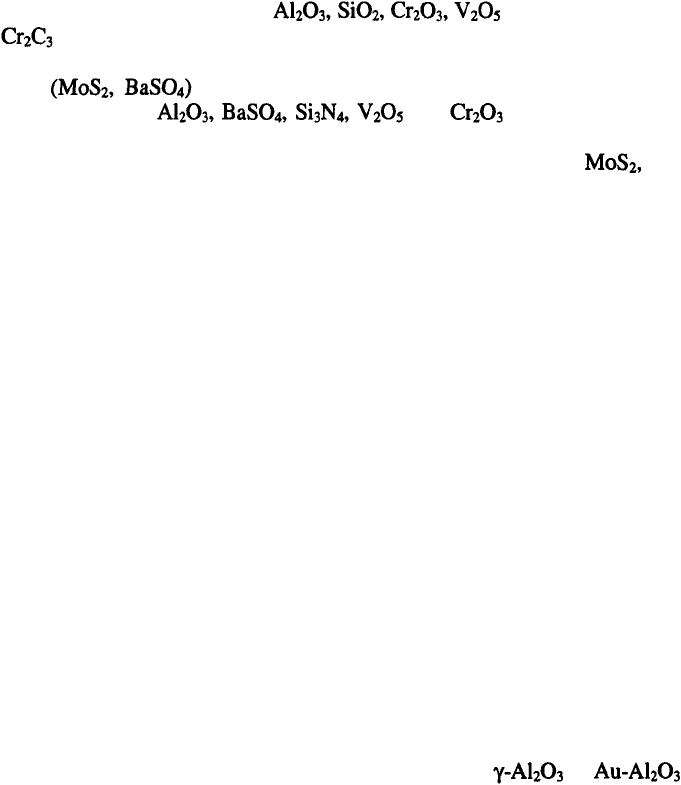
9. Electroplating and Surface Finishing
211
and tribological properties, although other characteristics such as corrosion
and thermal resistance can also be significantly advanced.
The metal matrices may include nickel, cobalt, copper, zinc, precious
metals and related alloys. Solid (inert) particles, which are incorporated into
metal deposit, include oxides ( etc.), carbides (SiC,
), graphite, diamond or boron nitride particles, polymer powders
(polytetrafluorethylene, polyvinyl chloride) and other components such as
salts or some pigments. The incorporation of submicron
powders such as and in the nickel-based
metallic matrices significantly increases the corrosion resistance. Particulates
like WC, diamond and SiC protect metal from abrasion, while and
polytetrafluorethylene (PTFE) and graphite reduce the friction coefficient of
the composite materials.
For deposition of composite materials with metallic matrices, solutions
similar to those in the electrodeposition of metals and alloys are used. The
main difference is that solutions used in the electrodeposition of composite
materials contain dispersed fine particles or fibres. Codeposition of inert
particles into metal matrix is influenced by the adsorption of particles on the
cathode. The content of particles in the deposit is influenced by their
concentration in solution, additives, pH and current density. Most of the
studies show that the content of deposited particles in the metal matrix
increases with increasing particle concentration in the solution. In terms of
particle size, different results have been reported for the same systems.
Additives, such as brightners or wetting agents, influence codeposition of
inert particles. Quite opposite observations on the effect of brightners or
wetting agents on the amount of solid particles occluded into deposit were
reported. In some cases, in the presence of these substances, an increase in
the amount of particles is observed. Other researchers, in contrast reported a
decrease in the particle content with an addition of wetting agents.
Current density significantly influences the codeposition of particles.
Although, some researchers reported no influence of current density on the
amount of particles deposited, most commonly, the observed dependence of
current density on the particle concentration passes through one or several
maximums. Typical examples are presented in Figures 9.6 and 9.7. As
shown in Figure 9.6, the dependence of the amount of
in
deposit on current density, passes through two maximums for different
rotation speeds.
17
Similar dependencies of the amount of SiC in the Co-SiC deposit on
current density, for different concentrations of SiC in the solution are
presented in Figure 9.7.
18
A presence of particles in the plating solution
increases the current density for the same cathodic potential. This indicates
that the presence of particles in the solution causes a depolarization of the
cathode.