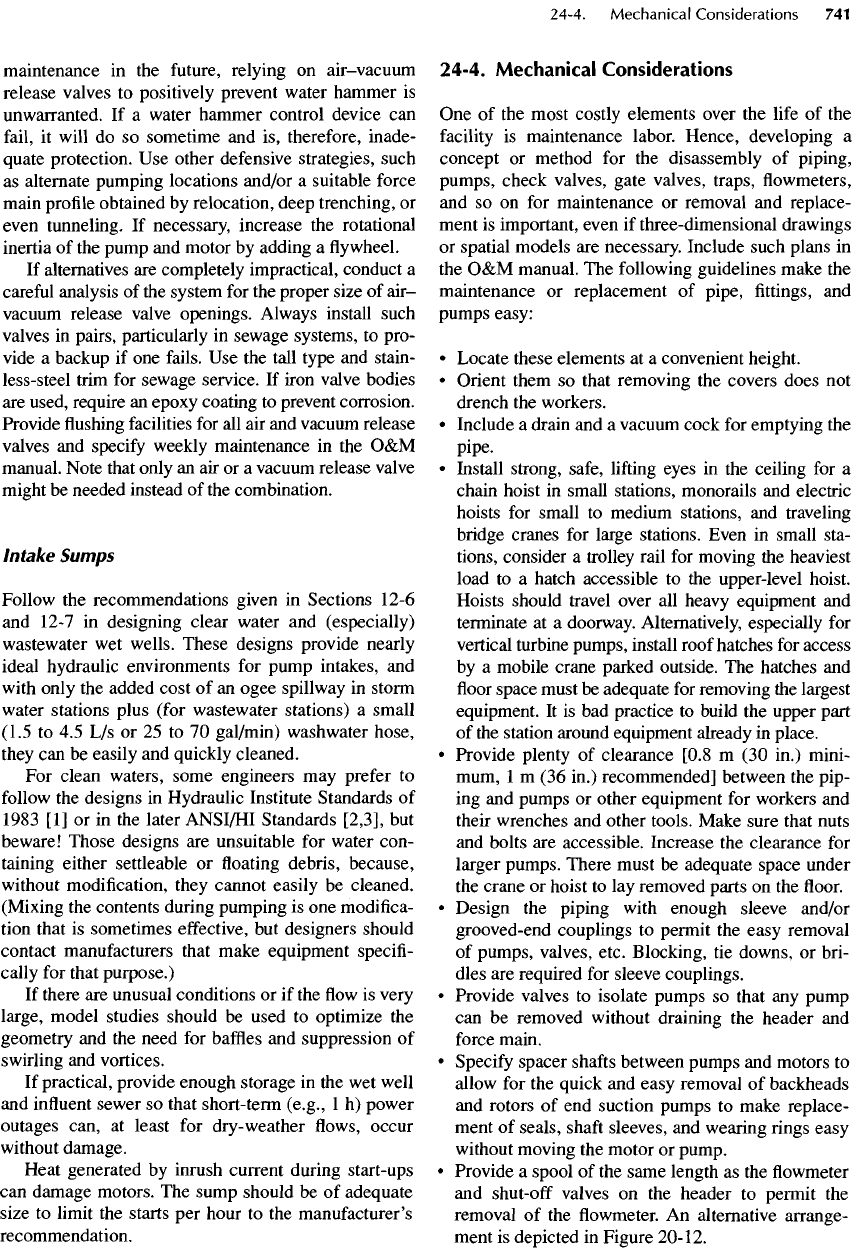
maintenance
in the
future,
relying
on
air-vacuum
release valves
to
positively prevent water hammer
is
unwarranted.
If a
water hammer control device
can
fail,
it
will
do so
sometime
and is,
therefore, inade-
quate
protection.
Use
other defensive strategies, such
as
alternate pumping locations and/or
a
suitable force
main
profile
obtained
by
relocation,
deep
trenching,
or
even tunneling.
If
necessary,
increase
the
rotational
inertia
of the
pump
and
motor
by
adding
a
flywheel.
If
alternatives
are
completely impractical, conduct
a
careful
analysis
of the
system
for the
proper size
of
air-
vacuum
release
valve openings. Always install such
valves
in
pairs, particularly
in
sewage systems,
to
pro-
vide
a
backup
if one
fails.
Use the
tall type
and
stain-
less-steel trim
for
sewage service.
If
iron valve bodies
are
used, require
an
epoxy coating
to
prevent corrosion.
