.
1.6.2 shows the timing of the operations 1 to
4
needed for a one pool
double effect tidal power plant,
e.g. the French "Rance".
Conclutling, the following requirements can be stated for the design of a tubular pump
turbine, for direct and reversed flow, in both the modes of operation, for such a tidal
power plant:
a) The stroke of the gate must enable a gate-position of about
90"
with the circumference.
The
sate vane must be rounded at both its ends, since they may both serve as entrance
(,Fig. 10.2.3 1.5 a).
b) The rotor vane ad;ustn~ent must enable
a
vane position of about 20" with the circum-
ference for normal operation and a position of
-
10"
for brakirg (Fig. 10.2.31.5
b).
C)
The required camber of the roior blade is the same for direct turhining and reversed
pumping,
namely that due to forward curved blades. For the other two operations