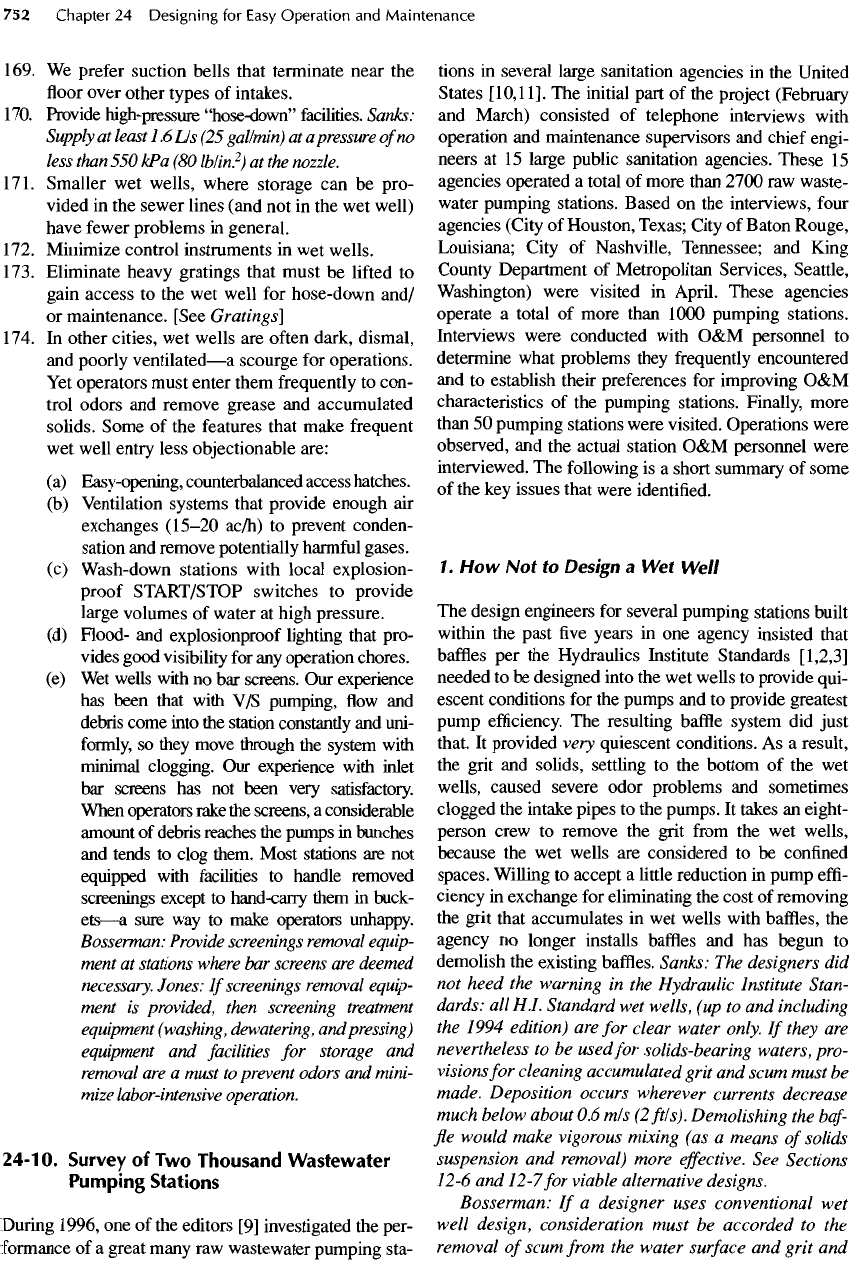
169.
We
prefer suction bells that terminate near
the
floor
over other types
of
intakes.
170. Provide high-pressure
"hose-down"
facilities.
Sanks:
Supply
at
least
1
.6
LIs (25
gallmin)
at a
pressure
of
no
less
than
550
kPa
(80
lblin?)
at the
nozzle.
111.
Smaller
wet
wells, where storage
can be
pro-
vided
in the
sewer lines (and
not in the wet
well)
have
fewer problems
in
general.
172. Minimize control instruments
in wet
wells.
173. Eliminate heavy gratings that must
be
lifted
to
gain access
to the wet
well
for
hose-down and/
or
maintenance. [See Gratings]
174.
In
other cities,
wet
wells
are
often
dark, dismal,
and
poorly
ventilated
—
a
scourge
for
operations.
