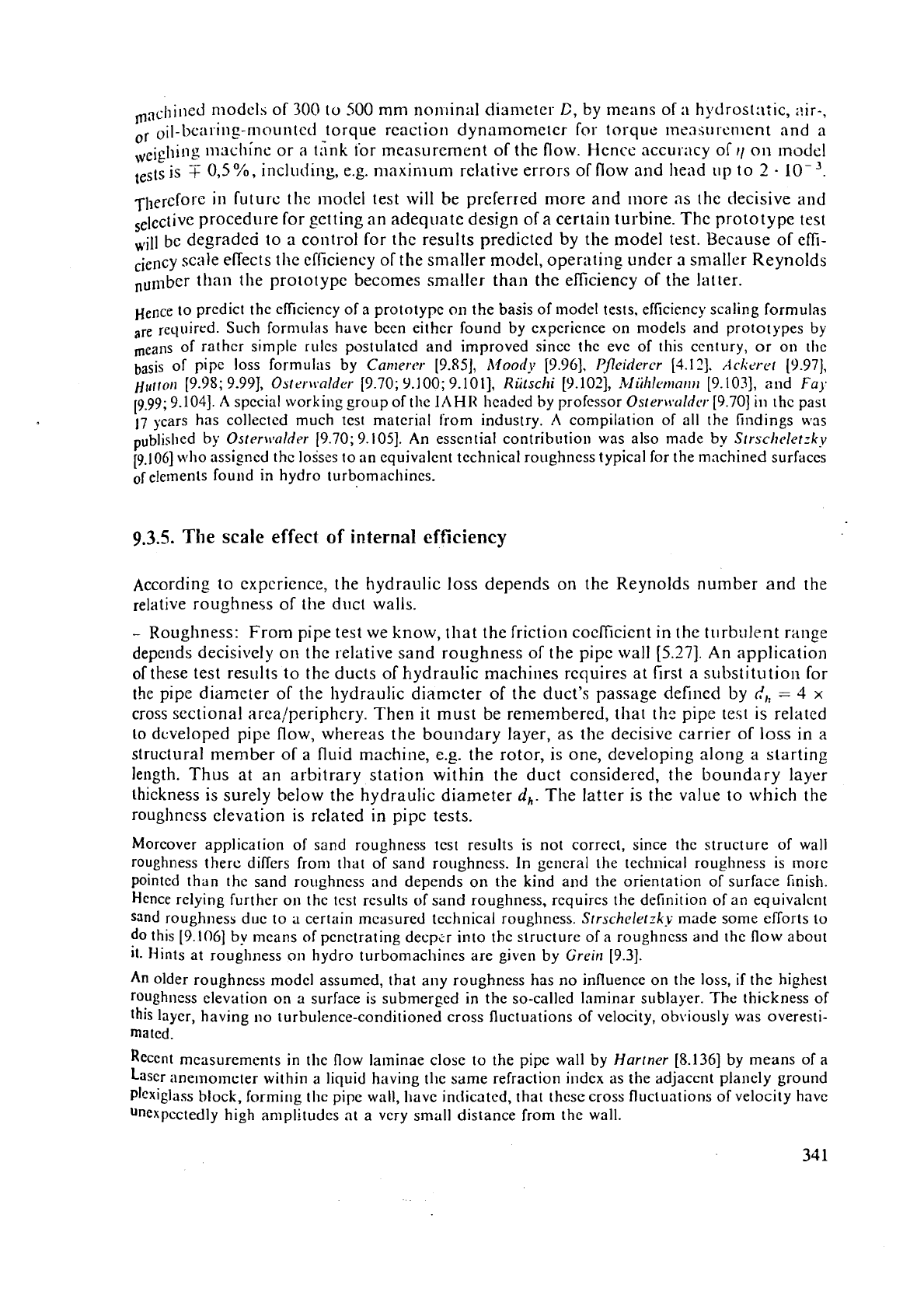
In3
&ined niodelh of
300
to 500 mni nonlinal diameter
C,
by means of
a
hydrost:t;ic, ilir-.
or
oil-bca~~ing-r~~o~~~ltcri
torque reaction dynamometer for torque IneasuI.cnlent and a
,veigl~i~~g lnachine or a tink for measurement of the flow. Hcnce accurilcy of
rl
on
lnodel
is
T
0,5
%,
including, e.g. maximum relative errors
of
flow and head up to
2
.
