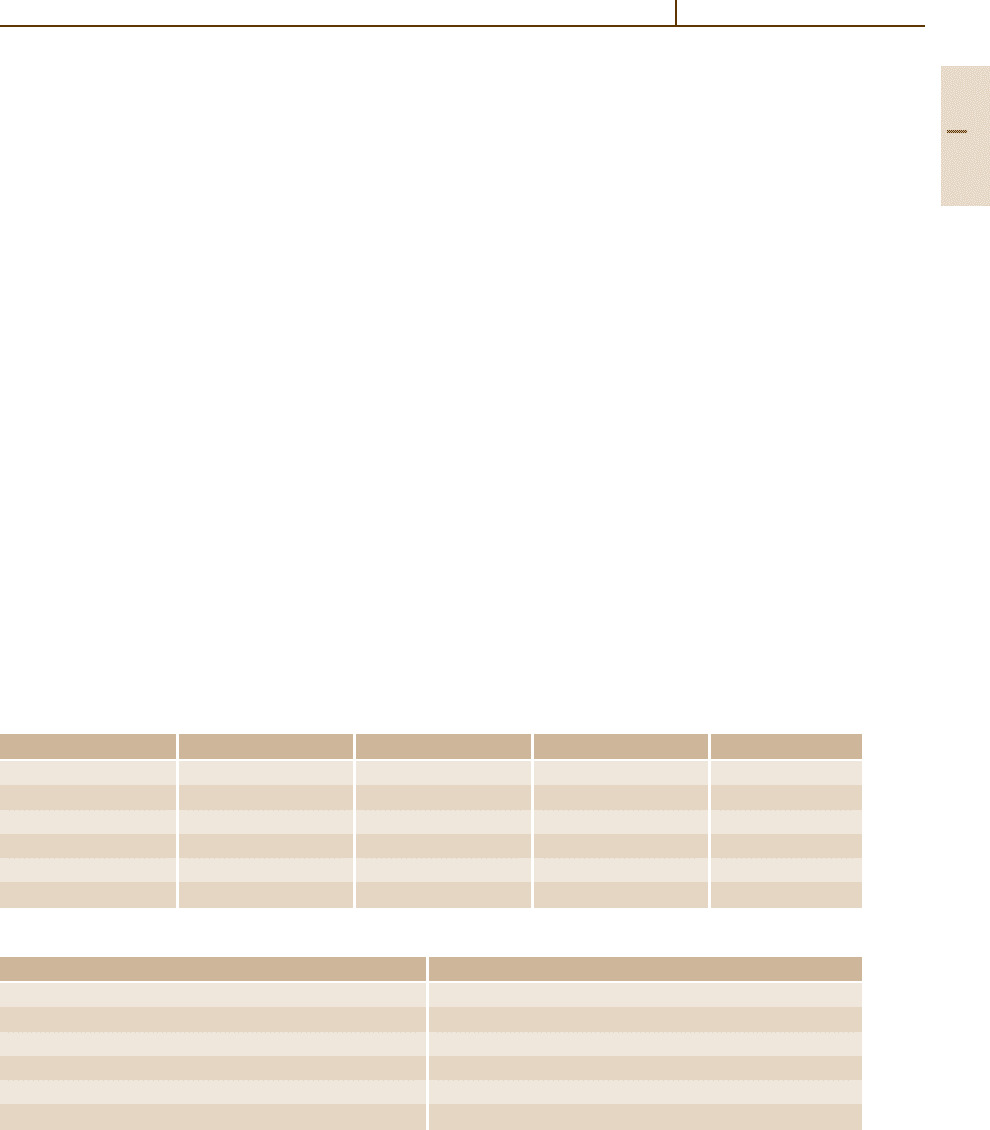
Metals 1.3 Titanium and Titanium Alloys 213
Chemical Properties. The oxidation resistance of the
Ti
3
Al-based alloys is higher than that of conventional
Ti alloys with TiO
2
formation, but lower than that of
Al
2
O
3
-forming alloys. The rate controlling mechanisms
are complex and change with atmosphere, temperature,
and time. Oxidation is moderate with porous scales up to
800
◦
C whereas spallation occurs athigher temperatures.