Yet
operators must enter them frequently
to
con-
trol odors
and
remove
grease
and
accumulated
solids. Some
of the
features that make frequent
wet
well entry less objectionable are:
(a)
Easy-opening, counterbalanced access
hatches,
(b)
Ventilation systems that provide enough
air
exchanges
(15-20
ac/h)
to
prevent conden-
sation
and
remove potentially
harmful
gases,
(c)
Wash-down stations with
local
explosion-
proof START/STOP switches
to
provide
large volumes
of
water
at
high
pressure,
(d)
Rood-
and
explosionproof lighting that pro-
vides good visibility
for any
operation
chores,
(e)
Wet
wells with
no bar
screens.
Our
experience
has
been that with
V/S
pumping,
flow and
debris
come into
the
station constantly
and
uni-
formly,
so
they move through
the
system with
minimal
clogging.
Our
experience
with
inlet
bar
screens
has not
been very satisfactory.
When operators rake
the
screens,
a
considerable
amount
of
debris reaches
the
pumps
in
bunches
and
tends
to
clog them. Most stations
are not
equipped with facilities
to
handle removed
screenings except
to
hand-carry them
in
buck-
ets
—
a
sure
way to
make operators unhappy.
Bosserman:
Provide
screenings
removal
equip-
ment
at
stations
where
bar
screens
are
deemed
necessary.
Jones:
If
screenings
removal
equip-
ment
is
provided,
then
screening
treatment
equipment
(washing,
dewatering,
and
pressing)
equipment
and
facilities
for
storage
and
removal
are a
must
to
prevent
odors
and
mini-
mize
labor-intensive
operation.
24-10.
Survey
of Two
Thousand
Wastewater
Pumping
Stations
During 1996,
one of the
editors
[9]
investigated
the
per-
formance
of a
great many
raw
wastewater pumping sta-
tions
in
several large sanitation agencies
in the
United
States
[10,11].
The
initial part
of the
project (February
and
March) consisted
of
telephone interviews with
operation
and
maintenance supervisors
and
chief engi-
neers
at 15
large public sanitation agencies.
These
15
agencies operated
a
total
of
more than
2700
raw
waste-
water pumping stations. Based
on the
interviews,
four
agencies (City
of
Houston, Texas; City
of
Baton Rouge,
Louisiana; City
of
Nashville, Tennessee;
and
King
County
Department
of
Metropolitan Services, Seattle,
Washington) were visited
in
April.
These
agencies
operate
a
total
of
more than 1000 pumping stations.
Interviews were conducted with
O&M
personnel
to
determine what problems they frequently encountered
and
to
establish their preferences
for
improving
O&M
characteristics
of the
pumping stations. Finally, more
than
50
pumping stations were visited. Operations were
observed,
and the
actual station
O&M
personnel were
interviewed.
The
following
is a
short summary
of
some
of
the key
issues that were identified.
1.
How Not to
Design
a Wet
Well
The
design engineers
for
several pumping stations built
within
the
past
five
years
in one
agency insisted that
baffles
per the
Hydraulics Institute Standards
[1,2,3]
needed
to be
designed into
the wet
wells
to
provide qui-
escent conditions
for the
pumps
and to
provide greatest
pump
efficiency.
The
resulting
baffle
system
did
just
that.
It
provided
very
quiescent conditions.
As a
result,
the
grit
and
solids, settling
to the
bottom
of the wet
wells, caused severe odor problems
and
sometimes
clogged
the
intake
pipes
to the
pumps.
It
takes
an
eight-
person crew
to
remove
the
grit
from
the wet
wells,
because
the wet
wells
are
considered
to be
confined
spaces.
Willing
to
accept
a
little
reduction
in
pump
effi-
ciency
in
exchange
for
eliminating
the
cost
of
removing
the
grit that accumulates
in wet
wells with
baffles,
the
agency
no
longer installs
baffles
and has
begun
to
demolish
the
existing
baffles.
Sanks:
The
designers
did
not
heed
the
warning
in the
Hydraulic
Institute Stan-
dards:
all HJ.
Standard
wet
wells,
(up to and
including
the
1994 edition)
are for
clear water
only.
If
they
are
nevertheless
to be
used
for
solids-bearing waters, pro-
visions
for
cleaning accumulated grit
and
scum must
be
made.
Deposition occurs wherever currents decrease
much
below about
0.6
mis
(2ft/s).
Demolishing
the
baf-
fle
would
make vigorous mixing
(as a
means
of
solids
suspension
and
removal)
more
effective.
See
Sections
12-6
and
12-7
for
viable alternative designs.
Bosserman:
If a
designer uses conventional
wet
well
design, consideration must
be
accorded
to the
removal
of
scum from
the
water
surface
and
grit
and