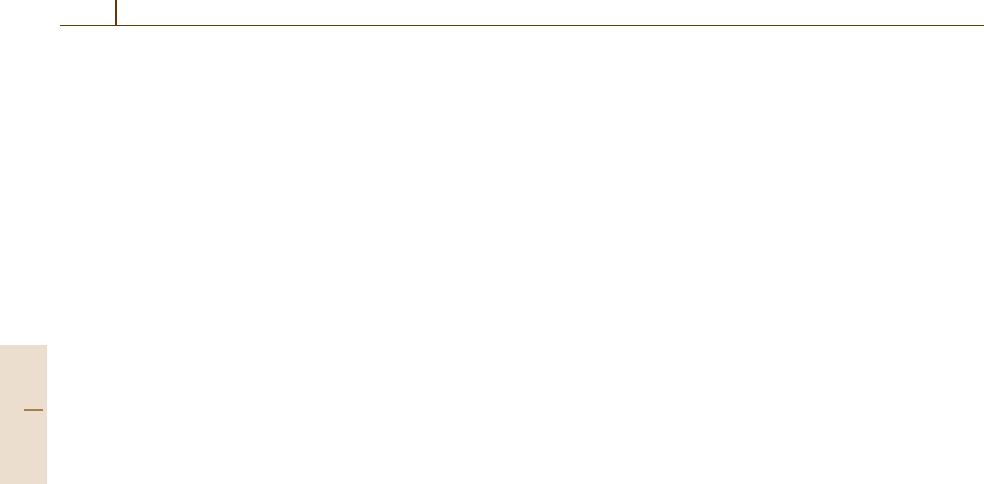
1024 Part F Industrial Automation
weight profile at the end of the paper machine. Some
basic constraints for the implementation of statistical
process (quality) control in paper industry are given
in [58.12], e.g.,
this assumes that all of the important variables are
measured in a timely manner ... Another point to
consider is the sampling frequency. Generally, the
more variability in a material, the more often it
should be sampled.
Blatzheim gave an example of the benefit of such
system: 15–16km of waste material reduction was
achieved after implementing this system, corresponding
to an approximate increase of 200 000 of sellable paper
per year.
Laukkanen mentioned OTS and appropriate work-
flow guidelines as being one of the keys to reduce
commissioning and start-up, especially abroad [58.3].
Through the engineering life cycle, depending
on the project phase, different tools and methods
are used. In the worst case, the corresponding data
have to be re-entered during the transition from one
phase to the next because there are no appropri-
ate interfaces between the individual tools. The ideal
is to strive for a higher-level tool that consistently
provides all system information in a model and en-
ables the design to be realized both at an abstract
level and in a conventional environment (e.g., electri-
cal engineering computer aided engineering (E-CAE),
IEC 61131-3).
58.3 Emerging Trends, Open Challenges
There are many open challenges in the timber and paper
industries. Some will be discussed in this section, i.e.,
engineering lifecycle and data integration, reduction
of complexity for operators, improvement of operator
training, as well as evaluation of new technologies.
Open challenges are to increase engineering ef-
ficiency while reducing costs and start-up time by
applying modularity andreuse. Communicationis a ma-
jor factor to consider when improving engineering
quality because different disciplines such as sales, tech-
nology, mechanical engineering (including hydraulic),
electrical engineering, and computer science are in-
volved through different phases in the engineering
process. Communication could be supported by a com-
prehensive model. Unfortunately modeling of hybrid
systems in process automation is still a field for
research and development, especially for reuse and
modularity, and when the target group is engineers
or technicians coming from different disciplines. One
promising approach is to apply a comprehensive mod-
eling notation such as the systems modeling language
(SysML) [58.19] that is based on the unified modeling
language (UML) and developed for systems engineer-
ing. This basically solves the deficiencies of UML for
automation, i.e., modeling of hardware aspects, inte-
gration, and tracking of requirements. The advantage
of UML in terms of supporting modularity through an
object-oriented mechanism is fully available. The task
is to evaluate SysML in terms of ease of application by
engineers and technicians in automation depending on
the availability of strong tools. One of the first steps
to integrate modeling into IEC 61131-3 is already in
progress in a research and development (R&D) project
in Germany. Various UML diagrams are implemented
in one of the market leading IEC 61131-3 tools [58.20].
Presenting the modules throughout the engineering life
cycle from customers’ requirements to operation is still
not solved and will not only be a task for research
but also for the development department of leading au-
tomation companies. Plant manufacturing companies
need an easy way to evaluate whether a new plant con-
cept could be realized by reusing existing modules or
to determine the number of new modules that need
to be developed. Data integration throughout the en-
gineering life cycle is theoretically solved but still far
away from realization in the applied tools. Coupling of
computer-aided engineering (CAE) system on the basis
of a tool-to-tool interface is not sufficient for the two
considered industries.
There is also huge potential for cost saving during
start-up by integrating engineering data into an ERP
system, and offshoring in a global market. Additional
elaboration on logistics, e.g., just-in-time machine or
component to site, is needed. Today mainly mechan-
ical construction has been subject to offshoring. This
will change during the next few years. A lot of chal-
lenges for the engineering workflow will consequently
be affected.
Operation and maintenance, which is challenging
to improve, is also a very important phase in the en-
gineering life cycle. Application of three-dimensional
(3-D) visualization can successfully reduce complexity
Part F 58.3