The addition of Nbto the Ti
3
Al-based alloys isbeneficial
to the oxidation resistance as well as nitrogen in the
atmosphere [1.58]. Table 3.1-27 presents characteristic
data for oxidation at 800
◦
C.
It should be noted that H is easily dissolved in
Ti
3
Al-based alloys, leading to embrittlement and stress
corrosion cracking. Furthermore, the thermal stability
of intermetallic Ti
3
Al-based matrix composites – in
particular SCS-6 SiC/Ti-25Al-10Nb-3V-1Mo – is af-
fected by chemical reactions between the matrix and the
strengthening phase.
TiAl-Based Alloys
Alloys based on γ -TiAl, also called gamma titanium
aluminides, excel due to their high strength per unit
density. These alloys contain the α
2
-phase Ti
3
Al as
a second phase and are further alloyed with other elem-
ents for property optimization. The composition range
is Ti-(45–48)Al-(0–2)(Cr, Mn, V)-(0–5)(Nb, Ta, W)-(0–
2)(Si, B, Fe, N) (at.%). Further components such as Hf,
Table 3.1-27 Characteristic oxidation data for various Ti
3
Al-based alloys at 800
◦
C. Apparent parabolic rate constant k
p
and apparent activation energy Q [1.58]
Alloy (at.%) Atmosphere Test duration (h) k
p
(10
−12
g
2
cm
−4
s
−1
) Q (kJ mol
−1
)
Ti-25Al O
2
9 19 289
Ti-25Al-11Nb O
2
4 2.0 330
Ti-24Al-15Nb O
2
6 2.2 329
Ti-24Al-15Nb 20% O
2
+ 80% N
2
5 0.25 274
Ti-24Al-10Nb-3V-1Mo 20% O
2
+ 80% N
2
15 1150 217
Ti-25Al-10Nb-3V-1Mo Air 24 2.4 248
Table 3.1-28 Standard microstructures of TiAl-based alloys [1.59]
Type Phase distribution
Near-gamma (NG) γ grains + α
2
particles
Duplex (DP) γ grains + α
2
plates or particles
Nearly lamellar (NL) Lamellar γ +γ grains
Fully lamellar (FL) Lamellar γ + residual γ grains on grain boundaries
Modified NL (MNL) Lamellar γ + fine γ grains
Modified FL (MFL) Lamellar γ
Sn, C, and/or 0.8–7vol.%TiB
2
are added for dispersion
strengthening [1.59]. Table 3.1-28 shows the standard
microstructures and Table 3.1-29 lists the alloys of
primary interest.
Various jet engine and car engine components have
been identified for application of TiAl-based alloys. It
is particularly noteworthy that large sheets, which are
suitable for superplastic forming and joining by diffu-
sion bonding, can be produced from these intrinsically
brittle intermetallic compound alloys.
Physical Properties. Some thermal data for single crys-
talline and polycrystalline TiAl alloys are shown in
Tables 3.1-30 and 3.1-31.
Mechanical Properties. Elastic properties of TiAl-based
materials are compiled in Table 3.1-32. Strength, ductil-
ity, and toughness of the TiAl-based alloys are sensitive
functions of both composition and microstructure which
is controlled by prior processing [1.59]. Characteris-
tic data are shown in Table 3.1-33 for various alloys.
Different property data for the same alloy composition
indicate the effect of different prior thermo-mechanical
treatments. It is noted that TiAl-based alloys are prone
to hydrogen/environmental embrittlement depending on
the amount of α
2
from Ti
3
Al [1.60]. Creep and fatigue
data are available [1.59, 61].
Part 3 1.3