10
3.
TherCfOrc in future the model test will be preferred more and Inore as the decisive and
selccti~e procedure for setting an adequate design of
a
certain turbine. The prototype test
Hr;l~
be degraded to a control for the results predicted by the model test. Because
of
effi-
ciency scale effects the efficiency of the
smaller model, opernting under a snialler Reynolds
than the prototype becomes smaller than the efficiency of the latter.
Hence to predict the efficiency of a prototype
on
the basis of
nod el
tests, efficiency scaling formulas
are
recluired. Such formillas have been eithcr found by experience on models and prototypes
by
means of rather simplc rules postulated and improved since the eve of this century, or on
the
basis of pipe loss formu1:is by
Can~er-or
[9.85],
Moorly
[9.96],
PJcidercr
[3.11-1.
~~Iirr-c~t
19.971,
~lrtrorl
[9.98; 9.991,
Ostrr\~alder
[9.70;
9.100;
9.1011,
Riitschi
[9.102],
.bJiihlrr~~nitr,
[9.103], and
Fa).
i9.99; 9.1041.
A
special working group of the
1AHII
headed by professor
Oster\t'~lldcr.
[9.70] in thc past
17
years has collected much test material from industry.
A
compilation of all the findings wss
by
Osr~r\tlnlder
[9.70; 9.1051. An essential contribt!tion was also made by
Srrschclerzkv
[g.106] \lfllo rlssipcd thc losses to an equivalellt technical roughness typical for the machined surraccs
of
elements found in hydro turbomachines.
9.3.5.
The scale effect of internal efficiency
According to experience, the hydraulic loss depends on the Reynolds number and the
relative roughness of the duct walls.
-
Roughness: From pipe test we know, that the friction cocficient in the turbulent range
depends decisively on the relative sand roughness of the pipe wall
[5.27].
An application
of these test results to the ducts of hydraulic machines requires at first
a
substitution for
the
pipe diameter of the hydraulic diamcter of the duct's passage defined by
dl,
=
3
x
cross sectional arealperiphcry. Then it must be remembered, that thc pipe test
is
related
to developed pipe flow, whereas the
boundary layer, as the decisive carrier of loss in a
structural member of a fluid machine,
e.g.
the rotor, is one, developing along a starting
length. Thus at an arbitrary station within the duct considered, the boundary layer
thickness is surely below the hydraulic diameter
d,.
The latter is the value to which the
roughness elevation is related in pipc tests.
Morcover application of sand roughness test results is not correct, since the structure of wall
roughness there differs from that of sand
roilghness. In gcneral the
technical
roughness is morc
pointcd than the sand roilghncss and depends on the kind and the orientation of surface finish.
Hence relying further on
thc test results of sand roughness, requires the definition of an equivalent
sand roughness due to
a
certain measured technical roughness.
Srrscheletzky
made some eflorts to
do this
[9.106]
by means of penetrating decpcr into thc structure of a roughness and the
flow
about
it. Hints at roughness on hydro turbomacl~ines are given by
Grein
19.31.
An
older roughness modcl assumed, that any roughness has no influence on the loss,
if
the highest
roughness
elevation on a surface is submerged in the so-called laminar sublayer. The thickness of
this layer, having no turbulence-conditioned cross fluctuations of velocity, ob~iously was overesti-
mated.
Recent measurements in
thc flow laminae closc to the
pipc
wall by
Hartner
[8.136] by means of a
Laser
iinernolncter within a liquid having the same refraction index as the adjaccnt planely ground
~lcxiglass block, formirlg thc pipe wall, have indicatcd, that thcsc cross fluctuations of velocity have
unexpectedly
high
amplitudes
at a very small distance from thc wall.