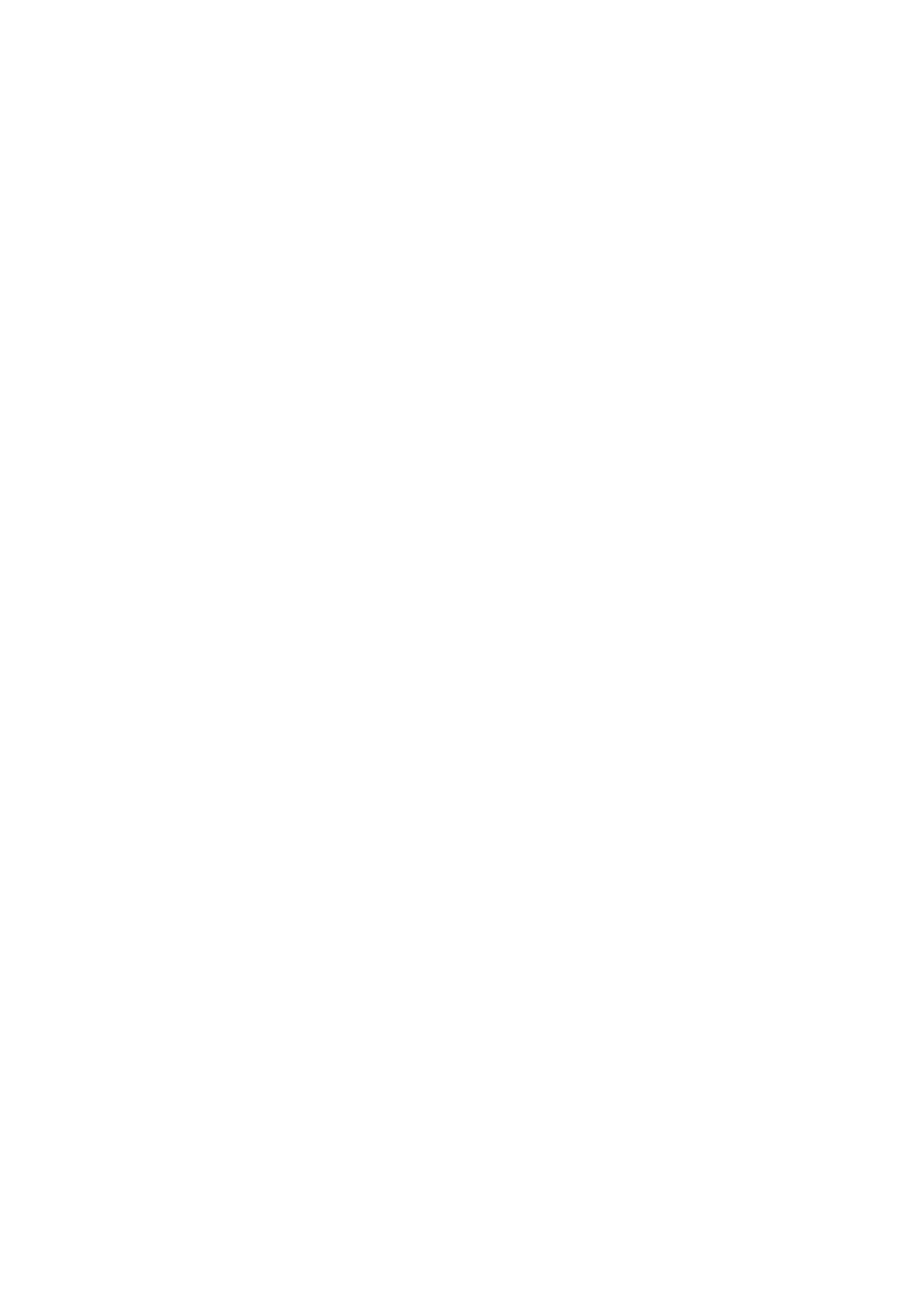
133
В стали 50X13Г8 при повышении температуры нагрева под закалку с 900 до 1200
о
С прочностные
характеристики изменяются по кривой с максимумом, а относительное удлинение и ударная вязкость
возрастают, относительное поперечное сужение уменьшается. Наибольшие значения предела текучести в
исследованных хромомарганцевых аустенитных сталях достигаются при мелком зерне и повышенной
стабильности аустенита к образованию мартенситных фаз при малых напряжениях. Получение
максимального предела прочности, характеристик пластичности и ударной вязкости обусловлено
благоприятным развитием мартенситного превращения при испытании механических свойств. В
исследованных аустенитных сталях целесообразно проводить закалку с 1000–1100
o
С, что обеспечивает
растворение карбидов по границам зерен, еще не вызывает сильный их рост и позволяет получить
хорошее сочетание прочностных и пластических свойств.
