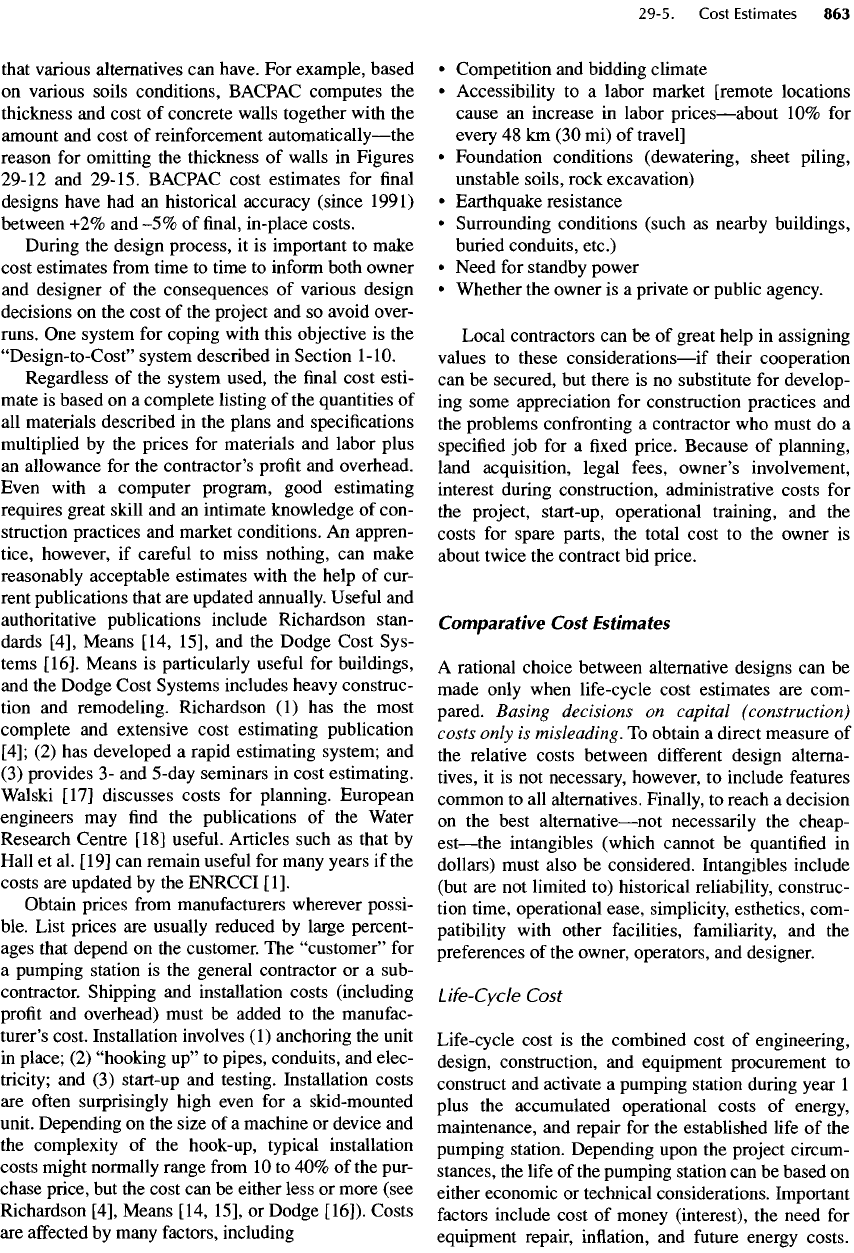
that
various alternatives
can
have.
For
example, based
on
various soils conditions, BACPAC computes
the
thickness
and
cost
of
concrete
walls together with
the
amount
and
cost
of
reinforcement
automatically
—
the
reason
for
omitting
the
thickness
of
walls
in
Figures
29-12
and
29-15.
BACPAC
cost
estimates
for final
designs have
had an
historical accuracy (since 1991)
between
+2% and -5% of final,
in-place
costs.
During
the
design process,
it is
important
to
make
cost estimates
from
time
to
time
to
inform
both owner
and
designer
of the
consequences
of
various design
decisions
on the
cost
of the
project
and so
avoid over-
runs.
One
system
for
coping with this objective
is the
"Design-to-Cost"
system described
in
Section
1-10.
Regardless
of the
system used,
the final
cost esti-
mate
is
based
on a
complete listing
of the
quantities
of
all
materials described
in the
plans
and
specifications
multiplied
by the
prices
for
materials
and
labor plus
an
allowance
for the
contractor's
profit
and
overhead.
