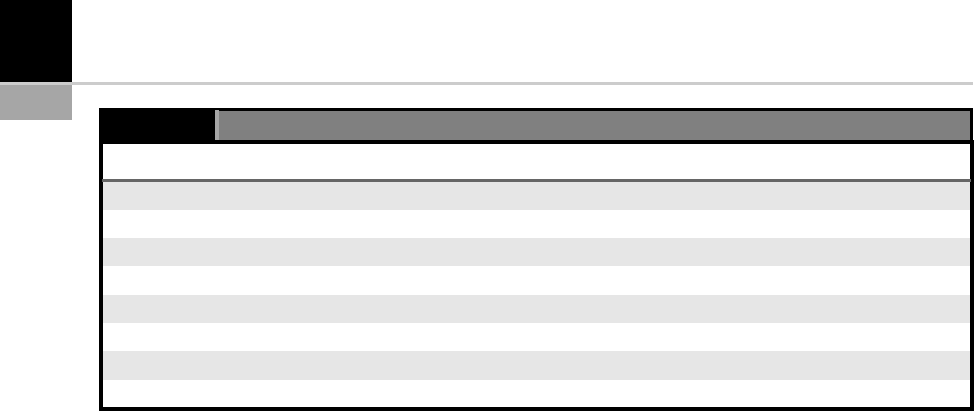
approaches incl ude rotary-turret archi tectu res
and linear pick-and-place architectures based
on carriers.
Rotary-dial indexers are well established in
the industry for their efficiency, flexibility and
ability to deliver high speed performance.
These systems generally use central, high accu-
racy, direct-drive indexing to synchronize a
number of operations nested around the cir-
cumference of the dial. Rotary-turret system
designs offer a simple, rugged-core mechanism
that can be used for integrating a variety of
assembling, inspection and other processing
operations on individual stations around the
periphery of the rotary-indexer platform. Some
of the primary advantages of rotary-indexed
architectures are simplicity, precision, rel iabil-
ity, durability, and high throughput within a
relatively small footprint.
Although rotary-turret architectures generally
provide the most efficient approach for the high
speed integration of most applications, linear
pick-and-place architectures can also be the best
choice for certain applications. For example, sys-
tems that process parts from carrier-to-carrier or
carrier-to-tape often can benefit from using a lin-
ear pick-and-place strategy instead of rotary-tur-
ret architecture. The use of carriers throughout
the stations makes it most efficient and appropri-
ate to feed the machines directly from carriers (see
Fig. 18-2). By combining advanced carrier-scan
techniques with multi-head pick-and-place sys-
tems, linear architecture can deliver a balanced
combination of flexibility and speed that fits
smoothly into carrier-oriented production-floor
operations.
Standard Carriers
A key problem area limiting the emergence of auto-
mated micro-handling technology is the lack of
standardization, which causes equipment makers
to spend an excessive amount of time and resources
on custom-automation solutions [2].
A carrier or tray is a flat magazine that can take
up pieces for storage, transport and handling in an
orderly manner and is adaptable to automatic
piece-feeding to the production equipment.
A cassette or cartridge is a container for car-
riers, which can be plugged into production
equipment for the purpose of automatic feeding.
There are some standards defined for micro-
handling issues. However, many standardized
systems are available in the semiconductor indus-
try, where some examples are:
1. Trays: standardized plastic carriers (2 or 4
inches) (50.8 or 101.6 millimeters) with
depressions for the individual placement of
components. The parts move freely within
the limits of these depressions. Manufacturers
offer standard-sized depressions in a range of
variations. To protect the components, the
trays are closed with a lid with accompanying
retaining clips.
2. Gel packs: components are held by adhesion
to glass or plastic carrying materials with gel
TABLE 18-1
Sequence of Actions in a Pick-and-Place Task
Sub-task Action Velocity Trajectory
Picking 0. Move to #A 100% Joint space
1. Approach to #P 30% Cartesian space
2. Grasp 0% Cartesian space
3. Depart to #A 70% Cartesian space
Hold and transport 4. Transport to #B 100% Joint space
Placing 5. Approach to #R 30% Cartesian space
6. Release 0% Cartesian space
7. Depart to #B 70% Cartesian space
300
CHAPTER 18 Handling for Micro-Manufacturing