Изучалось также влияние условий охлаждения (в воде, масле, на воздухе, в печи) с температуры
1000
o
С на фазовый состав и стабильность остаточного аустенита в сталях Fе – 0,1 % С – 14 % Сr,
содержащих 2–8 % Mn [204-206]. Общая зависимость количества γ
ост
от содержания марганца в сталях
сохраняется. Охлаждение в воде, масле, на воздухе незначительно влияет на фазовый состав и твердость
сталей. При охлаждении с печью в сталях, содержащих 2–8 % Mn, увеличивается на 5–10 % количество
остаточного аустенита и на HRC 2-3 снижается твердость в сравнении с закалкой в масло [206], что
объясняется стабилизацией аустенита при замедленном охлаждении. Последнее может быть связано с
уменьшением уровня внутренних напряжений и закреплением дислокаций примесными атомами.
Обнаруживается также повышение стабильности остаточного аустенита при деформации по мере
уменьшения скорости охлаждения. Так в 10Х14АГ6МФ, закаленной в воде, деформация прокаткой на
15 % вызвала полный распад остаточного аустенита с образованием мартенсита. После нормализации и
отпуска такая же деформация еще сохраняет остаточный аустенит. После отпуска хромомарганцевые
стали, содержащие 4–6 % Mn, характеризуются высокой пластичностью (δ = 14–20 %), но при этом
прочностные свойства ниже, чем после закалки и нормализации. Высокий уровень механических свойств
может быть достигнут после нормализации: σ
0,2
= 1180 MПa, σ
В
= 1510 MПa, δ = 8 %, ψ = 14 %, КСU =
0,8 МДж/м
2
(10Х14АГ6Д2М) [206]. Возможность получения хорошего сочетания свойств даже после
замедленного охлаждения (на воздухе или в печи) является важной особенностью рассмотренных сталей.
На сталях, содержащих 0,1 % С и от 0 до 8 % Mn, а также 10Х14АГ6, 10XI4AГ6M, 10Х14АГ6Д2
изучено влияние ступенчатой закалки после аустенитизации при 1000
о
С с выдержками при
температурах 100–400°
о
С в течение 0,5–5 ч. Выдержка 0,5–1 ч при температурах 100 и 400
o
С
увеличивает количество остаточного аустенита и его стабильность [204]. Повышение
продолжительности выдержки от 1 до 5 ч при температурах 300–400
o
С в сталях с 6–8 % Мn уменьшает
количество остаточного аустенита практически до нуля. Такое неоднозначное влияние выдержки
обусловлено тем, что при относительно небольшой ее продолжительности происходит закрепление
дислокаций примесными атомами, снижается уровень внутренних напряжений, что стабилизирует
аустенит, Напротив, продолжительные выдержки его дестабилизируют за счет выделения карбидов. В
стали 10Х14 мартенситного класса повышение температуры изотермической выдержки от 100 до
400
o
С 1 ч вызывает увеличение прочностных и пластических характеристик [204]. В случае
наибольшего содержания в структуре остаточного аустенита (27 %) в 10X14 достигнут высокий
комплекс свойств: σ
0,2
= 1240 МПа, σ
В
= 1430 МПа, δ = 11 %, ψ = 36 %, КСU = 1,0 МДж/м
2
, что
обусловлено развитием мартенситного превращения при испытаниях, а также получением более
дисперсного мартенсита. После ступенчатой закалки сталей 10Х14АГ6, 10Х14АГ6Д2, 10Х14АГ6М в них
может быть получен следующий уровень свойств: σ
0,2
= 1150–1260 МПа, σ
В
= 1470-1720 МПа, δ = 11–
14 %, ψ = 22–38 %, KCU = 1,0-1,6 МДж/м
2
. Эти результаты представляют несомненный интерес в связи с
тем, что показывают новые возможности получения остаточного аустенита и регулирования его
стабильности в высокохромистых и хромомарганцевых сталях за счет ступенчатой закалки. Обычно она
применяется в практике термообработки лишь для низколегированных сталей с целью уменьшения
внутренних напряжений. В данном случае стабилизация аустенита, имеющая место при ступенчатой
закалке, является полезной, а не вредной, как это обычно принято считать.
В работе [207] изучено влияние отпуска (старения) в сталях различных структурных классов:
мартенситно–ферритного - 10X14, мартенситного - 10Х14Г2, переходного - 10Х14Г(4-8), 10Х14АГ6,
10Х14АГ6МФ, 10Х14АГ6Д2, 10Х14АГ6ДМ, 10Х14АГ6ДМФ, а также аустенитного -
06Х10АГ8М2Д2ФС, 08Х10АГ8МД2ФС, 10Х10АГ8МД2ФС, 20Х13АГ12МД2ФС, 30Х10АГ8М3Д2ФС.
Рассмотрим вначале влияние отпуска на структуру, стабильность остаточного аустенита и свойства
сталей переходного класса. Низкий отпуск в интервале 200–300
o
С практически не оказывает влияния на
количество α′–фазы, однако снижает твердость с HRC 36–38 до HRC 33–35. Отпуск при 400
o
С вызывает
старение мартенсита, сопровождающееся увеличением твердости на HRC 3–5. При нагреве на 500–