Even with
a
computer program, good estimating
requires great skill
and an
intimate knowledge
of
con-
struction
practices
and
market conditions.
An
appren-
tice, however,
if
careful
to
miss nothing,
can
make
reasonably acceptable estimates with
the
help
of
cur-
rent
publications
that
are
updated annually.
Useful
and
authoritative publications include Richardson stan-
dards [4], Means [14, 15],
and the
Dodge Cost Sys-
tems
[16].
Means
is
particularly
useful
for
buildings,
and
the
Dodge Cost Systems includes
heavy
construc-
tion
and
remodeling. Richardson
(1) has the
most
complete
and
extensive cost estimating publication
[4];
(2) has
developed
a
rapid estimating system;
and
(3)
provides
3- and
5-day seminars
in
cost estimating.
Walski
[17] discusses costs
for
planning. European
engineers
may find the
publications
of the
Water
Research Centre [18]
useful.
Articles such
as
that
by
Hall
et
al.
[19]
can
remain
useful
for
many
years
if the
costs
are
updated
by the
ENRCCI
[I].
Obtain prices
from
manufacturers wherever possi-
ble. List prices
are
usually
reduced
by
large percent-
ages
that
depend
on the
customer.
The
"customer"
for
a
pumping station
is the
general contractor
or a
sub-
contractor. Shipping
and
installation costs (including
profit
and
overhead)
must
be
added
to the
manufac-
turer's cost. Installation involves
(1)
anchoring
the
unit
in
place;
(2)
"hooking
up" to
pipes, conduits,
and
elec-
tricity;
and (3)
start-up
and
testing. Installation costs
are
often
surprisingly high even
for a
skid-mounted
unit.
Depending
on the
size
of a
machine
or
device
and
the
complexity
of the
hook-up, typical installation
costs might normally range
from
10 to 40% of the
pur-
chase
price,
but the
cost
can be
either less
or
more (see
Richardson [4], Means [14, 15],
or
Dodge
[16]).
Costs
are
affected
by
many factors, including
•
Competition
and
bidding climate
•
Accessibility
to a
labor market [remote
locations
cause
an
increase
in
labor
prices
—
about
10% for
every
48 km (30 mi) of
travel]
•
Foundation conditions
(dewatering,
sheet piling,
unstable
soils,
rock excavation)
•
Earthquake resistance
•
Surrounding conditions (such
as
nearby buildings,
buried conduits, etc.)
•
Need
for
standby power
•
Whether
the
owner
is a
private
or
public agency.
Local contractors
can be of
great help
in
assigning
values
to
these
considerations
—
if
their cooperation
can
be
secured,
but
there
is no
substitute
for
develop-
ing
some appreciation
for
construction practices
and
the
problems confronting
a
contractor
who
must
do a
specified
job for a fixed
price.
Because
of
planning,
land
acquisition, legal
fees,
owner's involvement,
interest during construction, administrative costs
for
the
project, start-up, operational training,
and the
costs
for
spare parts,
the
total cost
to the
owner
is
about twice
the
contract
bid
price.
Comparative
Cost
Estimates
A
rational choice between alternative designs
can be
made only when life-cycle cost estimates
are
com-
pared. Basing decisions
on
capital
(construction)
costs
only
is
misleading.
To
obtain
a
direct measure
of
the
relative costs between
different
design alterna-
tives,
it is not
necessary, however,
to
include features
common
to all
alternatives.
Finally,
to
reach
a
decision
on
the
best
alternative
—
not
necessarily
the
cheap-
est
—
the
intangibles (which cannot
be
quantified
in
dollars) must also
be
considered. Intangibles include
(but
are not
limited
to)
historical reliability, construc-
tion time, operational
ease,
simplicity, esthetics, com-
patibility with other facilities,
familiarity,
and the
preferences
of the
owner, operators,
and
designer.
Life-Cycle
Cost
Life-cycle
cost
is the
combined cost
of
engineering,
design, construction,
and
equipment procurement
to
construct
and
activate
a
pumping station during year
1
plus
the
accumulated operational costs
of
energy,
maintenance,
and
repair
for the
established
life
of the
pumping
station. Depending upon
the
project circum-
stances,
the
life
of the
pumping station
can be
based
on
either economic
or
technical considerations. Important
factors
include cost
of
money (interest),
the
need
for
equipment repair,
inflation,
and
future
energy costs.