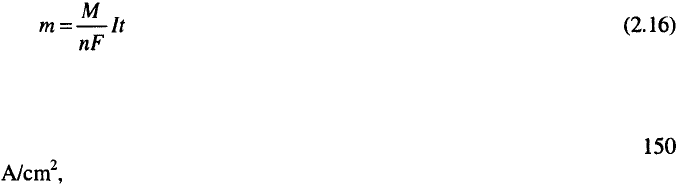
236
Chapter 9
where M is the atomic mass of the metal, n is the number of electrons, F is
the Faraday’s constant, I is the current and t is the time. The average current
densities depend on metal, and their values are usually between 50 and
while the voltage is about 10 to 20 V. Typical tolerances of about
0.127 mm are reported, however, under special circumstances they can
achieve 0.013 mm, or even 0.002 mm under pulsating current conditions.
63
During the electromachining the formation of surface oxide films
frequently occurs. To break the oxide film, higher voltages should be
applied. Due to oxygen evolution reaction at the anode the gas bubbles
rupture the oxide film causing localized pitting. The process variables can
significantly influence the surface finish. The smoother surface finish is
generally observed with higher current densities or with higher velocities of
the electrolyte.
Electrochemical machining processes have various applications such as
smoothing of rough surfaces, hole drilling, full form shaping, electrochemical
grinding, electrochemical arc machining, biomedical engineering etc.
64-67
9.8 ELECTROCHEMICAL OXIDATION OF METALS
Electrochemical oxidation of metals is an anodic process in which thin
oxide films are produced. These oxide films may have different color and
attractive physico-chemical properties. Color and other properties of
anodically produced oxide films are determined by the conditions of
electrochemical oxidation, which include composition of the electrolyte,
temperature, current density, voltage and duration of the process.
Thin oxide films can be produced anodically on many metals. Metals of
interest include so-called “valve” metals (i.e., metals such as aluminum,
tantalum, niobium, titanium, zirconium etc., which form adherent electrically
insulating anodic films,). At the present, this process is commercially applied
only to aluminum. Anodic oxidation of aluminum is often called
“anodizing”. Oxide films produced on aluminum surfaces as a consequence
of anodizing, have a very good hardness, abrasion- and corrosion-
resistances and unique columnar and porous structure.
Applications of anodized aluminum include protection against corrosion
and abrasion, decorative surfaces which provide color and base for paints
etc. These anodized surfaces are used in aggressive environments, permanent
external and architectural constructions, automotive, aircraft and electronics
industries.