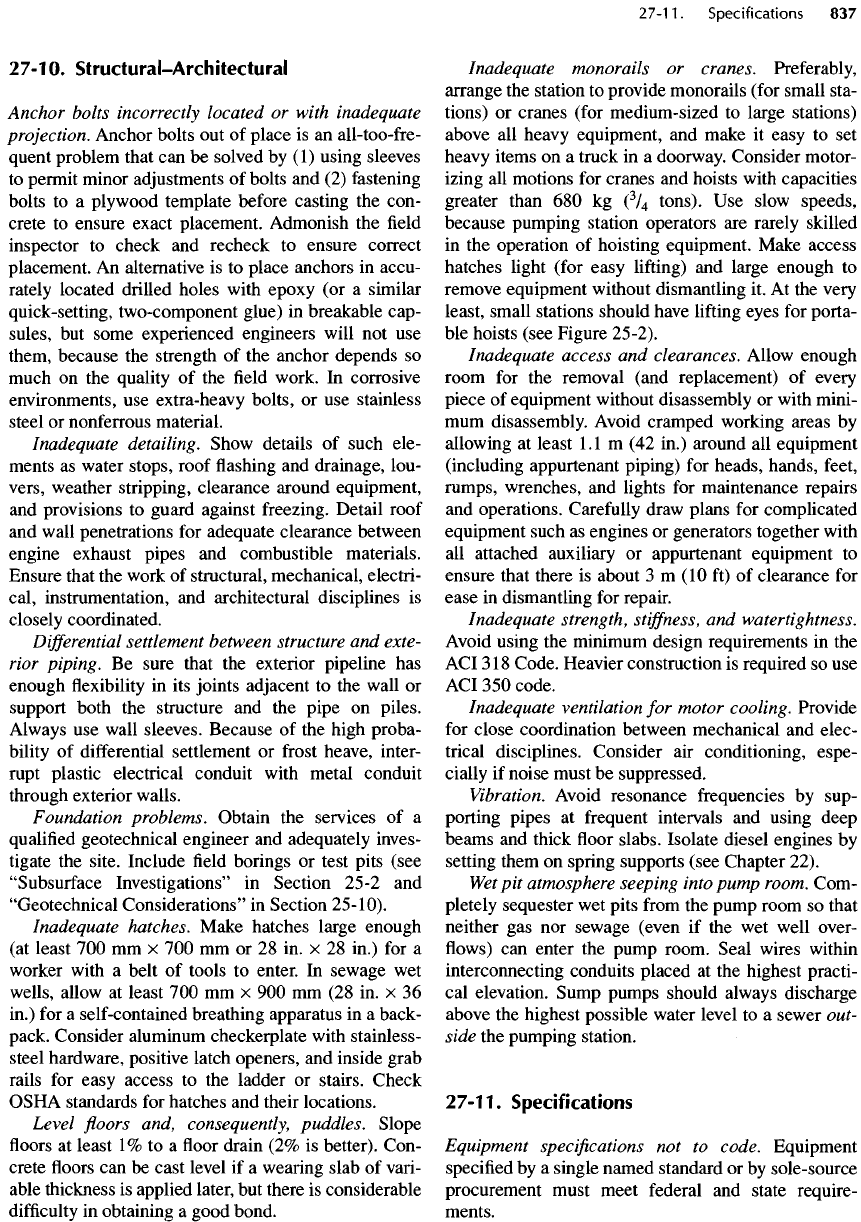
27-10.
Structural-Architectural
Anchor bolts
incorrectly
located
or
with inadequate
projection.
Anchor bolts
out of
place
is an
all-too-fre-
quent
problem that
can be
solved
by (1)
using sleeves
to
permit minor adjustments
of
bolts
and (2)
fastening
bolts
to a
plywood template before casting
the
con-
crete
to
ensure exact placement. Admonish
the field
inspector
to
check
and
recheck
to
ensure correct
placement.
An
alternative
is to
place anchors
in
accu-
rately located
drilled
holes
with epoxy
(or a
similar
quick-setting,
two-component glue)
in
breakable cap-
sules,
but
some experienced engineers will
not use
them,
because
the
strength
of the
anchor depends
so
much
on the
quality
of the field
work.
In
corrosive
environments,
use
extra-heavy
bolts,
or use
stainless
steel
or
nonferrous
material.
Inadequate
detailing. Show details
of
such ele-
ments
as
water stops, roof
flashing and
drainage, lou-
vers,
weather stripping, clearance around equipment,
and
provisions
to
guard against freezing. Detail roof
and
wall penetrations
for
adequate
clearance
between
engine exhaust pipes
and
combustible materials.