Provide
flushing
facilities
for all air and
vacuum
release
valves
and
specify
weekly maintenance
in the O&M
manual.
Note that only
an air or a
vacuum release valve
might
be
needed instead
of the
combination.
Intake
Sumps
Follow
the
recommendations given
in
Sections 12-6
and
12-7
in
designing clear water
and
(especially)
wastewater
wet
wells. These designs provide nearly
ideal hydraulic environments
for
pump intakes,
and
with
only
the
added cost
of an
ogee spillway
in
storm
water stations plus (for wastewater stations)
a
small
(1.5
to 4.5 L/s or 25 to 70
gal/min)
wash
water hose,
they
can be
easily
and
quickly cleaned.
For
clean waters, some engineers
may
prefer
to
follow
the
designs
in
Hydraulic Institute Standards
of
1983
[1] or in the
later
ANSI/HI
Standards [2,3],
but
beware! Those designs
are
unsuitable
for
water con-
taining
either settleable
or floating
debris, because,
without
modification, they cannot easily
be
cleaned.
(Mixing
the
contents during pumping
is one
modifica-
tion
that
is
sometimes
effective,
but
designers should
contact manufacturers that make equipment
specifi-
cally
for
that purpose.)
If
there
are
unusual
conditions
or if the flow is
very
large, model studies should
be
used
to
optimize
the
geometry
and the
need
for
baffles
and
suppression
of
swirling
and
vortices.
If
practical, provide enough storage
in the wet
well
and
influent
sewer
so
that short-term (e.g.,
1 h)
power
outages
can,
at
least
for
dry-
weather
flows,
occur
without
damage.
Heat
generated
by
inrush current during start-ups
can
damage motors.
The
sump should
be of
adequate
size
to
limit
the
starts
per
hour
to the
manufacturer's
recommendation.
24-4. Mechanical Considerations
One of the
most costly elements over
the
life
of the
facility
is
maintenance labor. Hence, developing
a
concept
or
method
for the
disassembly
of
piping,
pumps,
check valves, gate valves, traps,
flowmeters,
and
so on for
maintenance
or
removal
and
replace-
ment
is
important, even
if
three-dimensional
drawings
or
spatial models
are
necessary. Include such plans
in
the O&M
manual.
The
following guidelines make
the
maintenance
or
replacement
of
pipe,
fittings, and
pumps
easy:
•
Locate these elements
at a
convenient height.
•
Orient them
so
that removing
the
covers does
not
drench
the
workers.
•
Include
a
drain
and a
vacuum cock
for
emptying
the
pipe.
•
Install strong,
safe,
lifting
eyes
in the
ceiling
for a
chain hoist
in
small stations, monorails
and
electric
hoists
for
small
to
medium stations,
and
traveling
bridge cranes
for
large stations. Even
in
small sta-
tions, consider
a
trolley rail
for
moving
the
heaviest
load
to a
hatch accessible
to the
upper-level hoist.
Hoists should travel over
all
heavy equipment
and
terminate
at a
doorway. Alternatively, especially
for
vertical turbine pumps, install roof hatches
for
access
by
a
mobile crane parked outside.
The
hatches
and
floor
space must
be
adequate
for
removing
the
largest
equipment.
It is bad
practice
to
build
the
upper part
of
the
station around equipment already
in
place.
•
Provide plenty
of
clearance [0.8
m (30
in.) mini-
mum,
1 m (36
in.) recommended] between
the
pip-
ing and
pumps
or
other equipment
for
workers
and
their wrenches
and
other tools. Make sure that nuts
and
bolts
are
accessible. Increase
the
clearance
for
larger pumps. There must
be
adequate space under
the
crane
or
hoist
to lay
removed parts
on the floor.
•
Design
the
piping with enough sleeve and/or
grooved-end couplings
to
permit
the
easy removal
of
pumps, valves, etc. Blocking,
tie
downs,
or
bri-
dles
are
required
for
sleeve couplings.
•
Provide valves
to
isolate pumps
so
that
any
pump
can be
removed without draining
the
header
and
force
main.
•
Specify
spacer
shafts
between pumps
and
motors
to
allow
for the
quick
and
easy removal
of
backheads
and
rotors
of end
suction pumps
to
make replace-
ment
of
seals,
shaft
sleeves,
and
wearing
rings
easy
without
moving
the
motor
or
pump.
•
Provide
a
spool
of the
same length
as the flowmeter
and
shut-off
valves
on the
header
to
permit
the
removal
of the flowmeter. An
alternative arrange-
ment
is
depicted
in
Figure
20-12.