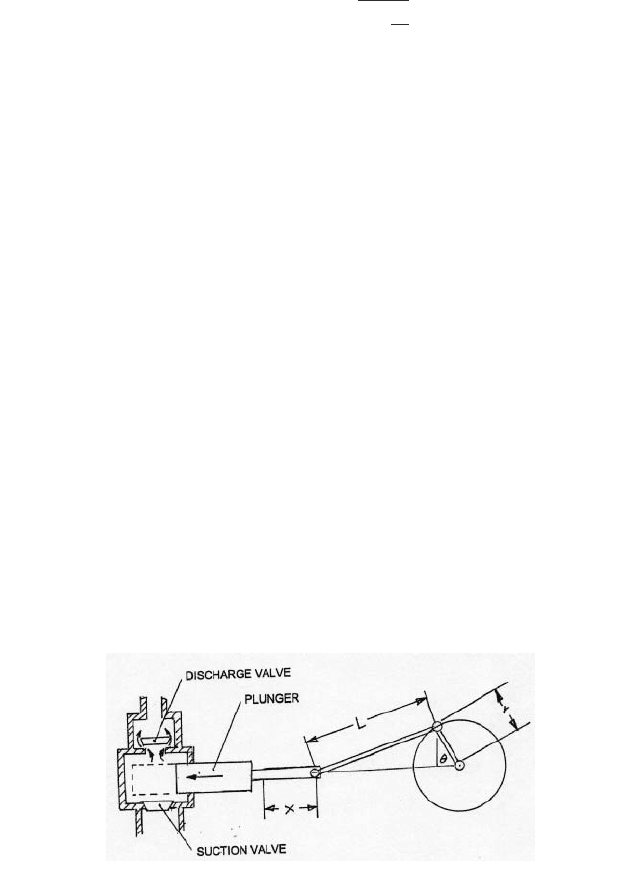
3.10 CHAPTER THREE
FIGURE 5 Slider-crank mechanism
FLUID END THEORY __________________________________________________
Pumping Cycle
Unlike the relatively smooth, continuous flow of fluid through a cen-
trifugal pump, the flow of fluid through a power pump occurs in a transitory dynamic con-
dition called a pumping cycle. The event that initiates this cycle is the linear movement
of the plunger or piston. In Figure 5, r is the radius of the crank in feet (meters), L is the
length of the connecting rod in feet (meters), C equals L / r, and v equals (2p / 60) rpm.
Thus, X , the linear movement of the piston or plunger is
As the plunger (or piston) withdraws from the fluid cylinder or pumping chamber, the
volume of the cylinder increases.The pressure in the cylinder decreases in response to the
increased volume. Since most of the fluids handled by power pumps are relatively incom-
pressible, very little plunger movement is required to cause a pressure drop. When the
cylinder pressure drops sufficiently below suction pressure, the differential pressure
begins to open the suction valve. The valve opens gradually and smoothly at the start of
the suction stroke because the velocity and acceleration of the plunger are small.
Fluid flows through the suction valve assembly, following the plunger and filling the
cylinder. As the plunger decelerates at the end of the suction stroke, the suction valve
gradually returns to its seat. Ideally, the suction valve is completely closed as the plunger
comes to a stop.
The motion of the slider-crank mechanism causes the plunger to reverse direction and
start its discharge stroke. The fluid trapped in the fluid cylinder is compressed until the
cylinder pressure exceeds the discharge pressure by an amount sufficient to begin to open
the discharge valve.As with the suction valve, the discharge valve continues to open until
it reaches its travel limit or until the velocity of fluid through the valve becomes constant.
As the plunger decelerates, the valve moves back toward its seat. Again, ideally, the dis-
charge valve closes when the motion of the plunger stops.
The number of pumping cycles in a single revolution of the crankshaft is the same as
the number of cylinders in the pump. Every cylinder will “pump” in a sequence determined
by the “firing order” of the crankshaft. The cylinders are arranged in parallel, with each
one discharging into a common discharge manifold. In industry terms, the pump is usually
identified by the number of plungers or pistons on the crankshaft. They are the same for
single- or double-acting pumps (see Table 7).
Pulsations The pulsating characteristics of the fluid flowing into and out of power
pumps are significantly influenced by the number of plungers or pistons. Discharge flow
pulsations are the most critical because of the high energy potential generated when the
system resistance reacts with the flow to create pressure. Since the magnitude of the dis-
charge pulsation is mostly affected by the number of cylinders, increasing the number of
cylinders will reduce the flow pulsations.
X r c1 cos u L a1
B
1
r
2
L
2
1sin u2
2
bd