Ensure
that
the
work
of
structural, mechanical, electri-
cal, instrumentation,
and
architectural
disciplines
is
closely coordinated.
Differential
settlement between structure
and
exte-
rior
piping.
Be
sure that
the
exterior pipeline
has
enough
flexibility in its
joints adjacent
to the
wall
or
support
both
the
structure
and the
pipe
on
piles.
Always
use
wall sleeves. Because
of the
high proba-
bility
of
differential
settlement
or
frost
heave, inter-
rupt
plastic electrical conduit with metal conduit
through
exterior walls.
Foundation
problems. Obtain
the
services
of a
qualified
geotechnical engineer
and
adequately inves-
tigate
the
site. Include
field
borings
or
test pits (see
"Subsurface
Investigations"
in
Section 25-2
and
"Geotechnical
Considerations"
in
Section 25-10).
Inadequate
hatches. Make hatches large enough
(at
least
700 mm x 700 mm or 28 in. x 28
in.)
for a
worker
with
a
belt
of
tools
to
enter.
In
sewage
wet
wells,
allow
at
least
700 mm x 900 mm (28 in. x 36
in.)
for a
self-contained breathing apparatus
in a
back-
pack. Consider aluminum
checkerplate
with stainless-
steel hardware, positive latch openers,
and
inside grab
rails
for
easy access
to the
ladder
or
stairs.
Check
OSHA standards
for
hatches
and
their locations.
Level
floors
and, consequently, puddles. Slope
floors
at
least
1%
to a floor
drain
(2% is
better). Con-
crete
floors can be
cast level
if a
wearing slab
of
vari-
able thickness
is
applied later,
but
there
is
considerable
difficulty
in
obtaining
a
good bond.
Inadequate
monorails
or
cranes. Preferably,
arrange
the
station
to
provide monorails (for small sta-
tions)
or
cranes (for medium-sized
to
large stations)
above
all
heavy equipment,
and
make
it
easy
to set
heavy
items
on a
truck
in a
doorway. Consider motor-
izing
all
motions
for
cranes
and
hoists with capacities
greater than
680 kg
(
3
/
4
tons).
Use
slow speeds,
because pumping station operators
are
rarely
skilled
in
the
operation
of
hoisting equipment. Make access
hatches light (for easy
lifting)
and
large enough
to
remove equipment without dismantling
it. At the
very
least, small stations should have
lifting
eyes
for
porta-
ble
hoists (see Figure 25-2).
Inadequate
access
and
clearances. Allow enough
room
for the
removal (and replacement)
of
every
piece
of
equipment without disassembly
or
with mini-
mum
disassembly. Avoid cramped working areas
by
allowing
at
least
1.1 m (42
in.) around
all
equipment
(including
appurtenant piping)
for
heads, hands,
feet,
rumps,
wrenches,
and
lights
for
maintenance repairs
and
operations.
Carefully
draw plans
for
complicated
equipment such
as
engines
or
generators together with
all
attached auxiliary
or
appurtenant equipment
to
ensure that there
is
about
3 m (10 ft) of
clearance
for
ease
in
dismantling
for
repair.
Inadequate
strength,
stiffness,
and
watertightness.
Avoid
using
the
minimum design requirements
in the
ACI
318
Code. Heavier construction
is
required
so use
ACI
350
code.
Inadequate
ventilation
for
motor cooling. Provide
for
close coordination between mechanical
and
elec-
trical disciplines. Consider
air
conditioning, espe-
cially
if
noise must
be
suppressed.
Vibration.
Avoid resonance frequencies
by
sup-
porting pipes
at
frequent
intervals
and
using deep
beams
and
thick
floor
slabs. Isolate
diesel
engines
by
setting them
on
spring supports (see Chapter 22).
Wet
pit
atmosphere
seeping
into pump room. Com-
pletely sequester
wet
pits
from
the
pump room
so
that
neither
gas nor
sewage (even
if the wet
well over-
flows)
can
enter
the
pump room. Seal wires within
interconnecting conduits placed
at the
highest practi-
cal
elevation. Sump pumps should always discharge
above
the
highest
possible
water level
to a
sewer out-
side
the
pumping station.
27-11.
Specifications
Equipment
specifications
not to
code. Equipment
specified
by a
single named standard
or by
sole-
source
procurement must meet federal
and
state require-
ments.